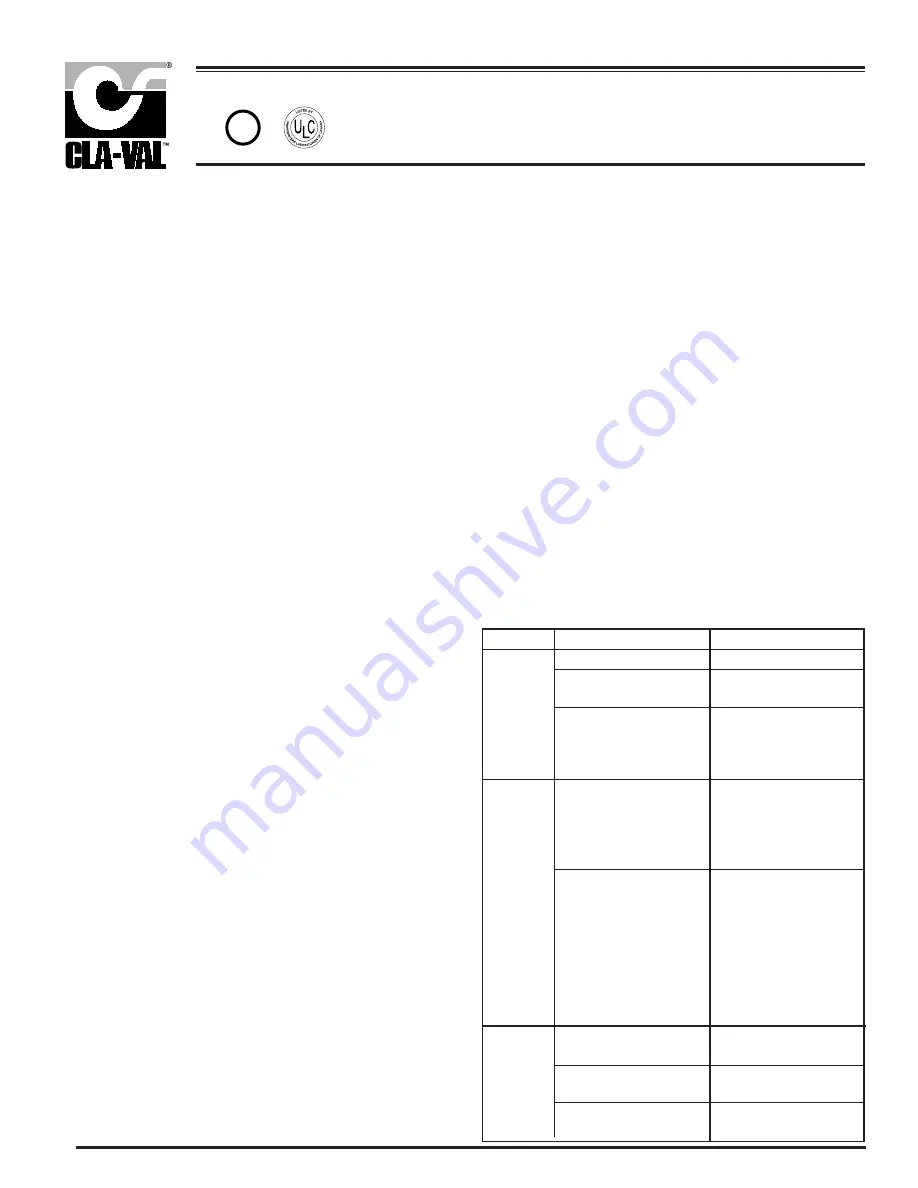
UL Listed Pressure Reducing Valve
INSTALLATION / OPERATION / MAINTENANCE
90-21 UL
MODEL
The Cla-Val 90-21 Pressure Reducing Valve is a pilot-operated
regulator, capable of holding downstream pressure to a predeter-
mined pressure.
1.
Special Note:
For system protection, a pressure relief valve is
to be installed downstream (system side) of the 90-21 Pressure
Reducing Valve. Adequate drainage of the relief valve discharge
must be provided. The relief valve should be set above the “no
flow” or “dead end” shutoff pressure which will be 5 to 11 psi high-
er than the set pressure.
2. Allow sufficient room around the valve assembly to make adjust-
ments and for disassembly.
3. It is recommended that isolation valves be installed on both
ends of the 90-21 valve to facilitate isolating the valve for start-up,
testing and preventative maintenance.
4.
BEFORE THE VALVE IS INSTALLED, PIPE LINES SHOULD
BE FLUSHED OF ALL CHIPS, SCALE, AND FOREIGN MATTER.
5. Place the 90-21 valve in the line with flow through the valve in
the direction indicated on the inlet nameplate mounted on inlet
flange or by arrow on nameplate mounted on side of threaded
ends valves. Check all fittings and hardware for proper makeup
and that no apparent damage is evident.
