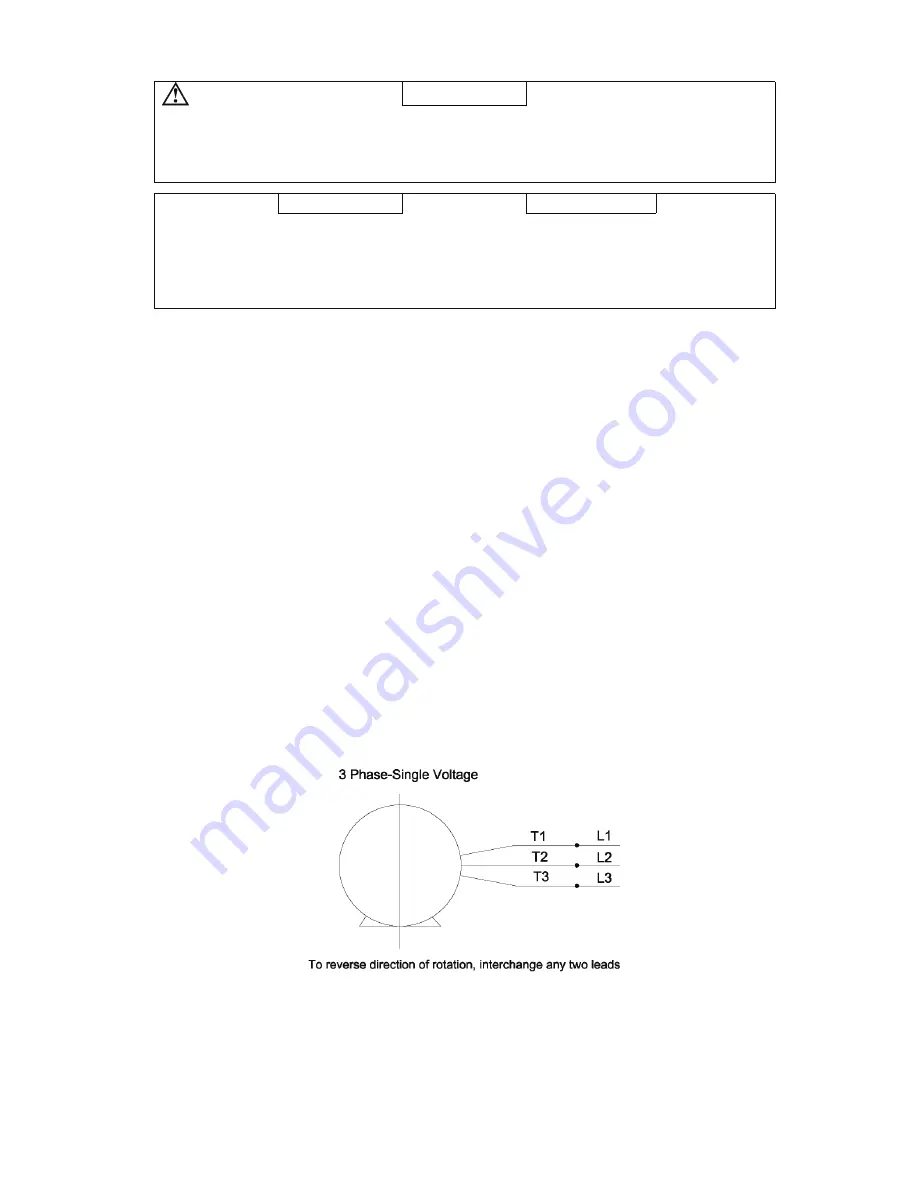
INSTALLATION
WARNING
This Equipment is limited to handling fluids compatible with motor windings and
insulation. Provide suitable safety and emergency systems to protect personnel
and property from injury due to pump malfunction, If pump handles hazardous
fluids, provide for safety in event of pump leakage or malfunction.
CAUTION
ATTENTION
Piping to pump MUST be independently supported and not allowed to impose
strains on case. Piping connections should be flexible whenever possible and
make provision for expansion and contraction due to temperature change. Piping
connections must not impose more than 1 times “API” forces and moments on inlet
and outlet.
Inlet Position
The pump inlet flange may be positioned in increments of 90° from position shown on assembly drawing.
To change position of flange, remove socket head cap screws (203) and lock washers (207). Rotate
housing (201) and inlet head (202) as a unit taking care not to damage O-ring (409). Replace socket head
cap screws with lock washers and torque to value on assembly drawing depending on pump type. Care
must be taken to not disengage pump shaft (311) from motor shaft . If this occurs, ensure key (213) is in
place and properly related before re-engaging shafts.
Suction Line
The suction line should be as short as possible. A suction line one size larger than pump inlet is
recommended. All joints in suction line must be tight and sealed. This prevents air from being drawn into
a pump with negative suction pressure or leaks from pump or line with positive pressure.
Suction Strainer
A suction strainer of at least 100 mesh with a flow capacity of 30 - 50 gpm and a pressure drop not
exceeding 0.5 psi ( when newly installed) should be used. (Inlet strainer shall be sized to insure that
pressure at inlet port of pump will not, under any circumstances, exceed 10 inches of mercury vacuum.)
Maintenance instructions shall provide for periodic cleaning or replacement of inlet strainer.
Electrical Connections
A label giving the electrical wiring connections for canned motor pump is located under conduit box cover
and in Figure 3. Note that extended reverse rotation can cause pump damage.
Figure 3 – Motor Wiring Connections
Rotation
Before attempting to operate pump, rotation must be verified. It is suggested that this can best be
accomplished with a Phase and Motor Rotation Tester such as AVO Biddle Instruments Catalogue No.
560060 / 560400 (510 Township Line Road, Blue Bell, PA 19422 USA). Follow instrument manufacture’s
instructions to determine proper motor/pump rotation.
2
Содержание IMO 110
Страница 7: ...Figure 4 5...