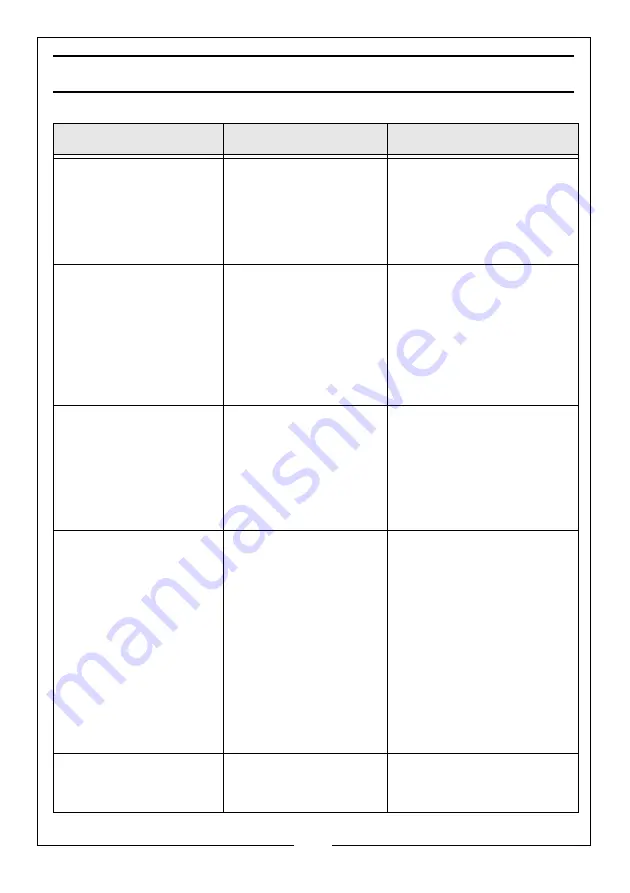
12
Parts & Service: 020 8988 7400 / E-mail: [email protected] or [email protected]
TROUBLESHOOTING
SYMPTOM
PROBLEM
SOLUTION
Tool runs at normal
speed but slows down
under any load.
1. Motor parts worn.
2. Worn or sticking
mechanism due to
lack of lubricant.
1. Return to CLARKE dealer
for repair.
2. Drip air tool lubricating
oil into air inlet. Allow oil
to soak moving parts
before using.
Tool runs slowly. Air flows
weakly from exhaust.
1. Motor parts jammed
with gum/dirt.
2. Air-line regulator in
closed position.
3. General airflow
blocked by dirt.
1. Examine inlet air filter for
blockage. Drip a few
drops of air tool lubricat-
ing oil into air inlet.
2. Adjust in-line regulator to
open position.
3. Operate tool in short
bursts.
Tool will not run. Air flows
freely from exhaust.
1. Motor vanes stuck
due to buildup of
foreign material.
1. Try operating tool in
short bursts.
2. Tap motor housing gently
with a rubber mallet.
3. Drip a few drops of air
tool lubricating oil into air
inlet to soak moving parts
Loss of power or erratic
performance.
1. Excessive drain on
the air hose.
2. Incorrect size or type
of hose connectors.
3. Moisture or restriction
in the air hose/tank
4. Compressor has
insufficient flow
1. Check and confirm that
air hose and fitting is
correct for the air inlet.
2. Do not use multiple hoses
connected together with
quick connecting fittings.
3. Vent system and drain
tank and air hose of
water. Oil tool and run for
1-2 seconds & ensure no
water is evident.
4. Ensure air supply rate
matches tool.
Tool will not shut off.
1. Throttle O-rings
damaged or ill-fitting
in seat.
1. Return to your CLARKE
dealer for repair.
Содержание 3110470
Страница 16: ......