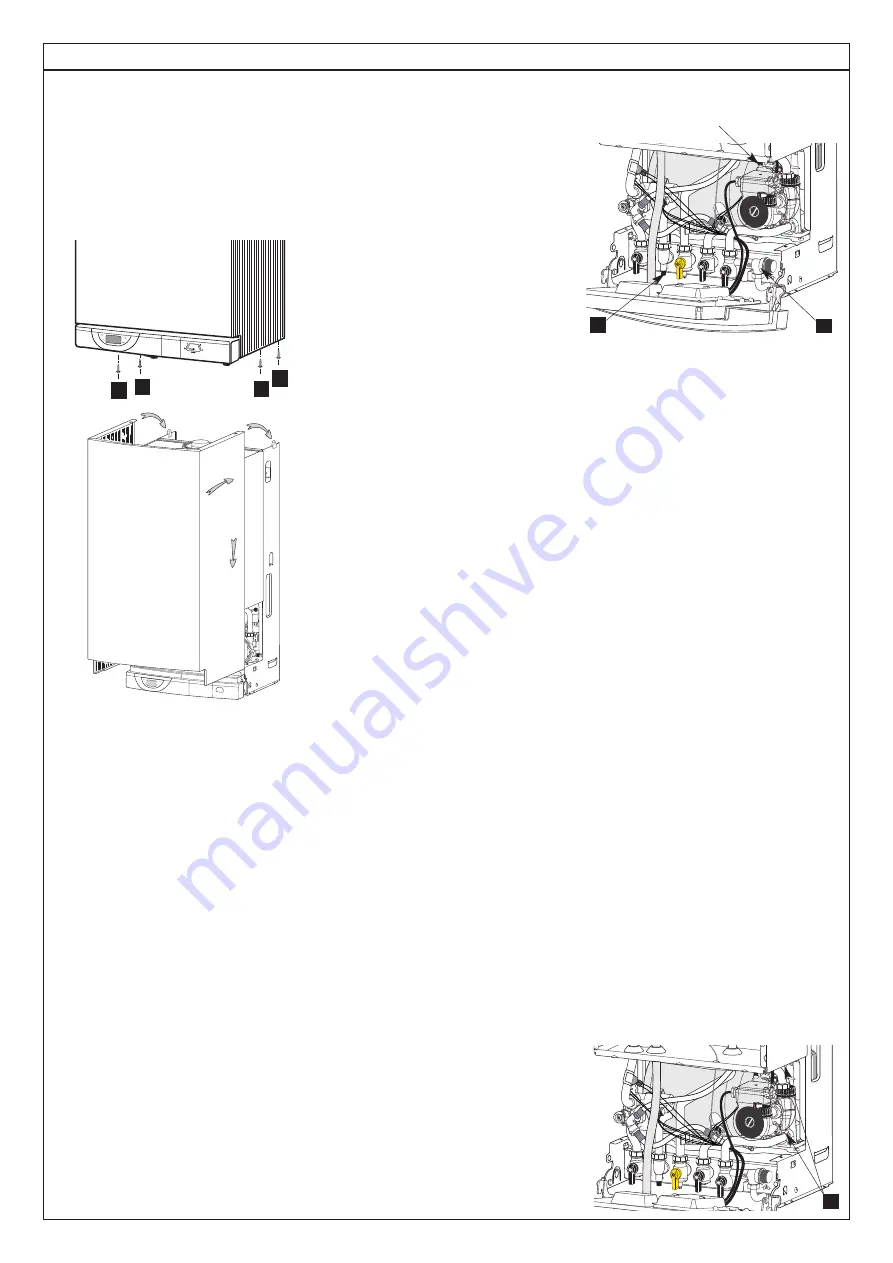
12
REMOVAL AND REPLACEMENT OF PARTS
Before removing the appliance case,
isolate the gas and electrical supplies.
Isolate the boiler from the system and
drain before removing any component in
the waterways. Ensure that the appli-
ance is cool.
1. Outer Case
Remove the four screws
A in the bottom
of the case and lift free. When replacing,
carefully locate on lugs
T on the top
edge of the chassis.
2. Sealed chamber front panel
Unscrew the four self tapping screws
securing the sealed chamber front panel
and lift over the top corner locating lugs.
Reassemble in reverse order.
