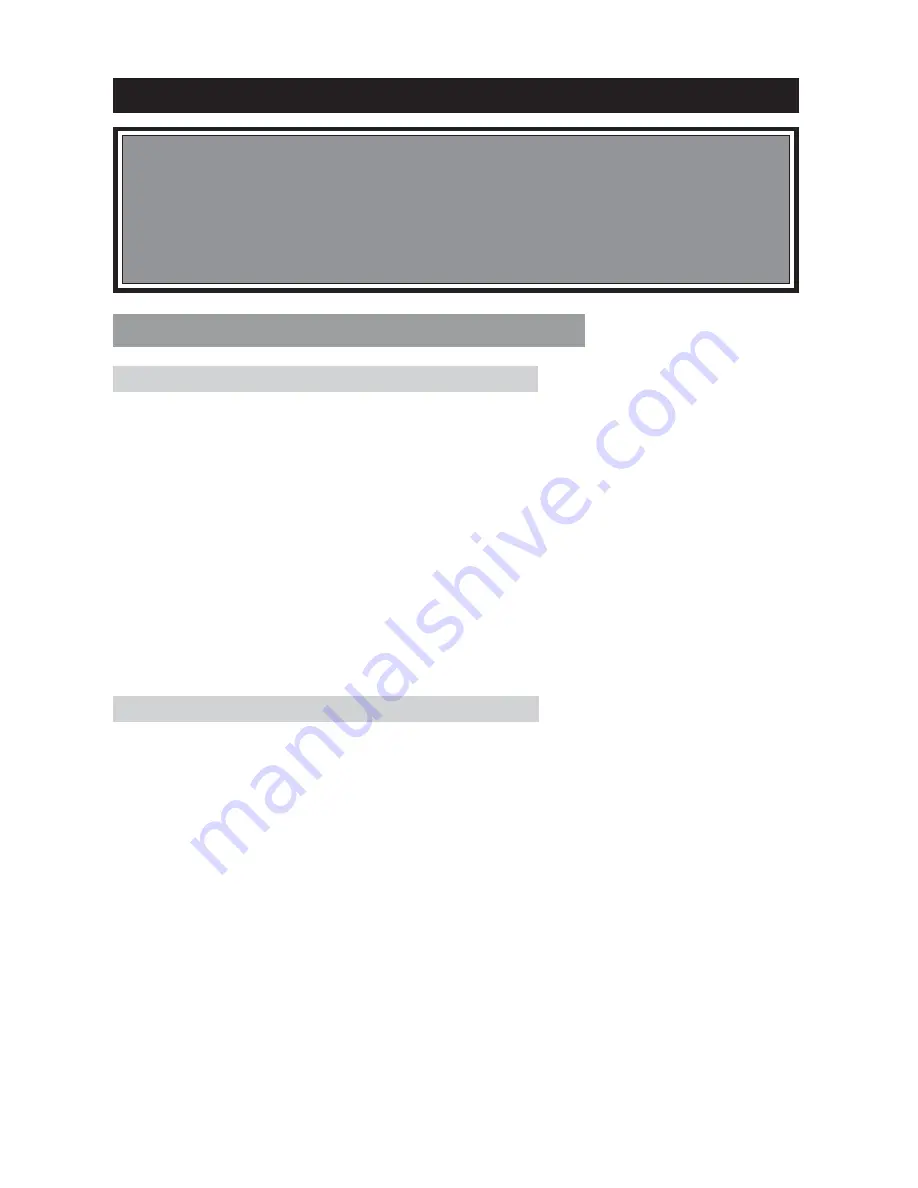
SAFETY PRECAUTIONS FOR ALL TYPES OF WELDING
1. WARNING:
As with all machinery, there are certain hazards involved with their operation
and use. Exercising respect and caution will considerably lessen the risk of
personal injury. However, if normal safety precautions are overlooked, or
ignored, personal injury to the operator may result.
FAILURE TO FOLLOW THESE RULES MAY RESULT IN SERIOUS PERSONAL INJURY
2. GENERAL PRECAUTIONS
A) Burn prevention
Wear protective clothing - gauntlet gloves designed for use in welding, apron, and
protective shoes. Button shirt collar and pocket flaps, and wear cuffless trousers to
avoid entry of sparks and slag. Wear helmet with safety goggles or glasses with side
shields underneath, appropriate filter lenses or plates (protected by clear cover
glass). This is a MUST for welding or cutting, (and chipping) to protect the eyes from
radiant energy and spatter. Replace cover glass when broken, pitted, or spattered.
Avoid oily greasy clothing. A spark may ignite them. Hot metal such as electrode
stubs and workpieces should never be handled without gloves. First aid facilities and
a qualified first aid person should be available unless medical facilities are close by
for immediate treatment of flash burns of the eyes and skin burns. Ear plugs should
be worn when working overhead or in a confined space. A hard hat should be
worn when others work overhead. Flammable hair preparations should not be used
by persons intending to weld or cut.
B) Toxic fume prevention
Severe discomfort, illness or death can result from fumes, vapours, heat, or oxygen
enrichment or depletion that welding (or cutting) may produce. Prevent them
with adequate ventilation. NEVER ventilate with oxygen. Lead-, cadmium-, zinc-,
mercury- and beryllium-, bearing materials, when welded (or cut) may produce
harmful concentrations of toxic fumes. Adequate local exhaust ventilation must
be used, or each person in the area as well as the operator must wear an air-
supplied respirator. For beryllium, both must be used. Metals coated with or
containing materials that emit toxic fumes should not be heated unless coating is
removed from the work surface, the area is well ventilated, or the operator wears
an air-supplied respirator. Work in a confined space only while it is being ventilated
and, if necessary, while wearing an air-supplied respirator. Vapours from chlorinated
solvents can be decomposed by the heat of the arc (or flame) to form PHOSGENE,
a highly toxic gas, and other lung and eye irritating products. The ultraviolet
(radiant) energy of the arc can also decompose trichloroethylene and
perchloroethylene vapours to form phosgene. DO NOT WELD or cut where solvent
vapours can be drawn into the welding or cutting atmosphere or where the radiant
energy can penetrate to atmospheres containing even minute amounts of
trichloroethylene or perchloroethylene.
6