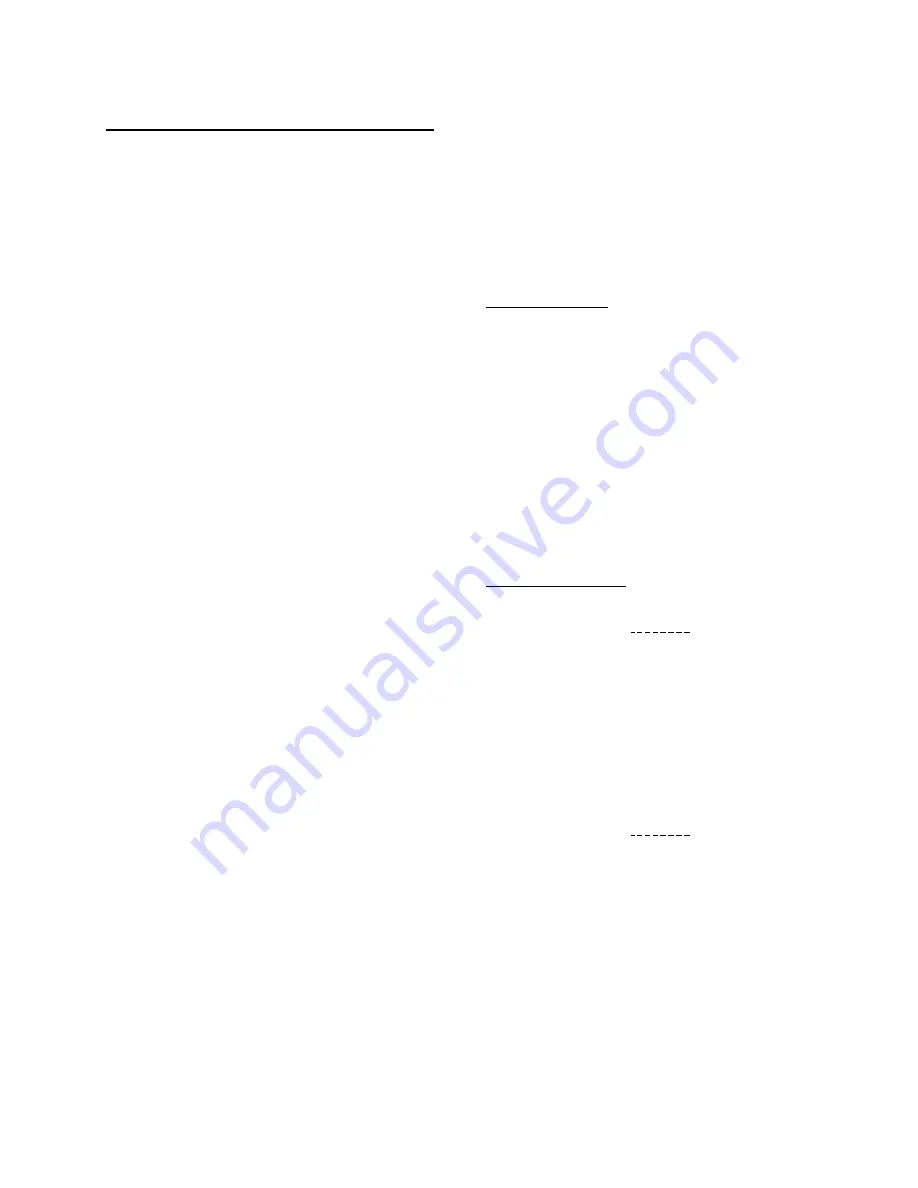
9
VII. MAINTENANCE.
Generally, the pump does not require continuous
supervision. Occasional visual checks are
recommended. Data should be recorded for each
pump to keep track of maintenance, which has been
performed and note operational problems. A pump
service record page is provided for this purpose in the
front of this manual.
A. FIELD INSPECTION.
Shutdown is not
required. Perform field inspection at regular intervals
and perform the following checks:
1. Check and record the suction and discharge
pressures to establish differential head. It
should conform to the pump nameplate.