3. Combustion Chamber front panel
and air/gas connection
Carry out steps 1 and 2 as above.
Unscrew the three screws securing the
air/gas connection pipe onto the gas
valve assembly. Disconnect the ionisa-
tion and lighting electrodes from their
wiring. Unscrew the six nuts to release
the combustion chamber front panel and
pull the assembly towards you.
Reassemble in reverse order.
4. Ionisation electrode
Carry out steps 1 and 2 as above.
Disconnect the ionisation electrode from
its wiring. Loosen the 2 screws and pull it
out from the combustion chamber front
panel. Replace the ionisation gasket
provided. Reassemble in reverse order.
5. Lighting electrode
Carry out steps 1 and 2. Disconnect the
lighting electrode from its wiring. Loosen
the 2 screws and pull it out from the
combustion chamber front panel.
Replace the ionisation gasket provided.
Reassemble in reverse order.
6. Burner
Carry out steps 1, 2 and 3. Remove the
4 Philips screw retaining the burner onto
the combustion chamber. Pull it out with
care to avoid any damage to the ceramic
panel protecting the combustion cham-
ber front panel. Replace the burner gas-
ket. Reassemble in reverse order.
7. Gas vale assembly
Carry out steps 1 and 2 Unscrew the
three screws securing the air/gas con-
nection pipe onto the gas valve assem-
bly. Disconnect the connectors from the
gas solenoids and fan. Loosen the gas
pipe nut. Unscrew the six nuts to
release the combustion chamber front
panel and pull the assembly towards
you. Replace the gas filter before fitting
the full assembly back into the boiler.
8. Fan assembly
Carry out all the operations mentioned in
step 7. Unscrew the three screws secur-
ing the air/gas connection pipe onto the
gas valve assembly. Separate the gas
valve assembly and the venturi from the
fan assembly by loosening the two
hexagonal head screws. Reassemble in
reverse order and replace all necessary
gaskets.
9. Gas section
Carry out all operations mentioned in
step 7. Unscrew the three screws secur-
ing the air/gas connection pipe onto the
gas valve assembly. Separate the gas
valve assembly and the venturi from the
fan assembly by loosening the two
hexagonal head screws. The venturi and
the gas section can be separated by
loosening the 2 screws located at the top
of the gas valve. Replace all necessary
gaskets before reassemble in reverse
order.
10. Venturi in the gas section
Carry out all operations mentioned in
step 7. Unscrew the three screws secur-
ing the air/gas connection pipe onto the
gas valve assembly. Separate the gas
valve assembly and the venturi from the
fan assembly by loosening the two
hexagonal head screws. The venturi and
the gas section can be separated by
loosening the 2 screws located at the top
of the gas valve. Replace all necessary
gaskets before reassembling in reverse
order.
11. Drain down
2 drain points are located on the boiler.
1 = DHW circuit drain point
2 = Heating circuit drain point
12. Water filters ( DHW and Heating)
The DHW filter ensures a seal between
the connecting bracket and the pipe to
the DHW flow switch. Drain the boiler as
in step 11. Unscrew the pipe nut and
remove the clip on the hydraulic assy.
Pull the pipe toward you and remove the
water filter from its location.
The C.H. filter is located in the right
hydraulic assembly. Remove the return
pipe as described previously and with-
draw the filter. Reassemble in reverse
order.
13. Flow switches
Drain boiler as in step 12. Disconnect
the electrical plug, turn the top cover
anti-clockwise, remove the O-ring and
the brass piston. Reassemble in reverse
order.
14. 3-Way valve
Drain boiler as in step 12. Remove the 3
clips on the 3 way valve. Remove the
clip on the exchanger flow pipe. Pull the
pipe down then pull it out of the 3 way
valve. Disconnect the plug from the
motor. Unscrew the nut on the pipe
between the connecting bracket and the
3 way valve and pull it toward you.
Rotate the 3 way valve body anti-clock-
wise to unclip it from the left hydraulic
assembly.
15. Secondary heat exchanger
Drain both circuits of the boiler as in step
12. Unscrew the 2 fixing screws
D and
remove the DHW exchanger from the
front. Prior to reassembly, check that the
4 gaskets are correctly positioned. The
heat exchanger is so designed that it
A A
A
A
T
T
1
2
1
2
air separator
D