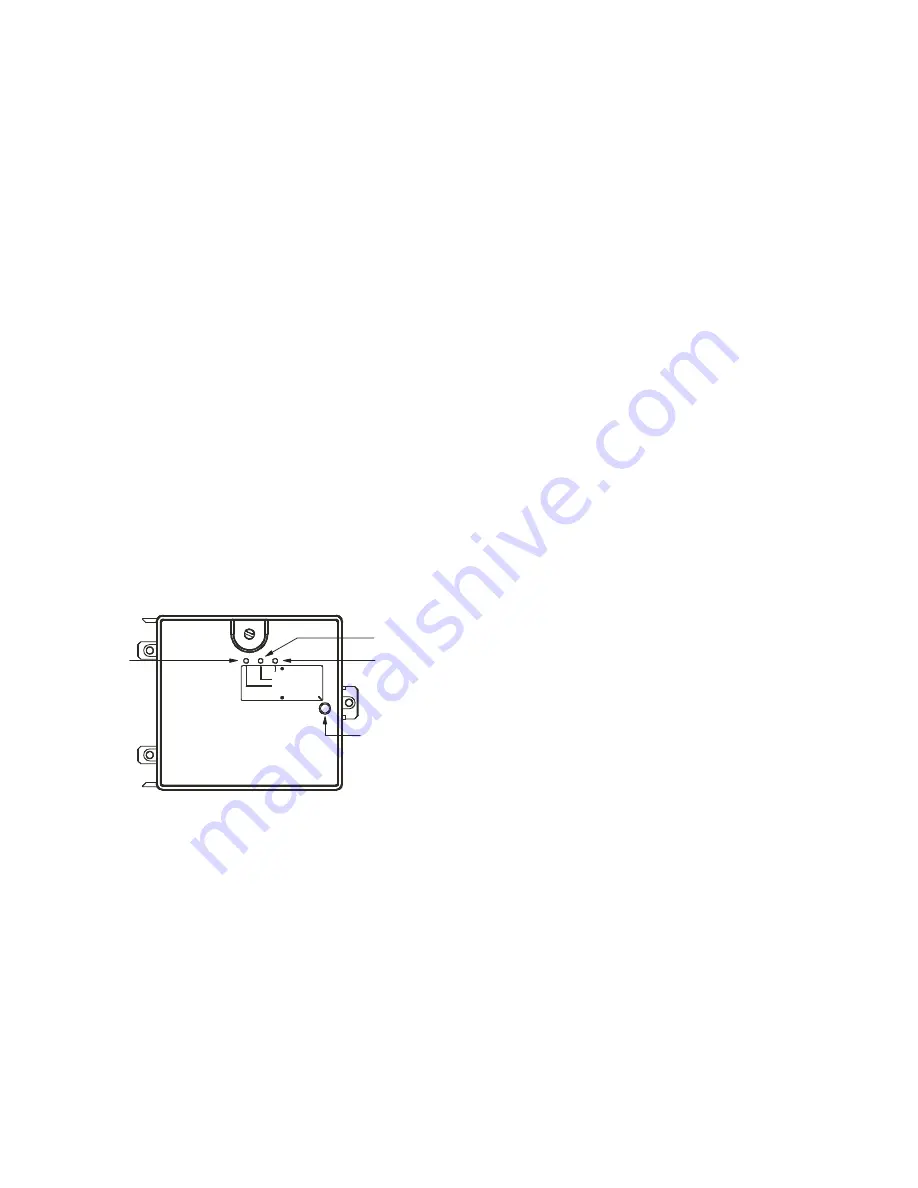
29
ALARM STATE
The smoke detector enters the alarm state when the amount of
smoke particulate in the sensor’s sensing chamber exceeds the
alarm threshold value. (See Table 8.) Upon entering the alarm
state:
• The sensor’s Alarm LED and the controller’s Alarm LED
turn on.
• The contacts on the controller’s two auxiliary relays switch
positions.
• The contacts on the controller’s alarm initiation relay
close.
• The controller’s remote alarm LED output is activated
(turned on).
• The controller’s high impedance multiple fan shutdown
control line is pulled to ground Trouble state.
The SuperDuct duct smoke detector enters the trouble state un-
der the following conditions:
• A sensor’s cover is removed and 20 minutes pass before it
is properly secured.
• A sensor’s environmental compensation limit is reached
(100% dirty).
• A wiring fault between a sensor and the controller is detected.
An internal sensor fault is detected upon entering the trouble
state:
• The contacts on the controller’s supervisory relay switch
positions. (See Fig. 59.)
• If a sensor trouble, the sensor’s Trouble LED the control-
ler’s Trouble LED turn on.
• If 100% dirty, the sensor’s Dirty LED turns on and the
controller’s Trouble LED flashes continuously.
• If a wiring fault between a sensor and the controller, the
controller’s Trouble LED turns on but not the sensor’s.
