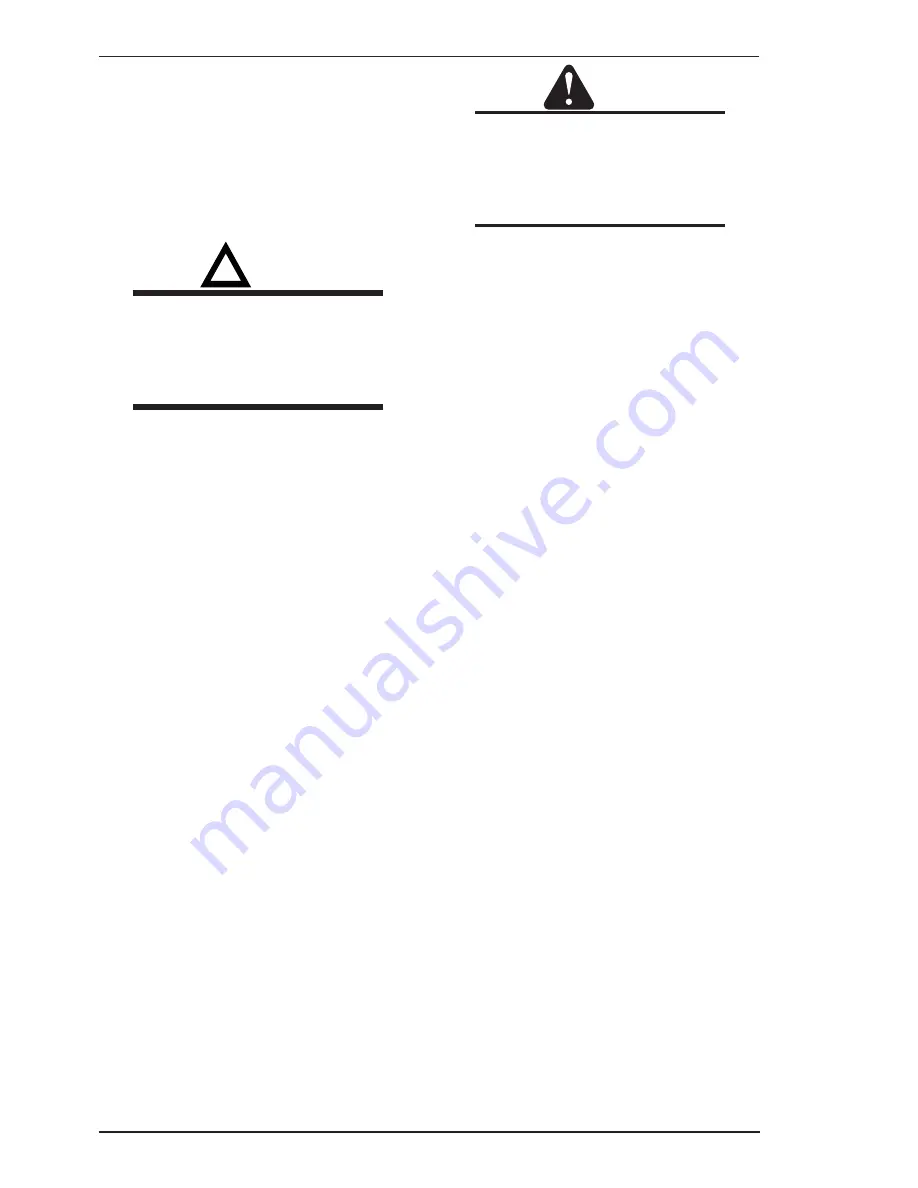
TRANSTIG 200 Pi
SERVICE MANUAL
3-4
March 31, 2008
3.07 Duty Cycle
The duty cycle of a welding power source is the
percentage of a ten (10) minute period that it can be
operated at a given output without causing
overheating and damage to the unit. If the welding
amperes decrease, the duty cycle increases. If the
welding amperes are increased beyond the rated
output, the duty cycle will decrease.
!
WARNING
Exceeding the duty cycle ratings will cause
the thermal overload protection circuit to
become energized and shut down the
output until the unit has cooled to normal
operating temperature.
CAUTION
Continually exceeding the duty cycle
ratings can cause damage to the welding
power source and will void the
manufactures warranty.
NOTE
Due to variations that can occur in
manufactured products, claimed
performance, voltages, ratings, all
capacities, measurements, dimensions
and weights quoted are approximate only.
Achievable capacities and ratings in use
and operation will depend upon correct
installation, use, applications,
maintenance and service.