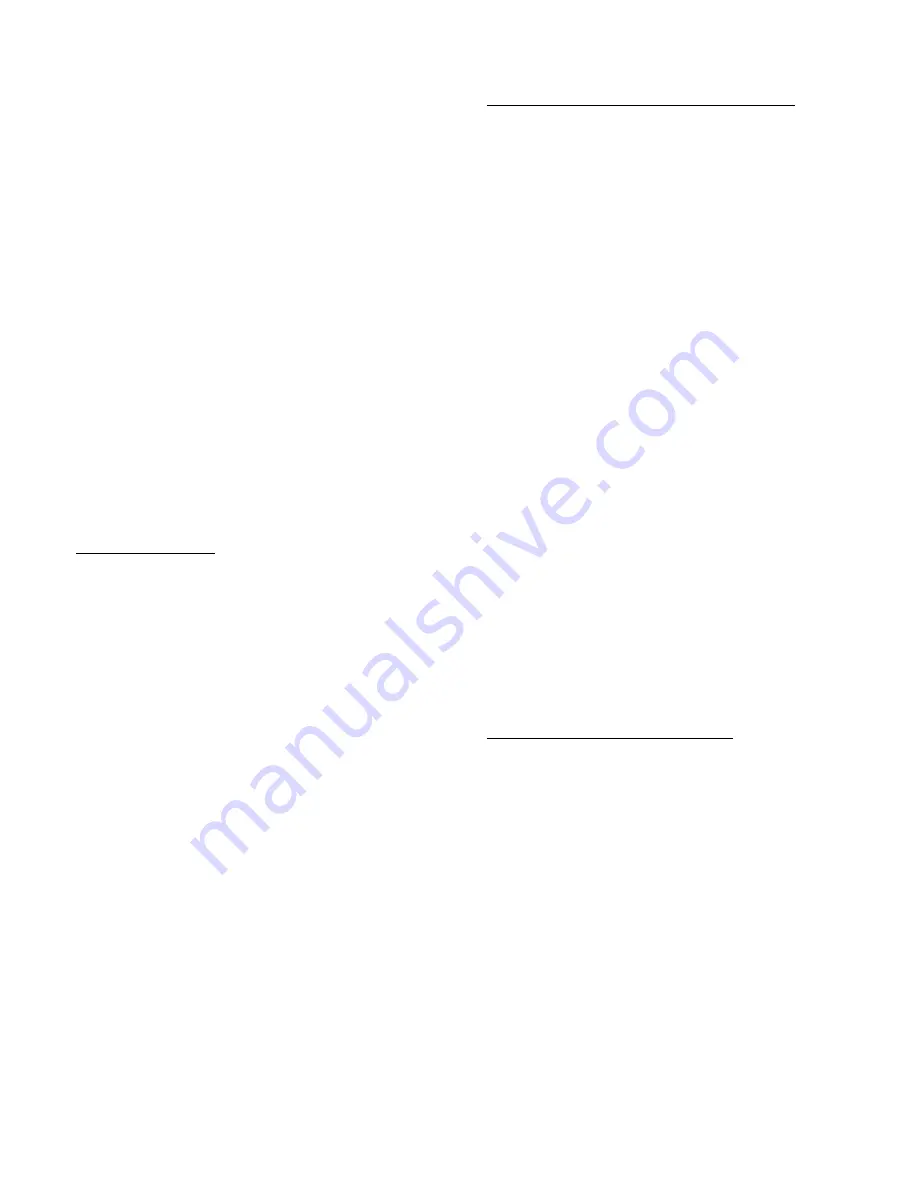
Model DX77
Installation, Operation and Maintenance
Page
4
Rev 06/17/2020
DX77-IOM-A.doc
R
ECEIVING
The shipment should be thoroughly inspected as
soon as it is received. The signed bill of lading is
acknowledgement by the carrier of receipt in good
condition of shipment covered by our invoice.
If any of the goods called for on this bill of lading are
shorted or damaged, do not accept them until the
carrier makes a notation on the freight bill of the
shorted or damaged goods. Do this for your own
protection.
NOTIFY
Challenger Lifts
AT ONCE if any hidden
loss or damage is discovered after receipt.
IT IS DIFFICULT TO COLLECT FOR LOSS OR
DAMAGE AFTER YOU HAVE GIVEN THE CARRIER
A CLEAR RECEIPT.
File your claim with
Challenger Lifts
promptly.
Support your claim with copies of the bill of lading,
freight bill, and photographs, if available.
A
CCEPTED
O
ILS
–
Do not use oils with detergents
Hydraulic fluid is not provided with the lift shipment
-10
wt.
anti-foam, anti-rust hydraulic / biodegradable oil
-Dexron III ATF
I
NSTALLATION
I
MPORTANT
:
Always wear safety glasses while installing lift.
T
OOLS
(
MINIMUM REQUIRED
)
a. Tape measure, 16ft
b. Chalk
line
c. 4ft
level
d. 10” adjustable wrench
e. Standard open end wrenches 9/16”, 3/4"
f. Needle
nose
pliers
g. Hammer drill with 1/2” diameter carbide tipped
bits
h. 2lb
hammer
i. Torque wrench: 40 foot pounds minimum with
3/4” socket
j. Allen Wrench 8mm
k. Long oil funnel
S
URFACE
M
OUNT
&
F
LUSH
M
OUNT
L
AYOUT
1) Layout the service bay according to the architect’s
plans or owners instructions
(see Fig. 1
).
Failure
to install in this orientation can result in
personal and property damage.
Be certain that
the proper conditions exist, see page 3.
NOTE: The correct orientation of the platforms
(DX & SX) is critical for proper layout of the lift.
The SX pad contains the longer air line which
is located under the front pivoting ramp.
2) See
Fig. 2
for control console location.
Relocating the control console further away than
the standard distance will require the installer to
provide suitable hydraulic hoses and air line.
Additional hose covers will also be needed if
installing lift in surface mount configuration.
Hydraulic hoses should be 1/4" minimum ID with
a minimum working pressure of 3000 psi and a
minimum burst pressure of 12,000 psi with #6 JIC
Swivel Female fittings. The air line for the locks
requires Ø6mm OD x 1mm wall poly tubing.
NOTE: Extend both hydraulic hoses the same
length and do not extend the hoses more than
21 feet [252 in].
3) Relocating the control console from DX to SX
side will require moving the green hose blocks at
the base of the unit under the ramp to direct the
hoses to the new side.
4) If the platform spacing is more than 27” wide
such as for wide electric vehicles, an extension
for the hydraulic hose and airline may be required
to locate the control box in desire location. See
Step #2 for hose and airline specs. For Wide
Electric Vehicles, please refer to DX77-SUP-T
provided with the optional hose cover (10354-4).
F
LUSH
M
OUNT
P
IT
R
EQUIREMENTS
5)
PRIOR TO POURING CONCRETE
, installer will
need the Flush Mount Kit (Part# DX77-FM).
Please contact the phone number listed on the
front cover of the manual for additional assistance.
The kit contains frame components with concrete
ties that will need to be in place during concrete
pour. See parts breakdown in the back of the
manual for included components. Temporary pit
forms are not provided and will be the
responsibility of the installer.
6) For flush mount pit specifications, see
Fig. 3
.