Fig. 59 — Controller Assembly
NOTE: All troubles are latched by the duct smoke detector. The
trouble condition must be cleared and then the duct smoke detec-
tor must be reset in order to restore it to the normal state.
RESETTING ALARM AND TROUBLE CONDITION TRIPS
Manual reset is required to restore smoke detector systems to
Normal operation. For installations using two sensors, the duct
smoke detector does not differentiate which sensor signals an
alarm or trouble condition. Check each sensor for Alarm or
Trouble status (indicated by LED). Clear the condition that has
generated the trip at this sensor. Then reset the sensor by press-
ing and holding the reset button (on the side) for 2 seconds.
Verify that the sensor’s Alarm and Trouble LEDs are now off.
At the controller, clear its Alarm or Trouble state by pressing
and holding the manual reset button (on the front cover) for
2 seconds. Verify that the controller’s Alarm and Trouble
LEDs are now off. Replace all panels.
Troubleshooting
CONTROLLER’S TROUBLE LED IS ON
1. Check the Trouble LED on each sensor connected to the
controller. If a sensor’s Trouble LED is on, determine the
cause and make the necessary repairs.
2. Check the wiring between the sensor and the controller. If
wiring is loose or missing, repair or replace as required.
CONTROLLER’S TROUBLE LED IS FLASHING
1. One or both of the sensors is 100% dirty.
2. Determine which Dirty LED is flashing then clean that sen-
sor assembly as described in the detector cleaning section.
SENSOR’S TROUBLE LED IS ON
1. Check the sensor’s Dirty LED. If it is flashing, the sensor
is dirty and must be cleaned.
2. Check the sensor’s cover. If it is loose or missing, secure
the cover to the sensor housing.
3. Replace sensor assembly.
SENSOR’S POWER LED IS OFF
1. Check the controller’s Power LED. If it is off, determine
why the controller does not have power and make the nec-
essary repairs.
2. Check the wiring between the sensor and the controller. If
wiring is loose or missing, repair or replace as required.
CONTROLLER’S POWER LED IS OFF
1. Make sure the circuit supplying power to the controller is
operational. If not, make sure JP2 and JP3 are set correctly
on the controller before applying power.
2. Verify that power is applied to the controller’s supply
input terminals. If power is not present, replace or repair
wiring as required.
REMOTE TEST/RESET STATION’S TROUBLE LED DOES
NOT FLASH WHEN PERFORMING A DIRTY TEST, BUT
THE CONTROLLER’S TROUBLE LED DOES
1. Verify that the remote test/station is wired as shown in
Fig. 57. Repair or replace loose or missing wiring.
2. Configure the sensor dirty test to activate the controller’s
supervision relay. See “Changing sensor dirty test operation.”
SENSOR’S TROUBLE LED IS ON, BUT THE CONTROL-
LER’S TROUBLE LED IS OFF
Remove JP1 on the controller.
PROTECTIVE DEVICES
Compressor Protection
OVERCURRENT
The compressor has internal line-break motor protection.
OVERTEMPERATURE
The compressor has an internal protector to protect it against
excessively high discharge gas temperatures.
HIGH PRESSURE SWITCH
The system is provided with a high pressure switch mounted
on the discharge line. The switch is stem-mounted and brazed
into the discharge tube. Trip setting is 630 psig ± 10 psig (4344
± 69 kPa) when hot. Reset is automatic at 505 psig (3482 kPa).
LOW PRESSURE SWITCH
The system is protected against a loss of charge and low evapo-
rator coil loading condition by a low pressure switch located on
ALARM
POWER
TEST/RESET
SWITCH
TROUBLE
RESET
ALARM
TROUBLE
POWER
Содержание WeatherMaster 50HC04
Страница 32: ...32 Fig 63 RTU Open Overlay for Economizer Wiring ...
Страница 33: ...33 Fig 64 VFD Overlay for W2770 Controller Wiring ...
Страница 85: ...85 Fig B 50HC A04 A06 PAC Control Diagram 208 1 60 208 230 3 60 460 575 3 60 APPENDIX D WIRING DIAGRAMS ...
Страница 86: ...86 Fig C 50HC A07 PAC Control Diagram 208 230 3 60 460 575 3 60 APPENDIX D WIRING DIAGRAMS ...
Страница 89: ...89 Fig F 50HC D08 D09 PAC Control Diagram 208 230 3 60 460 575 3 60 APPENDIX D WIRING DIAGRAMS ...
Страница 90: ...90 Fig G 50HC D11 PAC Control Diagram 208 230 3 60 460 3 60 575 3 60 APPENDIX D WIRING DIAGRAMS ...
Страница 91: ...91 Fig H 50HC D12 PAC Control Diagram 208 230 3 60 460 575 3 60 APPENDIX D WIRING DIAGRAMS ...
Страница 92: ...92 Fig I 50HC D14 PAC Control Diagram 208 230 3 60 460 3 60 575 3 60 APPENDIX D WIRING DIAGRAMS ...
