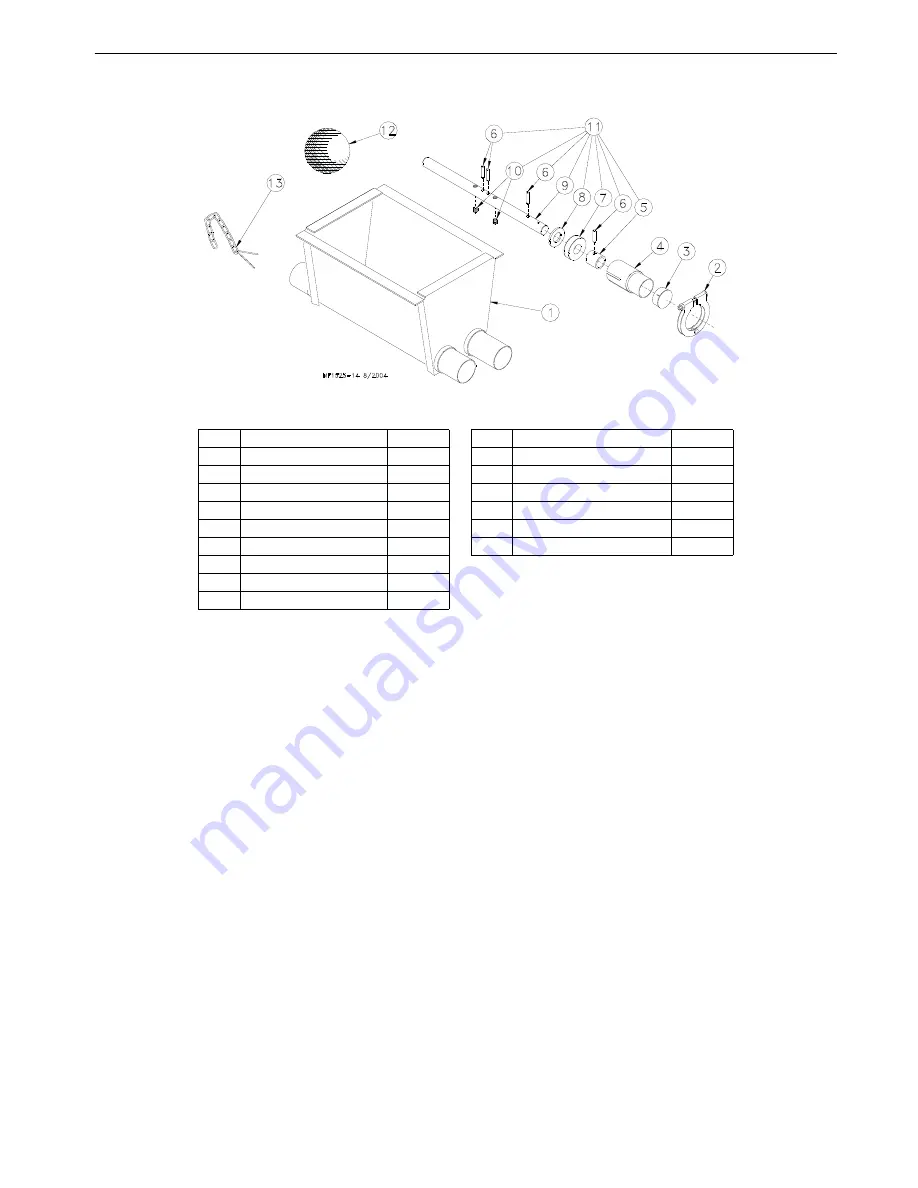
MODEL C2® Plus & MODEL G™ Plus Feeding System
Parts Listing
MF1255C
45
Twin Boot Components Part No. 6824
*The Jumper Wire Kit includes an insulated piece of High-Voltage Wire (part no. 28994) and (2) cable clamps.
Item Description
Part No.
Item Description
Part No.
1
Boot Weldment
3932
10
Setscrew
47867
2
Tube Clamp
24063
11
Anchor and Bearing Ass’y
39372
3
Cap
29373
12
Cannonball
3531
4
Outlet Tube
4556
13
Latch Pin Ass’y
2683
5
Sleeve
5648
--*
Jumper Wire Kit
5960
6
3/16 x 1" Pin
2960-1
--
Danger Decal
2527-9
7
Bearing
2689
8
Washer
2955-14
9
Anchor
38540