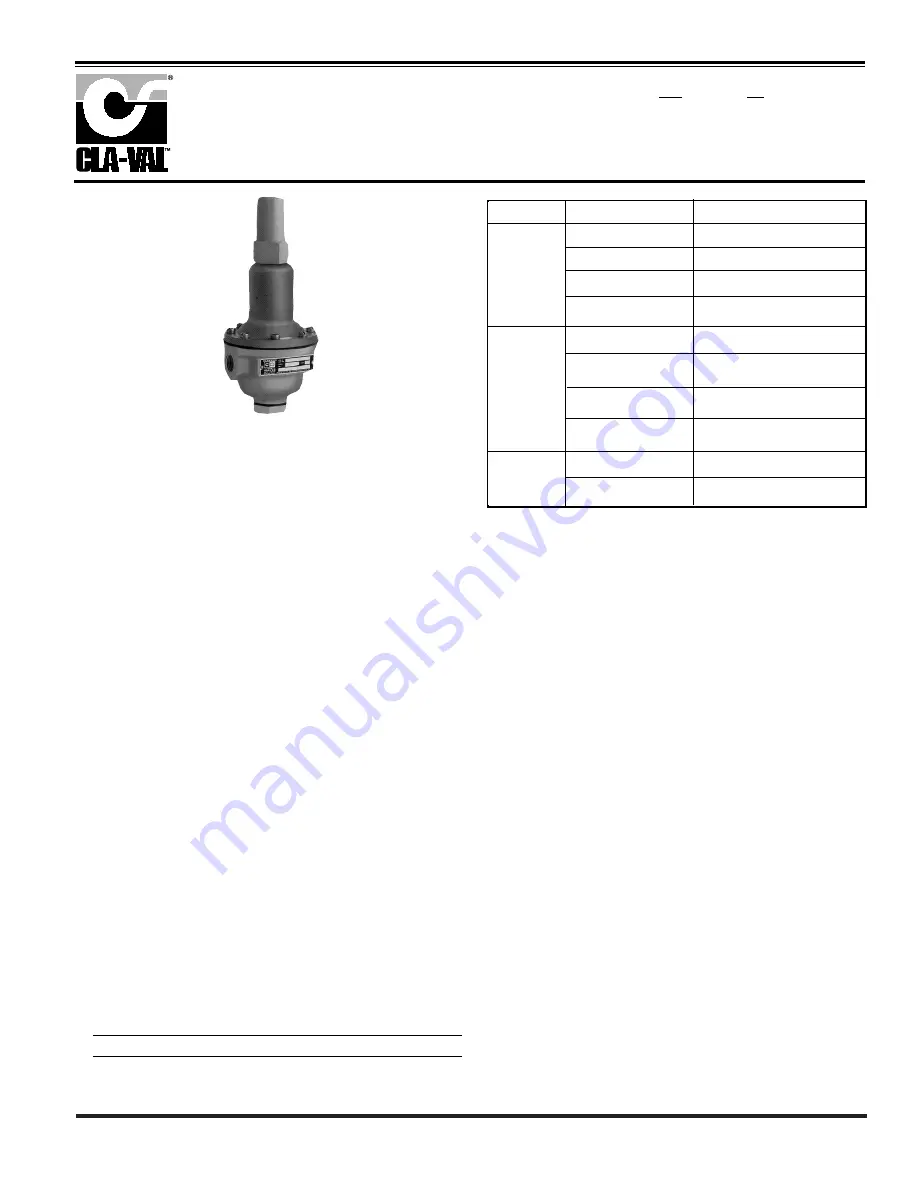
DESCRIPTION
The Cla-Val Model CRD Pressure Reducing Control automatically reduces
a higher inlet pressure to a lower outlet pressure. It is a direct acting,
spring loaded, diaphragm type control that operates hydraulically or pneu-
matically. It may be used as a self-contained valve or as a pilot control for
a Cla-Val main valve. It will hold a constant downstream pressure within
very close pressure limits.
OPERATION
The CRD Pressure Reducing Control is normally held open by the force of
the compression spring above the diaphragm; and delivery pressure acts
on the underside of the diaphragm. Flow through the valve responds to
changes in downstream demand to maintain a pressure.
INSTALLATION
The CRD Pressure Reducing Control may be installed in any position.
There is one inlet port and two outlets, for either straight or angle installa-
tion. The second outlet port can be used for a gage connection. A flow
arrow is marked on the body casting.
