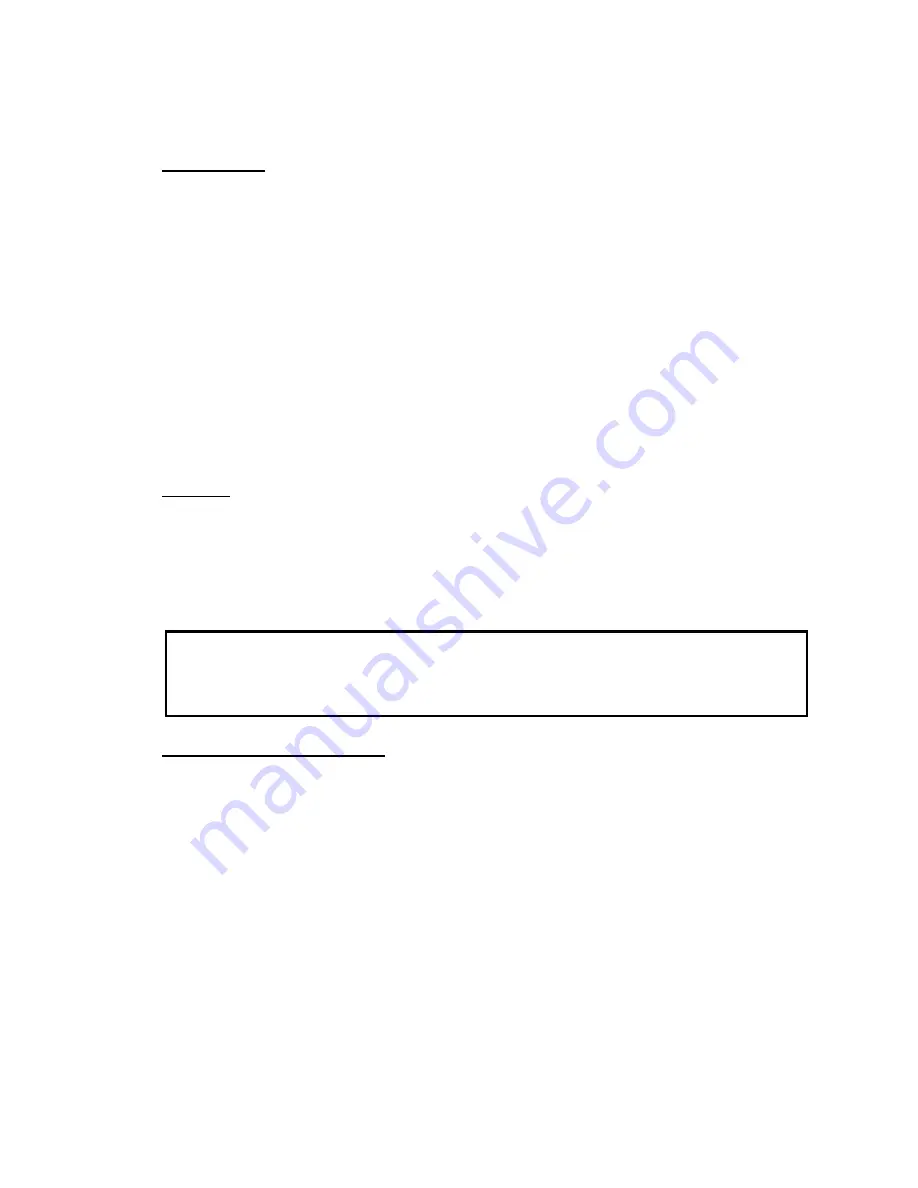
Chemtrac Systems, Inc.
Page 37
proportional band constant so that the max change in PUMP Output as the reading is
changing would be 3 to 5%. We say 3 to 5% and not just 5% because you have to
consider the lag time and the Integral Time setting and its effect upon the pump output.
Integral Time
A basic rule for setting the Integral Time constant setting is that the longer the lag time,
the higher integral time constant should be. Unlike Proportional Band which actually
responds to the changes in the SCV deviation, Integral Time only responds to the time
the deviation last and will continue to correct the pump output for as long as the SCV
stays away from the setpoint value (even if the deviation is not changing). A good
example of this would be to place the controller into manual while the SCV is at the
setpoint value and then decrease the Pump Output by 10%. Once the reading has
completely stabilized at a more negative value, place the controller into Automatic mode.
Since the reading will be stable at first, but away from the setpoint, the amount of Pump
Output change you note on the display is being controlled by the Integral Time constant
setting. Proportional Band will have no effect on the Pump Output until the SCV starts
to change as a result of the higher dosage of chemical finally reaching the sensor.
During the time when the SCV is stable (but not at the setpoint), you can note how much
the Pump Output is changing and if it appears to be making too small or too large of an
adjustment, simply change the Integral Time constant setting accordingly.
PID Rate
The PID Rate function serves to improve the controllers response when higher
Proportional Band and Integral Time settings appear to still be too responsive for the
application.
The PID Rate setting is usually left at 1 for most applications
since
proper setting of P Gain and Integral Time are capable of providing proper response.
Higher PID F settings will serve to buffer the responsiveness of the Controller. The PID
Rate setting should not exceed 10.
NOTE
R
There will normally be a small amount of cycling for a few minutes after a process
change, even if Proportional Band, Integral Time, and PID Rate are set correctly.
Output Limits (Min and Max)
The output limits define the maximum and minimum values of the pump control output
signal. This control can be used to limit the % output of the controller, high or low. On a
4-20 mA controller with Max: 50%, the Output would never be greater than 12 mA, i.e.,
the chemical pump could not go above 50% output. This function can be used as a
safety measure to prevent overfeed or underfeed.
3.8
AUTOMATIC CONTROL SETUP
The controller can be programmed while it is operating in the AUTOMATIC mode.
When the controller is in the SET-UP mode, displays can be altered to review and adjust
the tuning constants. Control action continues undisturbed, except for the normal
consequences of changing a certain parameter.
The AUTO or Manual control mode is indicated on the MAIN screen. To switch between
AUTO or Manual control mode can be done by pressing both
p
and
q
keys from the
MAIN screen. When in AUTO control mode, the pump output percent will increase or
decrease automatically in response to deviations from the setpoint.
Содержание SCC3500XRD
Страница 2: ......
Страница 41: ...Chemtrac Systems Inc Page 40 This page intentionally left blank ...
Страница 47: ...Chemtrac Systems Inc Page 46 This page intentionally left blank ...
Страница 53: ...Chemtrac Systems Inc Page 52 This page intentionally left blank ...