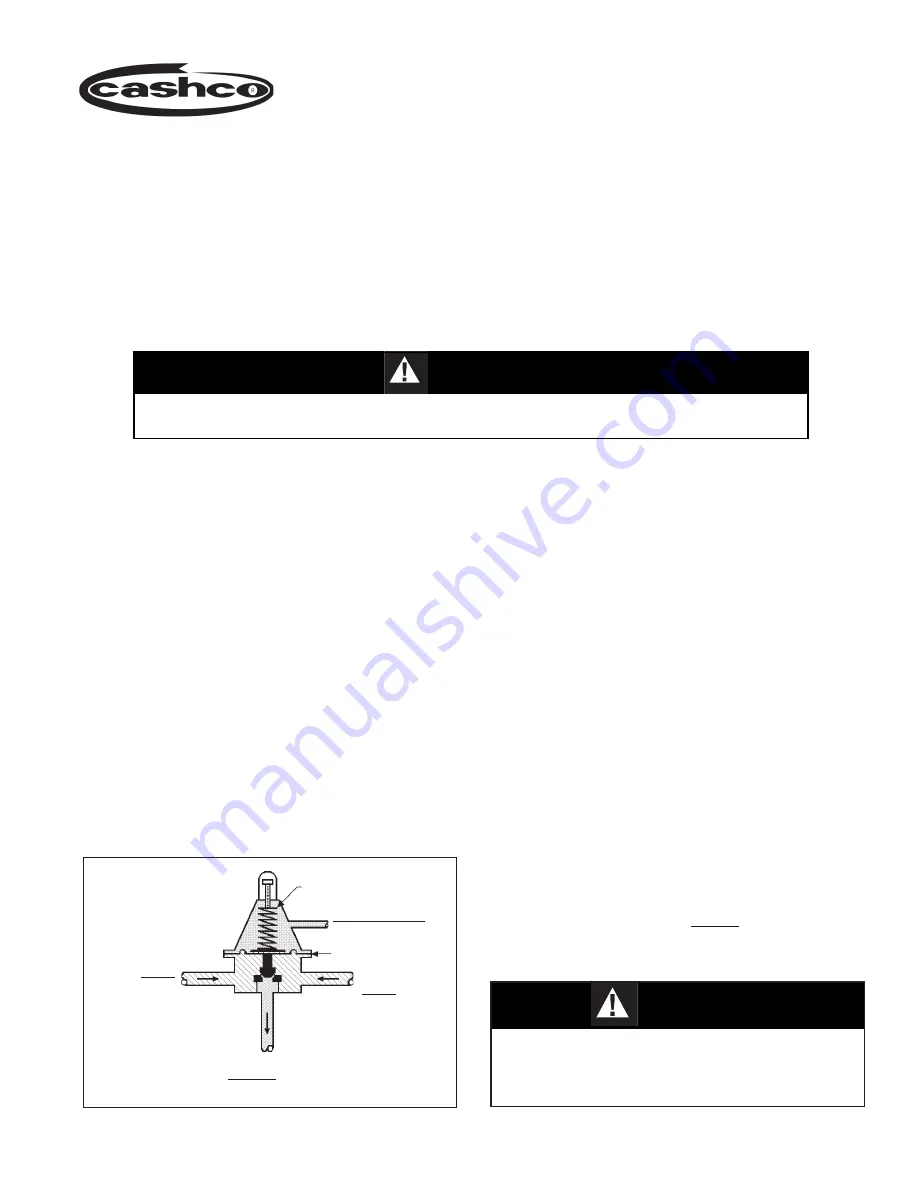
IIl. PRINCIPLE OF OPERATION
1. Movement occurs as pressure variations reg is ter
on the diaphragm (3). The registering pressure is
the inlet (P
1
) or upstream pressure which reg is ters
on the "un der neath" side of the diaphragm (3). The
second pressure registered is the loading (P
LOAD
)
pressure in the spring chamber (2) "above" the
diaphragm (3). The range spring (18) determines
the differential pres sure setpoint (P
SET
). As inlet
I. DESCRIPTION AND SCOPE
The Model 123-1+6+S Differential is designed for high pressure liquid or gas applications to Cashco drawing nos.
32934 (NACE construction) and 32935 (Non-NACE construction). It is used to control differential upstream (inlet or
P
1
) pressure and a loading (P
Load
) pressure to a rotating shaft seal. Sizes are 1/2", 3/4", 1", and 1-1/2" (DN15, 20,
25, and 40).
SECTION III
IOM-123 1+6+S
DIFF
02-16
MODEL 123-1+6+S DIFFERENTIAL
BACK PRESSURE / RELIEF REGULATOR
INSTALLATION, OPERATION & MAIN TE NANCE MANUAL (IOM)
SECTION I
SECTION II
II. INSTALLATION
This unit was designed and is used almost exclusively on compressor and turbo expander seal systems.
REFER
TO COM PRES SOR/EXPANDER MANUFACTURER'S MANUAL FOR DE TAILED INSTALLATION, START-UP
AND SHUTDOWN OF THIS UNIT.
Install regulator with Inlet (P
1
) pressure coming in the side body (1) connection
in accordance with the directional flow arrow cast on body (1).
∆
P
SIZING
= P
1
- P
2
P
1
> P
LOAD
P
1
= P
LOAD
+ P
SET
∆
P
DIFFERENTIAL
= P
1
- P
LOAD
LOADING FLUID
@ P
LOAD
DIA PHRAGM
RANGE SPRING:
SETTING @ P
SET
(Optional)
INLET
@ P
1
OUTLET @ P
2
Model 123-1+6+S Differential Schematic
(P
1
) pressure drops, the range spring (18) pushes
the diaphragm (3) down, clos ing the port; as
inlet (P
1
) pressure increases, the diaphragm (3)
pushes up and the port opens. As the loading
(P
LOAD
) pressure varies, the inlet (P
1
) pressure
tends to follow. An increase in (P
LOAD
) will increase
inlet (P
1
)
pressure by nearly an equal amount ;
a decrease in (P
LOAD
)
will decrease the inlet (P
1
)
pres sure.
2. A complete diaphragm (3) failure will cause the
fluids to mix in the spring chamber (2) or loading
pressure piping. Reg u la tor action will "fail close"
under a di a phragm (3) failure.
3. Under normal operating conditions, the inlet (P
1
)
pressure should be greater than the loading
(P
LOAD
) pressure by the range spring (P
SET
)
setpoint.
INLET
@ P
1
Limit any field hydrostatic test to 1-1/2 times the
Maximum Pressure Rat ing (See Ta ble 1). En sure
that the test pressure is applied uniformly to the
body inlet, body outlet, and spring chamber.
CAUTION
This is not a safety device and must not be sub sti tut ed for a code approved pres sure safety
relief valve or rupture disc. NOT FOR STEAM SERVICE. NOT FOR OXYGEN SERVICE.
CAUTION
ISO Registered Company