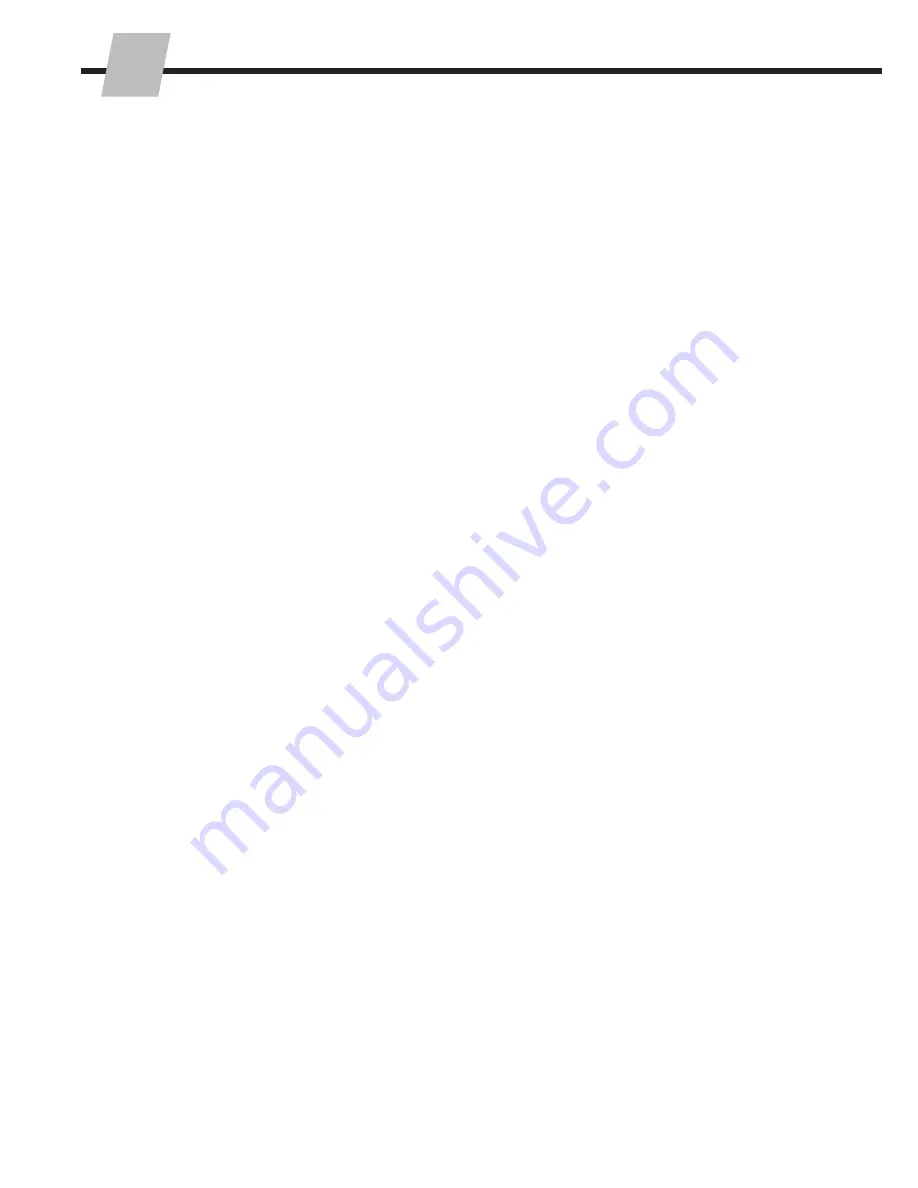
6817684
ERIODIC MAINTENANCE
P
3
2.3
2000-Hour Maintenance
After each 2000 hours of truck operation, in addition to
the 100 and 500-hour maintenance, perform the following
procedures:
•
Check all rotation bearing capscrews for proper torque
value. See Technical Bulletin TB183 or Section 4.5 for
inspection and replacement procedures.
•
Fork Inspection –
After 2000 hours of truck operation,
forks in use shall be inspected at intervals of not more
than 12 months (for single shift operations) or whenever
any defect or permanent deformation is detected.
Severe applications will require more frequent
inspection.
Fork inspection shall be carried out by trained
personnel to detect any damage that might impair safe
use. Any fork that is defective shall be removed from
service. Reference ANSI B56.1-2005.
Inspect for the following defects:
– Surface cracks
– Straightness of blade and shank
– Fork angle
– Difference in height of fork tips
– Positioning lock
– Wear on fork blade and shank
– Wear on fork hooks
– Legibility of marking
NOTE:
Fork Safety Kit 3014162 contains wear calipers,
inspection sheets and safety poster. Also available
is fork hook & carriage wear gauge 209560 (Class II),
209561 (Class III) and 6105257 (Class IV).
Содержание 220D
Страница 27: ...BLANK...