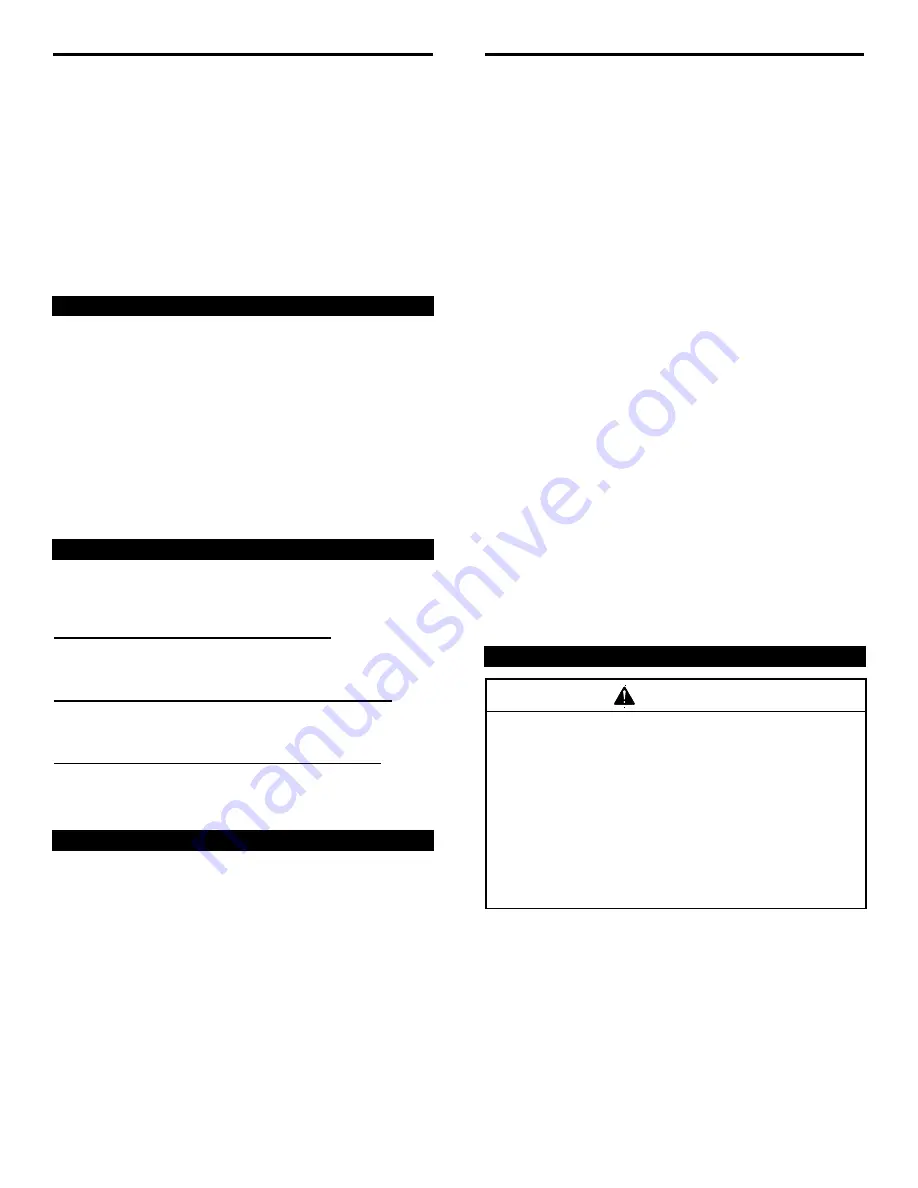
PREFACE
MAINTENANCE
III
•
ALWAYS shut off compressor and depressurize blast
machine BEFORE doing ANY maintenance.
•
Always check and clean ALL filters, screens and alarm
systems when doing any maintenance.
•
ALWAYS cage springs BEFORE disassembling valves IF
spring-loaded abrasive control valves are used.
•
ALWAYS completely follow owner's manual instructions
and maintain equipment at RECOMMENDED intervals.
ADDITIONAL ASSISTANCE
•
Training and Educational Programs.
Clemco Industries Corp. offers a booklet, Blast-Off 2,
developed to educate personnel on abrasive blast equipment
function and surface preparation techniques. Readers will learn
safe and productive use of machines, components and various
accessories, including selection of abrasive materials for
specific surface profiles and degrees of cleanliness.