2. Check and record the power input and speed
of the driver.
3. Check and record pumping temperatures.
4. Check pump for quiet running.
B. STUFFING BOX.
The stuffing box is equipped
with a throttle bushing which requires no regular
maintenance. The inside diameter of the throttle
bushing will increase with wear. The throttle bushing
should be inspected after pump disassembly. The
throttle bushing requires replacement if the inside
diameter is more than 0.020 inch out of round. Refer
to Table 2, Throttle Bushing Dimensions.
C. BEARING TEMPERATURE.
Bearing
temperature should be monitored periodically. Normal
operating temperatures are 120 degrees F to 160
degrees F, depending on the ambient temperature,
but should not run hotter than 180 degrees F.
Bearings may appear to run hot when pump is first
started. This is caused by the shaft seal, not the
bearing. When the seal is seated, temperature should
drop to normal.
Check bearing temperature by placing a pyrometer
against the bearing frame while pump is running. A
temperature rise above 180 degrees F indicates
possible damage that requires checking. The most
common cause of high bearing temperatures is
overgreased bearings.
D. BEARING LUBRICATION.
Lubrication
frequency depends on operating conditions. Normal
duty calls for relubrication every 1000 hours of
operation. Bearings are lubricated at Carver Pump
Company with Amoco Rykon Premium Grease No.
2EP, non-soap, polyurea thickened grease with a
drop point of 450 degrees F. This grease was
selected due to its suitability to extreme pressures
and its high temperature stability. Never mix greases
with differing properties.
Polyurea base greases are NOT compatible with
lithium or soda soap base greases. Therefore, the
type of grease added should not vary. However, if it is
necessary to change grease types, the bearings,
bearing frame, and bearing cap and/or cartridge
should be thoroughly cleaned and flushed with
suitable solvent to remove all traces of old grease. If
equipped, fill the bearing’s autogreaser. Remove
bearings in accordance with section VII, paragraph A.
For proper lubrication of bearings, use the following
procedures:
To properly lubricate driver bearings, refer to the
manufacturer’s specific instructions.
Grease Lubrication
1. Place bearings, bearing frame, and
bearing cap and/or cartridge in a wire or
mesh basket and suspend the basket in
a light mineral solvent. Allow it to soak,
preferably overnight.
2. After soaking and cleaning, the bearings,
bearing frame, and bearing cap and/or
cartridge should be rinsed in a clean, light
mineral solvent and agitated vigorously to
remove all loosened hard grease and dirt.
3. Dip bearings in clean, light oil and spin by
hand to determine that all foreign matter has
been removed.
4. After cleaning, repack bearings half full on
both sides with a good quality ball bearing
grease.
Bearing Relubrication
To relubricate bearings use the following procedure:
CAUTION
Overgreasing creates heat and is the cause
of many problems requiring repair. DO NOT
OVERGREASE.
1. Never relubricate pump bearings while unit is
running. If necessary, shut down pump
according to section V, paragraph C,
Stopping the Pump.
2. Remove plugs opposite grease fittings on
both ends of bearing frame.
CAUTION
Do not lubricate bearings with a power
grease gun.
3. Using a hand-operated grease gun on
grease fittings, add approximately one ounce
of fresh grease for each bearing. With most
hand-operated grease guns, two or three
pumps are enough. DO NOT
OVERGREASE. When installing new
bearings, pack new bearings only half full
with grease.
Содержание GVS Series
Страница 1: ...GVS I 480 Rev 01...
Страница 3: ...NOTES ON INSPECTION AND REPAIRS INSPECTION DATE REPAIR TIME REPAIRS COST REMARKS...
Страница 23: ...19 Figure 2 Shaft Coupling Detail...
Страница 24: ...20 Figure 3 Bearing Lube Options...
Страница 25: ...21 Figure 4 Optional Wear Ring...
Страница 26: ...22...
Страница 27: ...October 2003...