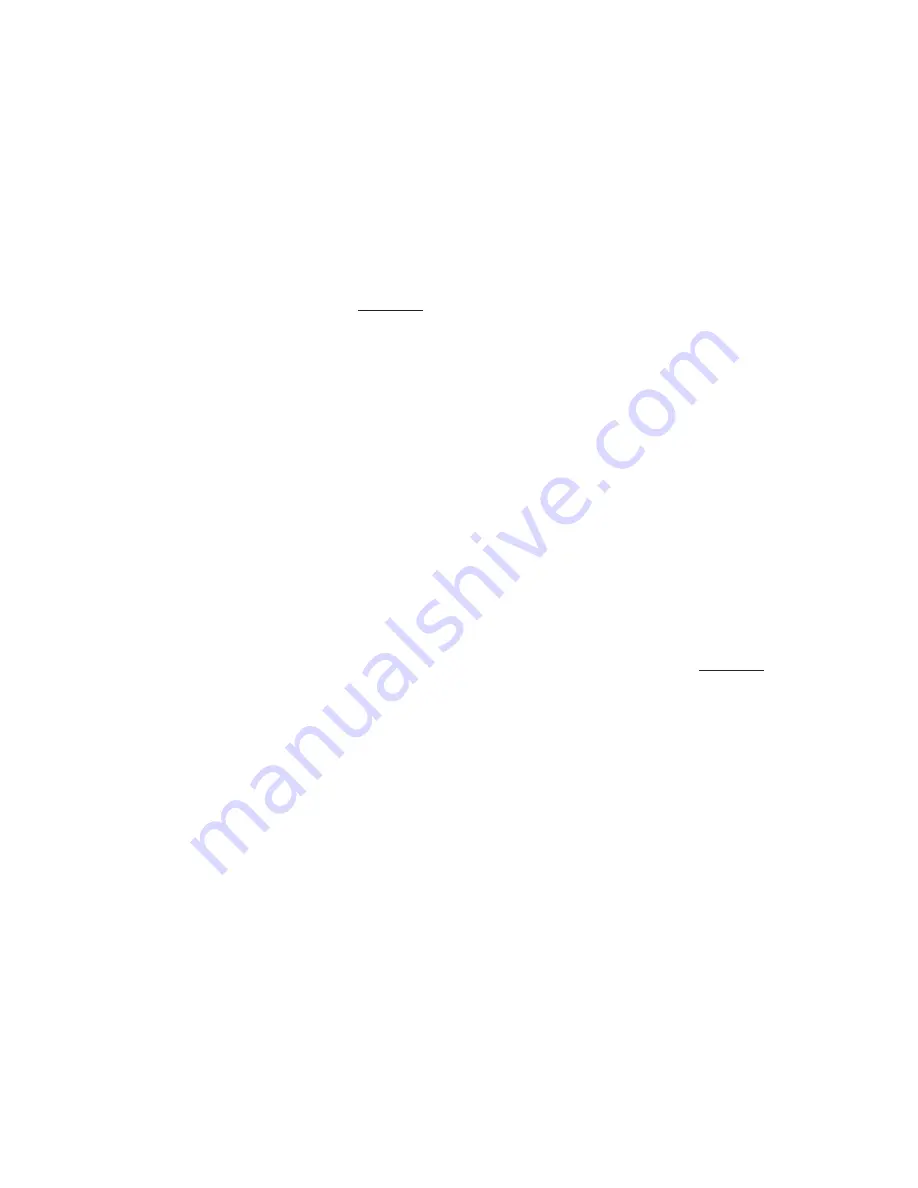
IOM-SLR-2
10
CW by hand onto the threaded portion of
the body (1) until firmly seated against
the diaphragm gasket (10). Tighten to the
fol low ing torque val ue:
65–70 Ft lbs (88–95 Nm).
12. Pressurize with air and spray liquid leak
de tec tor around body (1) and spring cham-
ber (6) to test for leakage. En sure that an
outlet pres sure is main tained during this
leak test of at least mid-range spring level;
i.e. 2-100 psig (.14-6.9 Barg) range spring,
51 psig (3.5 Barg) test pres sure min i mum.
Rotate knob (4) CW to obtain set point.
L. Trim Replacement - (Loader w/2 - 750 psig
range springs)
1. Remove spring chamber subassembly
and diaphragm subassembly per Steps
K.1. – K.6 previous.
2. With a 5/16" socket - rotate seat retainer
(13) CCW to remove from the body.
3. Remove poppet (8) and poppet spring (9).
4. Remove the pressed in seat (12) from
retainer (13).
5. Clean debris from within the body (1) cav-
ity. Clean all parts to be reused according
to own er's pro ce dures.
NOTE:
On reg u la-
tors origi nally sup plied as “oxygen clean”,
Option-55, main tenance must in clude a
level of clean li ness equal to Cash co's
clean ing stan dard #S-1134.
6. Inspect all parts for damage and replace
if necessary.
NOTE:
Use only parts
man u fac tured and supplied by Cashco,
Inc. for these products. See Section X.
7. Place the body (1) into a soft-jawed vise,
grasp the flats on the body.
8. Press the seat (12) into the seat retainer
(13) with the chamfer side of the seat
inserted first.
9. Place poppet spring (9) into body (1) cav-
ity.
10. Place poppet (8) inside the poppet spring
(9). The angled seating surface of the
poppet (8) must face up toward the seat
(12).
11. Install new seat retainer (13) with seat (12)
into body (1) cav i ty with the seat facing
down ward toward the angled seat ing sur-
face of the pop pet (8). Tighten seat re tain er
to the following torque val ue:
6.25 Ft-lbs (8.47 Nm).
12. Place a new diaphragm gas ket (10) onto
the body (1) diaphragm flange. Place di a-
phragm sub as sem bly on top of the gasket.
13. Lubricate the threads of the body (1) with
a light weight grease that is compatible with
service use. Ro tate the spring chamber (6)
CW by hand onto the threaded portion of
the body (1) until firmly seated against the
diaphragm gasket (10). Tighten to the fol-
low ing torque val ue:
65–70 Ft lbs (88–95 Nm).
14. Bench test unit for suitable operation.
NOTE:
Regulators are not tight shutoff de-
vices. Even if pressure builds up beyond set
point, a reg u la tor may or may not develop
bubble tight shutoff.
15. Pressurize with air and spray liquid leak de-
tec tor around body (1) and spring cham ber
(6) to test for leakage. En sure that an outlet
pressure is main tained during this leak test
of at least mid-range spring level; i.e. 2-100
psig (.14-6.9 Barg) range spring, 51 psig
(3.5 Barg) test pres sure minimum.
16. Install loader on mounting bracket and con-
nect inlet and outlet tubing.
M. Piston Replacement - (Loader w/50 - 1250
psig range springs)
1. Refer to Figure 9 for item numbers.
2. Securely the body (1) in a vise with the knob
(4) directed upwards.
3. Relax range spring (15) by turning knob (4)
CCW until rotation comes to a complete
stop.
NOTE:
It is not necessary to remove
the knob before removing the spring cham-
ber (6) from the body (1).
4. Remove spring chamber (6) by grasping the
flats and turning CCW. Upon removal, the
range spring (15), range spring clip (16), and
spring button (5) should remain inside the
spring cham ber.
5. Remove pusher plate (18).