•
The Society for Protective Coatings (SSPC) offers a video
training series on protective coatings including one entitled
"Surface Preparation." For loan or purchase information,
contact SSPC at the address shown below.
TECHNICAL DATA AND RESEARCH COMMITTEES
•
The following associations offer information, materials and
videos relating to abrasive blasting and safe operating
practices.
The Society for Protective Coatings (SSPC)
40 24th Street, Pittsburgh PA 15222-4643
Phone: (412) 281-2331 • FAX (412) 281-9992
Email: [email protected] • Website: www.sspc.org
National Association of Corrosion Engineers (NACE)
1440 South Creek Drive, Houston TX 77084
Phone: (281) 228-6200 • FAX (281) 228-6300
Email: [email protected] • Website: www.nace.org
American Society for Testing and Materials (ASTM)
100 Barr Harbor Dr., West Conshohocken, PA 19428
Phone (610) 832-9500 • FAX (610) 832-9555
Email: [email protected] • Website: www.astm.org
NOTICE
This equipment is not intended to be used in an area that might
be considered a hazardous location as described in the
National Electric Code NFPA 70 1996, article 500.
WARRANTY
The following is in lieu of all warranties express, implied or
statutory and in no event shall seller or its agents, successors,
nominees or assignees, or either, be liable for special or
consequential damage arising out of a breach of warranty. This
warranty does not apply to any damage or defect resulting from
negligent or improper assembly or use of any item by the buyer
or its agent or from alteration or attempted repair by any person
other than an authorized agent of seller. All used, repaired,
modified or altered items are purchased “as is” and with all
faults. In no event shall seller be liable for consequential or
incidental damages. The sole and exclusive remedy of buyer
for breach of warranty by seller shall be repair or replacement
of defective parts or, at seller’s option, refund of the purchase
price, as set forth below:
1. Seller makes no warranty with respect to products used
other than in accordance hereunder.
2. On products seller manufactures, seller warrants that all
products are to be free from defects in workmanship and
materials for a period of one year from date of shipment to
buyer, but no warranty is made that the products are fit for a
particular purpose.
3. On products which seller buys and resells pursuant to this
order, seller warrants that the products shall carry the then
standard warranties of the manufacturers thereof, a copy of
which shall be made available to customer upon request.
4. The use of any sample or model in connection with this order
is for illustrative purposes only and is not to be construed as a
warranty that the product will conform to the sample or model.
5. Seller makes no warranty that the products are delivered
free of the rightful claim of any third party by way of patent
infringement or the like.
6. This warranty is conditioned upon seller’s receipt within ten
(10) days after a buyer’s discovery of a defect, of a written
notice stating in what specific material respects the product
failed to meet this warranty. If such notice is timely given, seller
will, at its option, either modify the product or part to correct the
defect, replace the product or part with complying products or
parts, or refund the amount paid for the defective product, any
one of which will constitute the sole liability of seller and a full
settlement of all claims. No allowance will be made for
alterations or repairs made by other than those authorized by
seller without the prior written consent of seller. Buyer shall
afford seller prompt and reasonable opportunity to inspect the
products for which any claim is made as above stated.
Except as expressly set forth above, all warranties, express,
implied or statutory, including implied warranty of
merchantability, are hereby disclaimed.
DAILY SET-UP CHECK LIST
WARNING
•
ALL
piping, fittings and hoses MUST be checked
DAILY for tightness and leakage.
•
ALL
equipment and components MUST be thoroughly
checked for wear.
•
ALL
worn or suspicious parts MUST be replaced.
•
ALL
blast operators MUST be properly trained to
operate equipment.
•
ALL
blast operators MUST be properly outfitted with
abrasive resistant clothing, safety shoes, leather gloves
and ear protection.
•
BEFORE
blasting ALWAYS use the following check list.
□
1. PROPERLY MAINTAINED AIR COMPRESSOR
sized
to provide sufficient volume (cfm) for nozzle and other tools
PLUS a 50% reserve to allow for nozzle wear. Use large
compressor outlet and large air hose (4 times the nozzle orifice
size). FOLLOW MANUFACTURERS MAINTENANCE
INSTRUCTIONS.
□
2. BREATHING AIR COMPRESSOR
(oil-less air pump)
capable of providing Grade D Quality air located in a dust free,
contaminant free area. If oil-lubricated air compressor is used
to supply respirator, it should have high temperature monitor