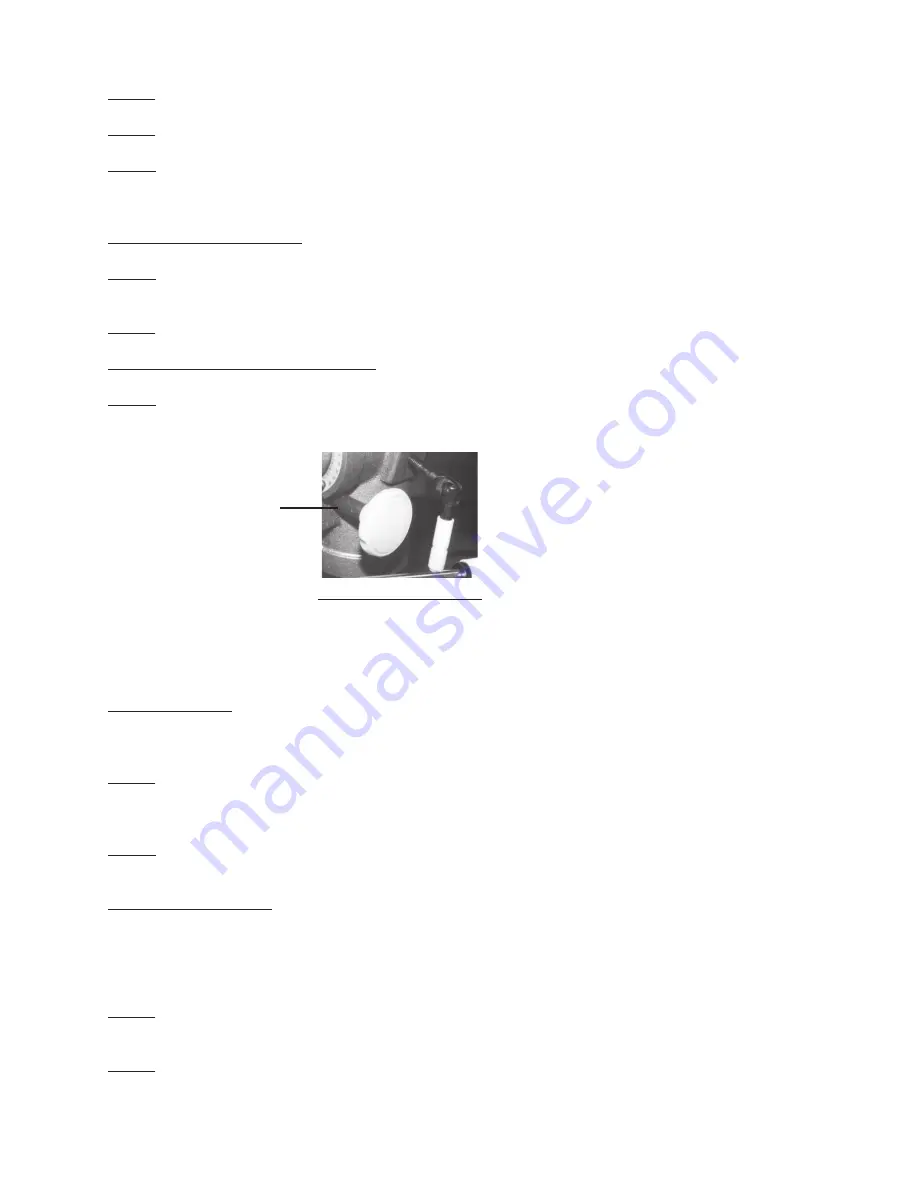
Step 2)
Align the mark on the Guide Column (#18B) with the Scale (part #33B).
Step 3)
Once the Head is tilted to the desired angle, re-tighten the Clamping Lever.
Step 4)
To move the Head (part #14B) back to its original position, loosen the Clamping Lever (#30B)
and pull up the Guide Pin (#16B). Turn the Guide Pin until the cross pin slides back into the
slot. Tighten the Clamping Lever (#30B).
Moving the Head Horizontally
Step 1)
Loosen the left Clamping Lever (#30B) and rotate the Head 360 degrees
to the desired position.
Step 2)
Fasten the Clamping Lever (#30B)
Moving the Head Forward and Backward
Step 1)
Loosen the right Clamping Lever (#30B). Turn the Moving Bar (part #32B), rotating it back and
forth if necessary - see Figure 6. Place the head in the desired position and re-tighten the
Clamping Lever (#30B).
To ensure that the drill is entirely perpendicular to the table, insert a piece of straight round bar in the chuck,
place a Square on the Table and bring it up to the round bar. Adjust the Table tilt if necessary so that the Table
is correctly aligned.
To Adjust the Table
The table is capable of being raised and lower by taking the following steps.
Step 1)
Turning the Crank (part #8C) clockwise will elevate the Table (#20C); turning the Crank
counterclockwise will lower the Table. The Table Clamp (#13C) must be released before
using the Crank.
Step 2)
You can tilt the Table by loosening the Hex Bolt (part #12C), tilting the table to the
desired position (up to 45 degrees) and re-tightening the Hex Bolt.
Setting the Drilling Depth
Located on the side of the Hub (#36B) is the Depth Stop Ring (part #37B) and the Depth Lock Screw
(part #38B) This allows the depth of the hole to be set so that you may drill a series of holes each to the
same depth - see Figure 7.
Step 1)
With the Depth Lock Screw loose, set the Scale on the Depth Stop Top Ring (part #37B) to the
depth of the hole desired.
Step 2)
Tighten the Depth Lock Screw (#38B) until secure.
The Drill is now set to drill holes to the desired depth.
Moving Bar (32B)
Figure 6 - Moving Head
#42289
Page 8
Brought to You by Augusta Flint