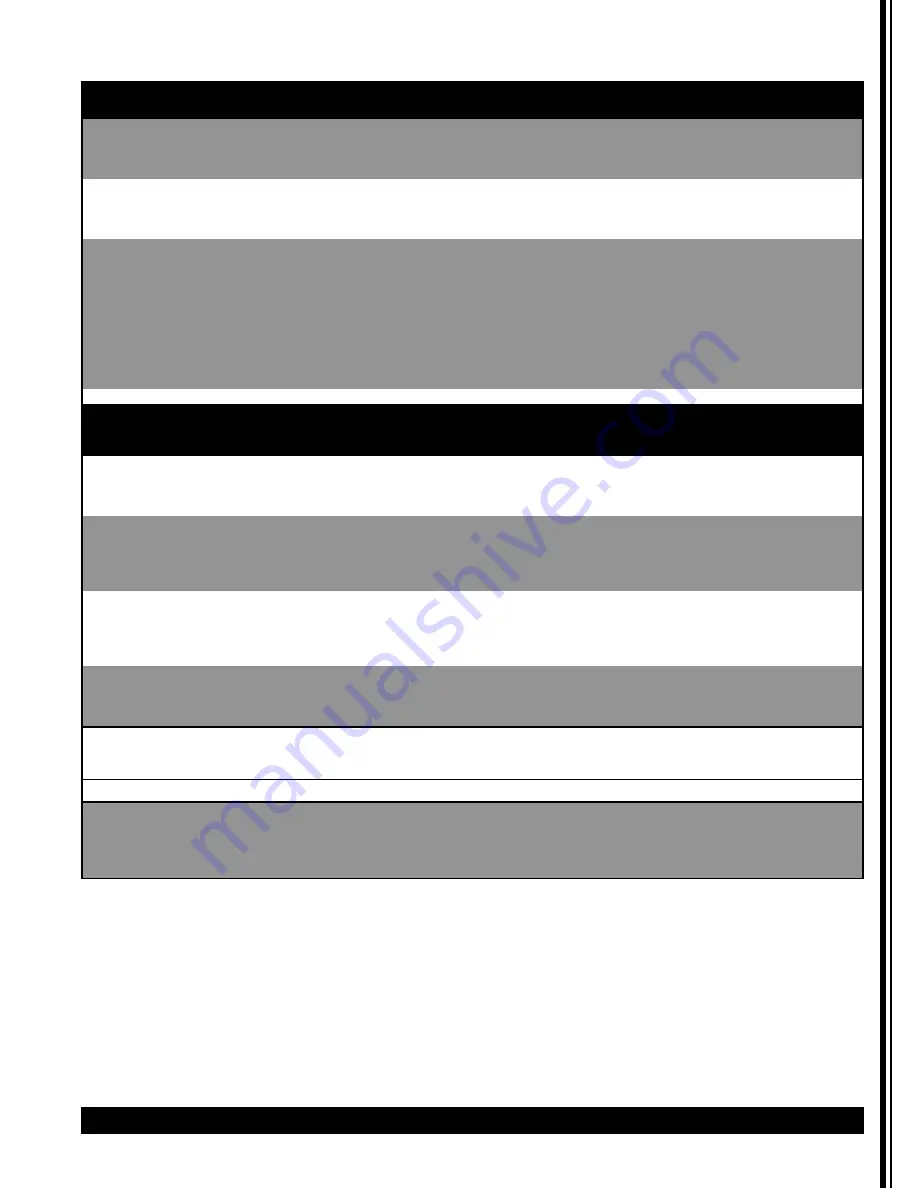
Radiance Technical Service Manual
Cecilware
®
31
Troubleshooting Guide (continued)
Machine Level Faults:
Fault #
Fault Definition
Corrective Actions
FAULT 4
Tank temperature probe is out of
• Verify that the appropriate power supply is connected to the machine
range (i.e. it is too hot, too “cold” or
• Verify that the heating connections to the heating element are good
there is an open or short circuit on
• Cycle the main power switch to reset machine and verify operation
the pin that reads the temperature)
• Call Technical Service if issue is not corrected
FAULT 5
The tank temperature is not rising as
• Verify that the appropriate power supply is connected to the machine
expected
• Verify that the heating connections to the heating element are good
• Cycle the main power switch to reset machine and verify operation
• Call Technical Service if issue is not corrected
FAULT 6
The tank is not being filled as expected • Verify that water supply is connected and turned "on" to unit
• Verify that there are no restrictions in the water supply line
• Verify that the water valve is connected to power
• Verify that the tank float switch is connected
• Cycle the main power switch to reset machine and verify operation
• Verify that all of the connectors to the Tank board are attached
• Call Technical Service if issue is not corrected
The tank has overflowed
• Verify that the float switch is operating properly
• Verify that the float switch is connected to the system
• Call Technical Service if issue is not corrected
Machine Level Faults:
After 30 seconds of not receiving a message from a board, these faults are activated:
Fault #
Fault Definition
Corrective Actions
FAULT 11
Tank communications Timeout
• Verify that the connectors to the tank board and Main Control board are good
• Check for damaged wires due to previous service, installation, or maintenance
• Cycle the main power switch to reset machine and verify operation
• Call Technical Service if issue not corrected
FAULT 12
IO Communications Timeout
• Verify that the connectors to the IO Boards and the Main Control boards are
good
• Check for damaged wires due to previous service, installation, or maintenance
• Cycle the main power switch to reset machine and verify operation
• Call Technical Service if issue not corrected
FAULT 14
BDCS bus timeout (two or more
• Verify that the connectors to all of the circuit boards and the Main Control boards
boards are not communicating to the
are good
main board)
• Check for damaged wires due to previous service, installation, or maintenance
• Cycle the main power switch to reset machine and verify operation
• Call Technical Service if issue not corrected
FAULT 16
Communication fault between two
• Verify that the connectors between the two Main Control boards is good
main boards
• Check for damaged wires due to previous service, installation, or maintenance
(Radiance 10 Units only)
• Cycle the main power switch to reset machine and verify operation
• Call Technical Service if issue not corrected
(Communications issues can occur due to Electro-Magnetic Interference at a particular installation. A dedicated power circuit for the
unit is required. However, the equipment that is installed near the machine can also be affecting the communications.)
Dispense Head Level Faults:
FAULT 15
Key Pressed Fault (If the dispense
• Check for damaged wires due to previous service, installation or maintenance
button is held for longer than 45
• Cycle the main power switch to reset machine and verify operation
seconds, this fault will appear, and
• Call Technical Service if issue not corrected
the dispense will stop. This is a head
specific fault.)