6. Cla-Val valves operate with maximum efficiency when mounted
in horizontal piping with the cover UP; however, other positions
are acceptable. Due to size and weight of cover and internal com-
ponents of six inch and larger valves, installation with the cover up
is advisable. This makes periodic inspection of internal parts read-
ily accessible.
Start-Up and Adjustment
1. Upon initial start-up and after any valve servicing, it is necessary
to follow these steps.
2. Prior to pressurizing the valve make sure the necessary gauges
to measure pressure are installed. Gauges should be installed
upstream (inlet) and downstream (outlet) of the valve. Unused
ports on main valve body can be used for this purpose.
Caution:
During start-up and test procedures a large volume of
water may be discharged downstream. Check to make sure that
the downstream venting is adequate to prevent damage to per-
sonnel and equipment.
3. Close upstream and downstream isolation valves.
4. Slowly open the upstream isolation valve enough to allow the
valve and pilot control system to fill with liquid.
5. Bleed air from the main valve (1) cover and pilot system by
slightly loosening fittings or plugs at all high points until a steady
flow of water is observed retighten. It may be necessary to do this
more than once.
6. Open fully the upstream isolation valve.
7. Slowly open the downstream isolation valve part way to estab-
lish a low flow rate.
There must be liquid flowing through the valve during
pressure adjustments
. Optimum valve performance occurs when
pressure setting is done with flow rate as low as practical.
8. Adjust the CRD Control (3) to desired pressure. To change pres-
sure setting, turn the adjusting screw in (clockwise) to increase
delivery pressure. Turn the adjusting screw out (counterclockwise)
to decrease delivery pressure. The pressure should change
approximately 27 psi per turn. Only slight changes in adjustment
should be made to avoid damage to equipment. When the desired
setting has been made, tighten jam nut and replace cover.
NOTE:
The “no flow” or “dead end” shutoff pressure will be 5 to 11
psi above the set pressure.
9. Open downstream isolation valve fully.
Maintenance
1. The Cla-Val 90-21 Pressure Reducing Valve requires no lubri-
cation or packing and a minimum of maintenance. However, a peri-
odic inspection schedule should be established to determine how
the fluid handled is affecting the efficiency of the valve.
Minimum of once per year.
2. When servicing the pilot control system, use care to prevent
damage. If it is necessary to remove fittings or components, be
sure they are kept clean and replaced exactly as they were.
3. Repair and maintenance procedures of the Cla-Val Hytrol Main
Valve and pilot control components are included in a more detailed
IOM manual. It can be downloaded from our web site (www.cla-
val.com) or obtained by contacting a Cla-Val Regional Sales
Office.
4.
When ordering parts always refer to the catalog number
and stock number on the valve nameplate.
Main valve
fails to open
Main valve
fails to close
Fails to
Regulate
No pressure at valve inlet
Main valve diaphragm assembly
inoperative
Pilot Valve (CRD) not opening:
1. No. spring compression
2. Damaged spring
3. Spring guide not in place
4. Yoke dragging on inlet nozzle
Foreign matter between disc
and
seat or worn disc. Scale on stem
or Diaphragm ruptured
Flow Clean Strainer plugged
CK2 (isolation valves) closed
Pilot Valve (CRD) remain open:
1. Spring compressed solid
2. Mechanical obstruction
3. Worn disc
4. Yoke dragging on inlet nozzle
diaphragm nut. Leakage from
vent hole in cover
5. Diaphragm damaged or loose
diaphragm nut. Leakage from
vent hole in cover
Air in main valve cover and/or
tubing
Pilot Valve (CRD) yoke dragging
on inlet nozzle
Pilot Valve (CRD) spring not in
correct range to control
Check inlet pressure
Disassemble, clean and polish
stem, replace detective parts
1. Tighten adjusting screw
2. Disassemble and replace
3. Assemble properly.
4. Assemble properly
Disassemble main valve,
remove matter, clean parts and
replace defective parts
Remove and clean or replace
Open isolation valves
1. Back off adjusting screw
2. Disassemble and remove
obstruction
3. Disassemble remove and
replace disc retainer assembly
4. Assemble properly
5. Disassemble. replace
diaphragm and/or tighten nut
Loosen top cover plug and fit-
tings and bleed air
Assemble properly
Check outlet pressure require-
ments
SYMPTOM
PROBABLE CAUSE
REMEDY
UL
®
Distributed By: M&M Control Service, Inc.
www.mmcontrol.com/claval-index.php 800-876-0036 847-356-0566
Содержание 90-21
Страница 4: ...Distributed By M M Control Service Inc...
Страница 5: ...Distributed By M M Control Service Inc www mmcontrol com claval index php 800 876 0036 847 356 0566...
Страница 16: ...Distributed By M M Control Service Inc...
Страница 21: ...Distributed By M M Control Service Inc www mmcontrol com claval index php 800 876 0036 847 356 0566...
Страница 22: ...Distributed By M M Control Service Inc www mmcontrol com claval index php 800 876 0036 847 356 0566...
Страница 23: ...Distributed By M M Control Service Inc www mmcontrol com claval index php 800 876 0036 847 356 0566...