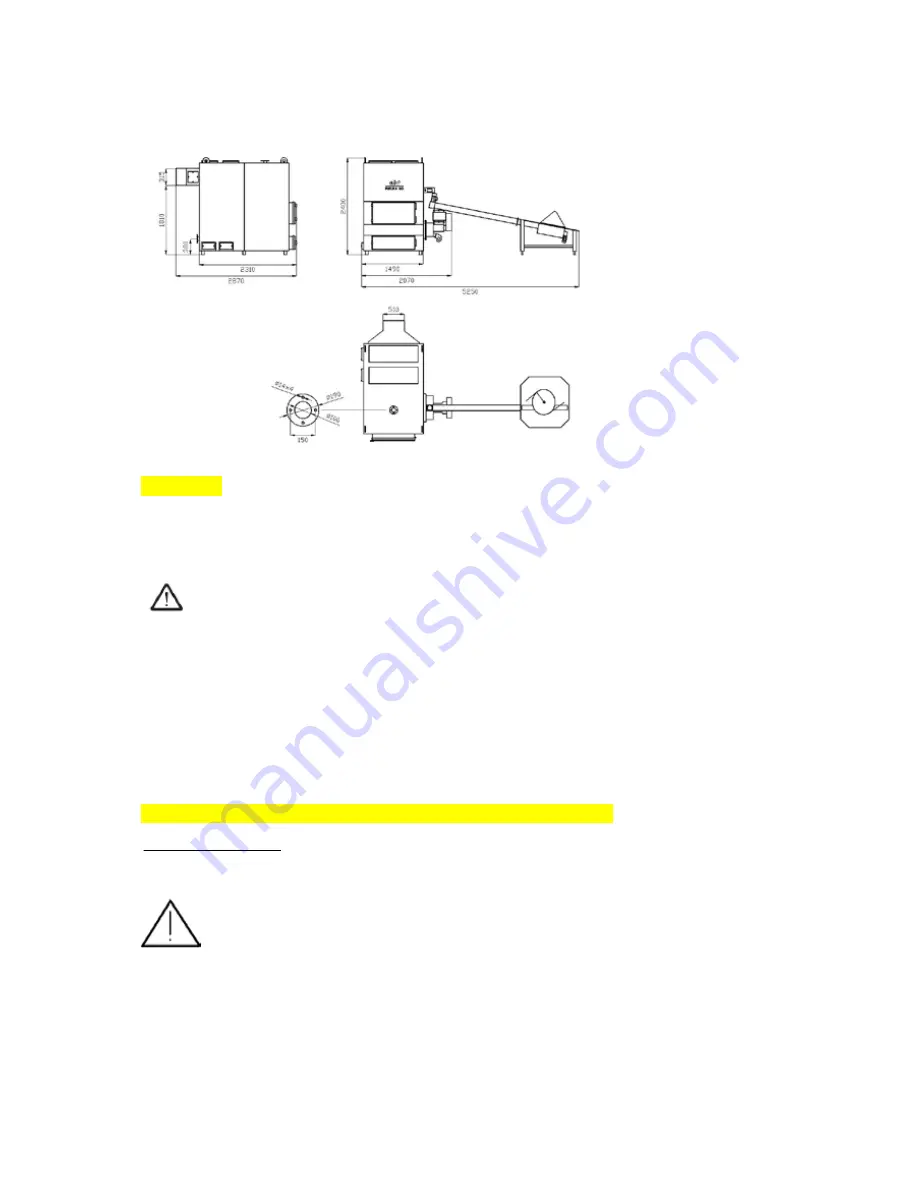
11
Figure: Dimensions of Bio Pellets 300-350 kW boiler
4. Safety
5. Boiler installation procedure and installation requirements
The design of Futura Bio boilers incorporates modern solutions concerning solid fuel combustion.
To ensure safe operation and use of the boiler, please read this manual carefully and always follow the guidelines
and recommendations given in it.
The boiler is supplied with electric power 400 V / 50 Hz. Incorrect installation or improper repair may
endanger life or health by exposing to electric shock.
OCCUPATIONAL HEALTH AND SAFETY GUIDELINES
1. Prior to boiler start-up, read this operating and maintenance manual.
2. Before starting the boiler up, check if it was installed properly in both electric and hydraulic aspects.
3. Never use solvents, petrol or similar substances for lighting of fuel.
4. Never step into fuel tank and poke fuel manually when the boiler is operating.
5. Never open electric box or fuse box when the boiler is not disconnected from the electric power
source, otherwise a risk of electric shock may occur.
6. Fuel can be charged only when fuel feeder is stopped.
General requirements
The boiler room where the boiler is to be installed must meet the requirements of Polish standard
No. PN-87/B-02411.
Each boiler fired with solid fuel has to be installed in accordance with valid standards and legal
regulations.
Unauthorised modifications of mechanical or electrical part of boiler structure will be
regarded as breach of warranty conditions causing its immediate termination.
First start-up of the boiler should be performed by authorised manufacturer’s service staff.
The heating system should be built according to the following guidelines:
a) The boiler should be installed in the open-type system.
b) The boiler should be installed at a safe distance from combustible or flammable materials.
c) Electric power supply is 400 V/ 50 Hz; the boiler should be electrically connected according to valid
regulations and standards by a qualified electrician who has all necessary licences.
d) The boiler should be connected to the chimney in compliance with valid regulations and
manufacturer’s recommendations.
e) A chimney draught regulator must be installed.