Страница 93: ...93 Fig J 50HC A04 A06 PAC Power Diagram 208 230 1 60 APPENDIX D WIRING DIAGRAMS ...
Страница 94: ...94 Fig K 50HC A04 A06 PAC Power Diagram 208 230 3 60 460 3 60 575 3 60 APPENDIX D WIRING DIAGRAMS ...
Страница 95: ...95 Fig L 50HC A07 PAC Power Diagram 208 230 3 60 460 3 60 575 3 60 APPENDIX D WIRING DIAGRAMS ...
Страница 98: ...98 Fig O 50HC D07 PAC Power Diagram 575 3 60 6 Ton 2 Stage with Dehumidification APPENDIX D WIRING DIAGRAMS ...
Страница 99: ...99 Fig P 50HC D08 D09 PAC Power Diagram 208 230 3 60 460 3 60 575 3 60 APPENDIX D WIRING DIAGRAMS ...
Страница 100: ...100 Fig Q 50HC D11 PAC Power Diagram 208 230 3 60 APPENDIX D WIRING DIAGRAMS ...
Страница 101: ...101 Fig R 50HC D11 PAC Power Diagram 460 3 60 575 3 60 APPENDIX D WIRING DIAGRAMS ...
Страница 102: ...102 Fig S 50HC D12 PAC Power Diagram 208 230 3 60 460 3 60 575 3 60 APPENDIX D WIRING DIAGRAMS ...
Страница 103: ...103 Fig T 50HC D14 PAC Power Diagram 208 230 3 60 APPENDIX D WIRING DIAGRAMS ...
Страница 104: ...104 Fig U 50HC D14 PAC Power Diagram 460 3 60 575 3 60 APPENDIX D WIRING DIAGRAMS ...
Страница 109: ...109 Fig Z 50HC D12 PAC Control Diagram 230 460 575 3 60 with Humidi MiZer System APPENDIX D WIRING DIAGRAMS ...
Страница 110: ...110 Fig AA 50HC D14 PAC Control Diagram 230 460 575 3 60 with Humidi MiZer System APPENDIX D WIRING DIAGRAMS ...
Страница 111: ...111 Fig AB 50HC A04 A06 PAC Power Diagram 208 230 1 60 with Humidi MiZer System APPENDIX D WIRING DIAGRAMS ...
Страница 112: ...112 Fig AC 50HC A04 A06 PAC Power Diagram 208 230 460 3 60 with Humidi MiZer System APPENDIX D WIRING DIAGRAMS ...
Страница 113: ...113 Fig AD 50HC A04 A06 PAC Power Diagram 575 3 60 with Humidi MiZer System APPENDIX D WIRING DIAGRAMS ...
Страница 114: ...114 Fig AE 50HC A07 PAC Power Diagram 208 230 460 3 60 with Humidi MiZer System APPENDIX D WIRING DIAGRAMS ...
Страница 115: ...115 Fig AF 50HC A07 PAC Power Diagram 575 3 60 with Humidi MiZer System APPENDIX D WIRING DIAGRAMS ...
Страница 116: ...116 Fig AG 50HC D08 D09 PAC Power Diagram 208 230 460 3 60 with Humidi MiZer System APPENDIX D WIRING DIAGRAMS ...
Страница 117: ...117 Fig AH 50HC D08 D09 PAC Power Diagram 575 3 60 with Humidi MiZer System APPENDIX D WIRING DIAGRAMS ...
Страница 118: ...118 Fig AI 50HC D11 PAC Power Diagram 208 230 3 60 with Humidi MiZer System APPENDIX D WIRING DIAGRAMS ...
Страница 119: ...119 Fig AJ 50HC D11 PAC Power Diagram 460 3 60 575 3 60 with Humidi MiZer System APPENDIX D WIRING DIAGRAMS ...
Страница 121: ...121 Fig AL 50HC D14 PAC Power Diagram 208 230 3 60 with Humidi MiZer System APPENDIX D WIRING DIAGRAMS ...
Страница 122: ...122 Fig AM 50HC D14 PAC Power Diagram 460 3 60 with Humidi MiZer System APPENDIX D WIRING DIAGRAMS ...
Страница 123: ...123 Fig AN 50HC D14 PAC Power Diagram 575 3 60 with Humidi MiZer System APPENDIX D WIRING DIAGRAMS ...
Страница 124: ...124 Fig AO PremierLink System A04 A06 Wiring Diagram APPENDIX D WIRING DIAGRAMS ...
Страница 125: ...125 Fig AP RTU Open System Control A04 A06 Wiring Diagram APPENDIX D WIRING DIAGRAMS ...
Страница 126: ...126 Fig AQ PremierLink System A07 D14 Wiring Diagram APPENDIX D WIRING DIAGRAMS ...
Страница 127: ...127 Fig AR RTU Open A07 D14 Wiring Diagram APPENDIX D WIRING DIAGRAMS ...