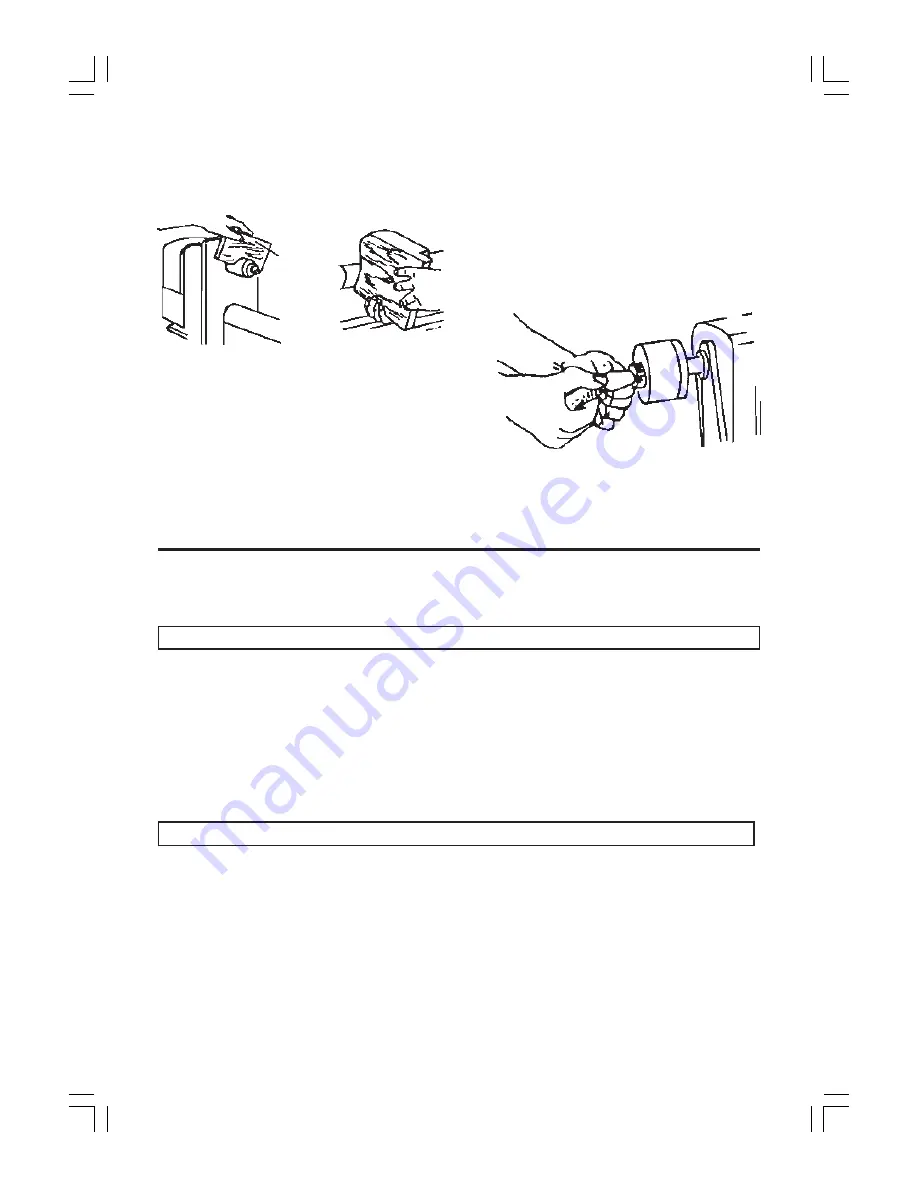
glued or tacked in place, do satisfactory work.
These have the advantage that special sizes,
tapers etc., can be made.
The drum is used mainly for sanding the edges
of curved work. The squareness of the edge of
the work can be best retained by using a simple
form of vertical fence as shown. The standard
sanding drums are commonly made with a
threaded hole to fit the Lathe Drive Spindle. To
guard against loosening of the taper shank while
the drum is in operation, it is advisable to support
the free end, using either a ball bearing or plain
60° centre in the tailstock.
4.
USE OF WOOD CHUCKS FOR SANDING
Quick acting chucks can be very useful for
sanding operations on duplicate production
parts. The chuck is made slightly oversized, and
a piece of rubber hose (for small parts) is inserted
in the recess to grip the workpieces. Workpieces
can be changed without stopping the lathe.
MAINTENANCE
WARNING : FOR YOUR OWN SAFETY, TURN THE SWITCH ‘OFF’ AND REMOVE THE PLUG FROM THE
ELECTRICAL SOCKET BEFORE MAINTAINING OR LUBRICATING YOUR LATHE.
Frequently blow out any dust that may accumulate inside the motor.
A coat of car-type wax applied to the bed will help to keep the surfaces clean and allow the tool
rest and tailstock to move freely.
If the mains lead is worn, cut or damaged in any way, have it replaced immediately.
LUBRICATION
All the BALL BEARINGS are packed with grease at the factory and require no further lubrication.
Periodically lubricate the the tailstock spindle with either SAE20 or SAE30 engine oil.
35
Fig.77
Fig. 76