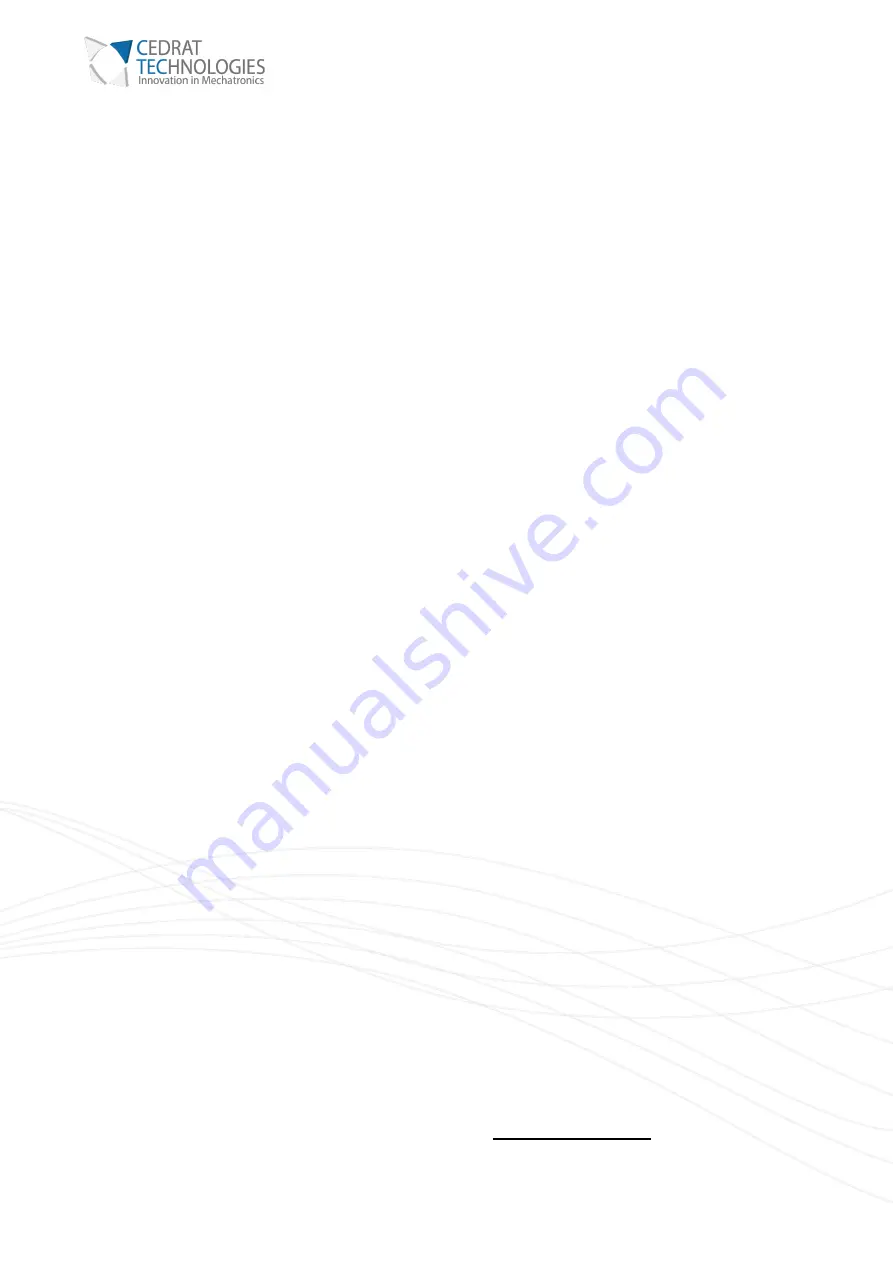
8 / 32
CCBU40 COMPACT CONTROLLER BOARD - PRODUCT AND WARRANTY INFORMATION
Version 1.21
V.3. ARCHITECTURE
The architecture of the CCBu40 is represented schematically on the Figure 2 or Figure 3 depending on the
selected sensor. On the figure, the commands for adjusting the configuration are identified wi
th ‘’ marks. The
details of the commands are given in Section 0. The CCBu40 has two fully independent control channels, thus
it is able to control a 2-axis push-pull mechanism, or 2 single axis piezo-mechanisms. The structure of the
channels is identical, as can be noticed on the figures.
In standard, the CCBu40 features two SG sensors conditioners (one per channel) which provide a voltage
output between ±10V corresponding to the position measurement. Alternatively, the CCBu40 exists in optional
hardware configuration without SG conditioning. In that case, the ±10V sensor signals are provided directly on
the mechanism connector, and no conditioning is applied. The sensor measurements are sampled by the
controllers to perform closed-
loop control. Those measurements can be read using the analog outputs “SX” and
“SY”, or through the digital link.
For driving the piezo actuators, the CCBu40 features 3 high voltage power amplifiers. The first power amplifier
provides the +130V in case a push-pull mechanism is controlled, and its output voltage is fixed. The 2 other
amplifiers are controllable, and each is associated to a control channel. Those amplifiers have an approximate
gain of 20V/V. They take a command voltage between [-1V ; +7.5V], and output a voltage to the piezo-actuators
in the range of [-20V ; +150V] approximately.
The user has the possibility to set limitations on the commands before they are applied to the amplifiers. This
can be very convenient to protect the system when tuning the closed-loop control in case some instability would
occur. Once the closed-loop is properly tuned and robust, the user can set again the limitations to the maximum
values [-20V ; +150V] to achieve full stroke.
The internal digital preamplifier is set to translate from customized range order to standard range order
[-1V;
+7.5V]
There is one digital controller per channel of the CCBu40, and they are independently configurable. The details
on the closed-loop controllers are given in the Section 0. The user can configure the board to operate with
analog ±10V commands from the “AIX” and “AIY” inputs, or to operate from the digital commands sent through
the digital communication. The user can also select between open-loop and closed-loop operation:
•
In open-loop operation, the commands are fed to a preamplifier if the input range is customized and
then the power amplifiers.
•
In closed-loop operation, the commands are fed to the closed-loop controllers. The closed-loop
controller outputs are controlling the power amplifier inputs. The role of the closed-loop controller is to
make sure that the sensor signal voltage equal to the command voltage. This means that the
command gain is equal to the sensor gain, and the user should provide commands that are in the
range of the sensor output. If the command is not in the sensor output range, the controller will simply
saturate.
Optionally, the mechanism can integrate a PT1000 temperature sensor, as well as a DS2431 1-wire memory.
Those functions are optional and thus not represented on the figures. The DS2431 memory is an option that
can be used for storage of calibration data upon specific customer request, this option is managed only by
Cedrat Technologies.
For the optional temperature sensor, this can be managed by Cedrat Technologies as an option directly
integrated on the mechanism or actuator. If the customer is responsible for the wiring of the mechanism or
actuators, he has the possibility to integrate the sensor himself. The sensor should be of type PT1000, and it
should be connected between the “T°C” and “GND” pins of the
mechanism connector
. The temperature signal