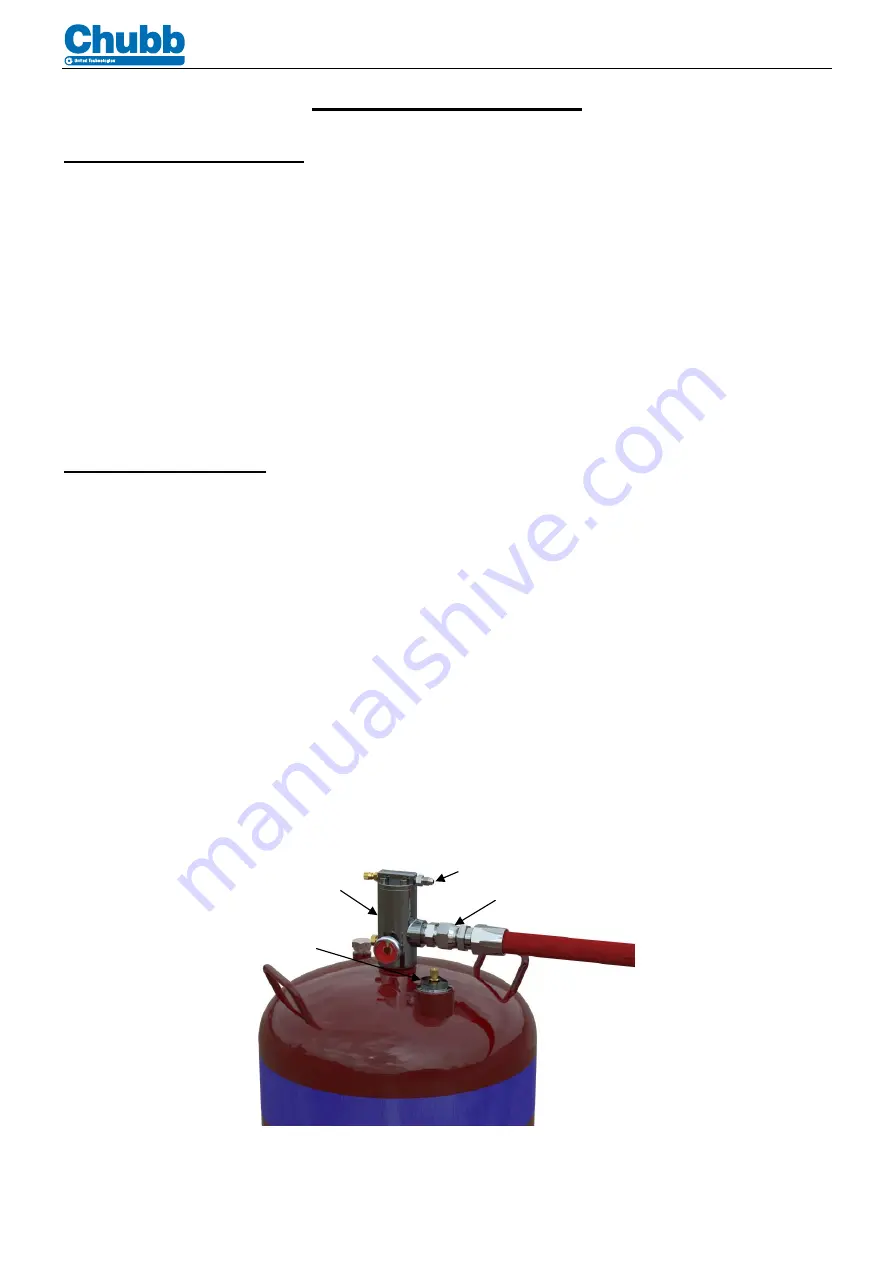
Maintenance Manual
17
PEFS F3 Maintenance Manual, Version 1.2, Feb 2018
© Copyright 2017 Chubb Fire & Security Pty Ltd
Yearly Service Instructions
Discharge Test [Optional] (Item 9)
An annual discharge test can be used to confirm the complete PEFS F3 system operates and performs as that
intended as when originally commissioned.
Please refer to the Chubb PEFS F3 Vehicle Fire Suppression System SDS prior to carrying out the Discharge Test.
Discharge of foam solution must be handled according to national or local waste regulations. Permission must be
granted from the site representative before carrying out the discharge test.
1. Check system pressure is reading in the green sector on the pressure indicators located on the cylinder valves
and manual actuators.
2. Discharge the PEFS system using the furthest located LOP manual actuator
3. Confirm all nozzles discharge and produce conical spray pattern.
4. Check that the nozzle discharge patterns cover the fire hazard area as specified in the commissioning
documentation.
5. Check that all monitoring and control panel alarms, shutdown and ancillary functions operate as intended
6. Record the Effective Discharge Time (EDT) and compare it to the EDT recorded during commissioning.
Storage containers (Item 10)
1. Remove discharge hose (3) from cylinder valve (4).
2. Fit end cap to discharge outlet port to prevent accidental discharge.
3. Remove Schrader valve cap from filler port assembly (1).
4. Depress Schrader valve core to release cylinder pressure.
5. Check that the pressure indicator on LOP Cylinder Valve (4) shows 0kPa.
6. Reinstall Schrader valve cap.
7. Remove actuation hose (2) from top of cylinder valve (4).
8. Remove filler port assembly (1)
9. Remove foam solution from the cylinder.
10. Check all cylinder burst disk assemblies are not damaged. Use of a vinyl protective cap over the burst disk
assembly is recommended to prevent ingress of dirt and wear on the burst disk surface.
11. Visually inspect exterior of all installed cylinders. Where a cylinder is dented, scored, pitted or otherwise
damaged by corrosion and it cannot be determined if the damage is within the limits as detailed in AS 2337.1,
then the cylinder shall be condemned.
12. Visually inspect interior of all installed cylinders. Where a cylinder is damaged by corrosion and it cannot be
determined if the damage is within the limits as detailed in AS 2337.1, then the cylinder shall be condemned.
13. Check the manufacture date and or last pressure test date of all installed cylinders. If this exceeds five years
old then the cylinder will require an inspection and hydrostatic test in accordance with AS2030.5 and
AS2337.1.
14. Check brackets are not damaged and secure.
15. Re-fit and secure cylinders into brackets.
Figure 2
3
1
2
4