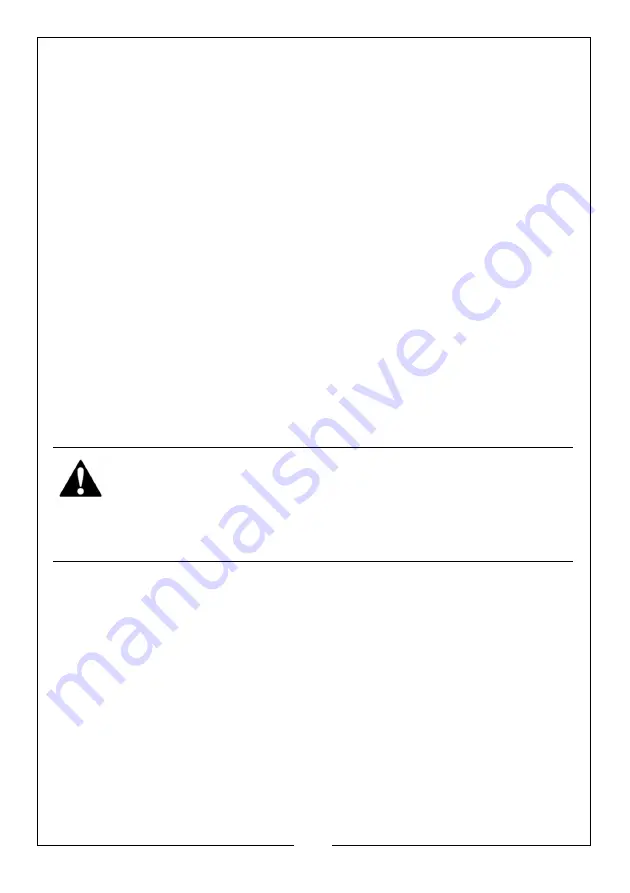
6
Parts & Service: 020 8988 7400 / E-mail: [email protected] or [email protected]
3. Always make all adjustments with the power off.
4. Always use the correct speeds for the bit size and the type of material
being worked.
5. Never leave the machine unattended whilst it is running. Turn the machine
OFF and do not leave until it has come to a complete stop.
6. Always remove and store the bits when you have finished work.
7. Never attempt to drill into a workpiece that does not have a flat surface
unless a suitable support is used.
8. Always stop the machine before removing workpieces, work supports or
swarf from the table.
9. Keep bits sharp and clean for best and safest performance. Follow
instructions for changing accessories.
10. Adjust the table or depth stop to avoid drilling into the table surface.
11. Always be sure that the bit is securely locked in the chuck.
12. Never assemble or set up any work on the table while the machine is
running.
13. Keep handles dry, clean and free from oil and grease.
14. Always keep hands and fingers away from the bit.
PROTECTIVE CLOTHING
1. Dress properly. Loose clothing or other jewellery may get caught in moving
parts. Non-slip footwear is recommended. Wear protective hair covering to
contain long hair.
2. Always wear safety glasses. (Everyday glasses are not safety glasses)
3. Wear a face mask if drilling into any material which produces dust.
4. Never wear gloves when operating rotating equipment.
WARNING: DUST GENERATED FROM CERTAIN MATERIALS CAN BE
HAZARDOUS TO YOUR HEALTH. ALWAYS OPERATE IN A WELL VENTILATED
AREA. USE A DUST COLLECTION SYSTEM IF POSSIBLE.
WARNING: THE USE OF ANY ACCESSORY OR ATTACHMENT OTHER THAN
ONE RECOMMENDED IN THIS INSTRUCTION MANUAL MAY PRESENT A RISK
OF PERSONAL INJURY.
Содержание 7610860
Страница 28: ......