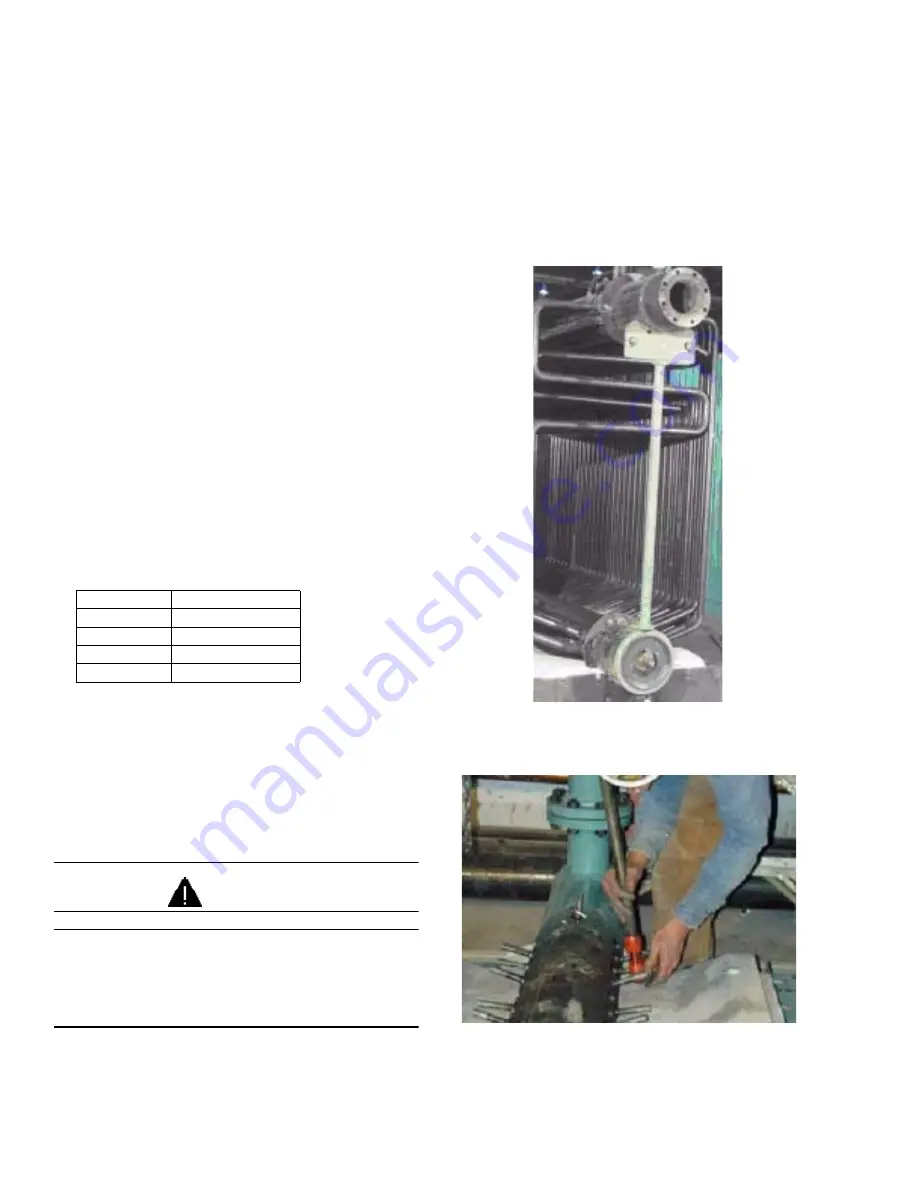
Pressure Vessel Assembly
Model FLE Assembly
2-4
750-192
5. Upper Drum Placement
Using appropriately sized lifting devices, place the
upper drum in position above the downcomer and
lower drum. Apply sealant to the downcomer gasket
and position the gasket between the flanges. Using
the studs provided, secure the flanges and/or front
spreader bar. Apply “Never-Seez” to all flange studs.
This will establish the correct distance between the
drums at the front of a steam boiler and the rear of
both steam and hot water boilers. The correct drum-
to-drum spacing at the front of the boiler is
established by temporarily installing an adjustable
drum spreader. The drum spreader should be
installed at the end of the drums, as shown in
Figure 2-6. The part numbers for the drum
spreaders are shown in Table 2-2. See table 2-1 for
drum dimensions.
6. Check All Drum Holes and Studs
Drum Holes
Check all drum holes for any burrs, weld splatter or
distortion as any imperfections must be cleaned or
repaired. To clean burrs or welding spatter, use 150
grit emery cloth (Figure 2-7).
CAUTION
Drum holes may be sharp from the machining
process. Burrs and sharp machined edges can
cause severe cuts. Care must be taken when
inspecting drum holes.
Studs
If there are any threads causing the tube retainer
studs to bind, chase them with a 5/8” die (Figure 2-
8). Checking all the retainer stud threads will make
the assembly process go smoother. All retainer
studs must be coated with “Never-Seez”.
Figure 2-6. Drum spreader in position on completed
vessel
Figure 2-7. Use a 5/8" die to chase all the retainer
stud threads
Table 2-2 Drum Spreader Part Numbers for Hot Wa-
ter Units by Size
Size
Part No.
150-250
98-317
300-350
98-323
400-600
98-318
700-1200
98-324
Содержание FLE
Страница 1: ...Model FLE Assembly Instructions 750 192 07 09 Field Erectable Flexible Watertube Boiler ...
Страница 4: ...iv Notes ...
Страница 8: ...viii ...
Страница 16: ...General Description Model FLE Assembly 1 8 750 192 ...
Страница 34: ...3 2 750 192 Figure 3 1 Typical Hot Water Flextube Casing ...
Страница 36: ...3 4 750 192 Figure 3 2 Typical Low Pressure Steam Flextube Casing ...
Страница 38: ...3 6 750 192 Figure 3 3 Typical High Pressure Steam Flextube Casing ...
Страница 56: ...Casing Assembly Model FLE Assembly 3 24 750 192 ...
Страница 58: ...750 192 4 2 Figure 4 2 Fuel Train Components ...
Страница 60: ...4 4 750 192 Figure 4 5 Typical conduit layout ProFire burner on a hot water Flextube boiler ...
Страница 61: ...750 192 4 5 Figure 4 6 Typical conduit layout ProFire burner on a steam Flextube boiler ...
Страница 62: ...4 6 750 192 Figure 4 7 Nameplate locations hot water boiler ...
Страница 63: ...750 192 4 7 Figure 4 8 Nameplate locations steam boiler ...
Страница 64: ...e mail info cleaverbrooks com Web Address http www cleaverbrooks com ...