ADJUSTMENT PROCEDURE
The CRD Pressure Reducing Control can be adjusted to provide a deliv-
ery pressure range as specified on the nameplate.
Pressure adjustment is made by turning the adjustment screw to vary the
spring pressure on the diaphragm. The greater the compression on the
spring the higher the pressure setting.
1. Turn the adjustment screw in (clockwise) to increase
delivery pressure.
2. Turn the adjustment screw out (counter-clockwise) to
decrease the delivery pressure.
3. When pressure adjustment is completed tighten jam nut on
adjusting screw and replace protective cap.
4. When this control is used, as a pilot control on a
Cla-Val main valve, the adjustment should be made
under flowing conditions. The flow rate is not critical,
but generally should be somewhat lower than normal
in order to provide an inlet pressure several psi higher
than the desired setting
SYMPTOM
PROBABLE CAUSE
REMEDY
Fails to open
when deliver
pressure lowers
No spring compression
Tighten adjusting screw
Spring guide (8) is not in
place
Assemble properly
Yoke dragging on inlet
nozzle
Disassemble and reassemble
properly (refer to Reassembly)
Fails to close
when delivery
pressure rises
Spring compressed solid
Back off adjusting screw
Mechanical obstruction
Disassemble and reassemble
properly (refer to Reassembly)
Worn disc
Disassemble remove and
replace disc retainer assembly
Yoke dragging on inlet
nozzle
Disassemble and reassemble
properly (refer to Reassembly)
Leakage from
cover vent hole
Damaged diaphragm
Disassemble and replace
Loose diaphragm nut
Remove cover and tighten nut
Damaged spring
Disassemble and replace
CRD
MAINTENANCE
Disassembly
To disassemble follow the sequence of the item numbers assigned to
parts in the sectional illustration.
Reassembly
Reassembly is the reverse of disassembly. Caution must be taken to
avoid having the yoke (17) drag on the inlet nozzle of the body (18).
Follow this procedure:
1. Place yoke (17) in body and screw the disc retainer
assembly (16) until it bottoms.
2. Install gasket (14) and spring (19) for 2-30 and 2-6.5 psi
range onto plug (13) and fasten into body. Disc retainer
must enter guide hole in plug as it is assembled. Screw
the plug in by hand. Use wrench to tighten only.
3. Place diaphragm (12) diaphragm washer (11) and belleville
washer (20) on yoke. Screw on hex nut (10).
4. Hold the diaphragm so that the screw holes in the
diaphragm and body align. Tighten diaphragm nut with
a wrench. At the final tightening release the diaphragm
and permit it to rotate 5° to 10°. The diaphragm holes
should now be properly aligned with the body holes.
To check for proper alignment proceed as follows:
Rotate diaphragm clockwise and counterclockwise as far as possible.
Diaphragm screw holes should rotate equal distance on either side of
body screw holes ±1/8".
Repeat assembly procedure until diaphragm and yoke are properly
aligned. There must be no contact between yoke and body nozzle
during its normal movement. To simulate this movement hold body
and diaphragm holes aligned. Move yoke to open and closed posi-
tions. There must be no evidence of contact or dragging.
5. Install spring (9) with spring guide (8).
6. Install cover (5), adjusting screw (2) and nut (3), then cap (1).
Pressure Reducing Control
The approximate minimum flow rates given in the table are for the main valve
on which the CRD is installed.
Valve Size
Minimum Flow GPM
1 1/4" -3"
4"-8"
10"-16"
15-30 50-200
300-650
MODEL
INSTALLATION / OPERATION / MAINTENANCE
N-CRD (R-1/08)
Distributed By: M&M Control Service, Inc.
www.mmcontrol.com/claval-index.php 800-876-0036 847-356-0566
Содержание 90-21
Страница 4: ...Distributed By M M Control Service Inc...
Страница 5: ...Distributed By M M Control Service Inc www mmcontrol com claval index php 800 876 0036 847 356 0566...
Страница 16: ...Distributed By M M Control Service Inc...
Страница 21: ...Distributed By M M Control Service Inc www mmcontrol com claval index php 800 876 0036 847 356 0566...
Страница 22: ...Distributed By M M Control Service Inc www mmcontrol com claval index php 800 876 0036 847 356 0566...
Страница 23: ...Distributed By M M Control Service Inc www mmcontrol com claval index php 800 876 0036 847 356 0566...