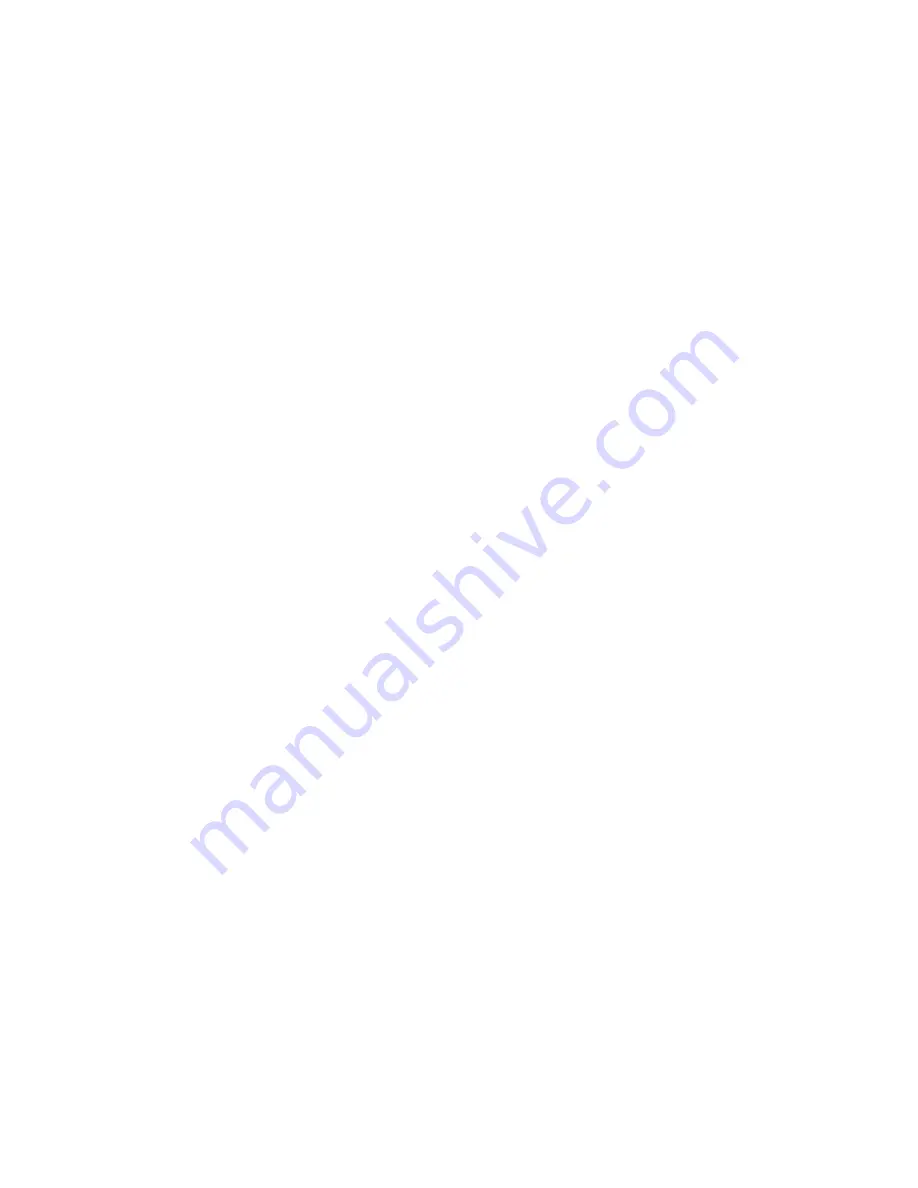
2
SUCTION STRAINER
A suction strainer with adequate flow rate and minimum pressure drop should be used to keep contamination
from entering the pump and system. The maximum pressure drop (when dirty) across the strainer plus all
other losses in the pump suction line at maximum fluid viscosity, including static lift, must not exceed the
suction lift capability of the pump. Regular cleaning of the suction strainer must be included in the mainte-
nance of the machine.
Note:
Keeping the fluid and system clean is essential in achieving maximum pump life.
BELT DRIVEN PUMPS – ALIGNMENT
Mount the sheaves as close to the bearing retainer as possible. This minimizes the overhung load on the
shaft.
Align the sheaves with a straight edge so their faces are parallel with no offset. Misaligned sheaves can cause
noise, shorten belt life, and may reduce the bearing life of the pump and/or motor.
Apply belt tension according to the belt manufacturer’s recommendations. After tension is applied, recheck
sheave alignment. Do NOT overtension belts. While loose belts slip and wear excessively, excessive belt
tension may cause misalignment, belt failures, and in extreme cases, a shaft failure.
For smooth, quiet, high speed operation, sheaves must be balanced and shaft bores must be concentric with
belting grooves.
When matched belts are removed, they should be kept in sequence and replaced exactly in the grooves from
which they were removed.
DIRECT DRIVEN PUMPS – ALIGNMENT
All pump-driver sets must be checked for proper alignment when the unit is installed and after all piping has
been connected to the pump. Factory alignment will most likely be disturbed during shipment and installation.
A flexible coupling is not intended to permit permanent misalignment. Proper alignment must be established
and maintained to obtain maximum pump life. Follow these steps:
1. Install the pump and/or motor.
2. Before aligning the units, be sure that all stresses are removed from the pump and that the foot of the
pump case fully conforms to its support.
3. Set the coupling end face gap as specified by the coupling manufacturer.
4. Perform rough alignment of the face and rim of the coupling using feelers and a straight edge.
5. Perform the final alignment of the pump and driver shaft using dial indicators. Acceptable alignment has
been obtained when the F.I.R. is less than or equal to .005" in both the face (angularity) and the rim
(parallelism) checks while rotating both shafts together 360
°
.
6. In special cases, “hot alignment” when the pump and motor are at operating temperature may be required.
Periodically check the alignment of the pump and its driver. Realign as necessary. Maintaining proper align-
ment is necessary for quiet operation and maximum equipment life.
ROTATION
Before connecting the belts our coupling, check the driver rotation to be sure it matches the required rotation
of the pump. Extended reverse rotation may cause damage.
When the coupling is connected and shafts are correctly aligned, the pump should turn freely by hand.
On initial start-up, it is suggested that the driver be “jogged” quickly before continuous operation to be sure the
system and pump and motor are functioning properly and rotating in the intended direction.