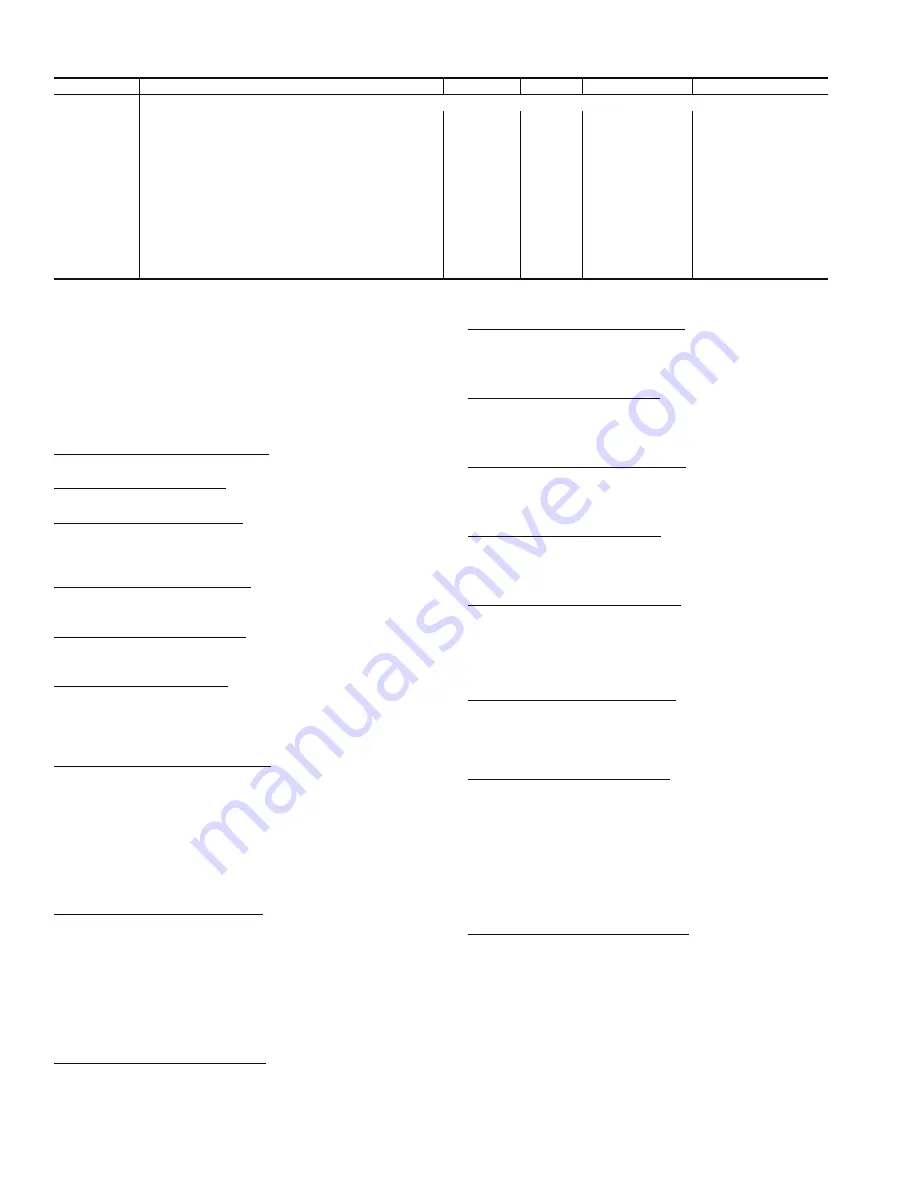
92
Table 78 — Auto View of Run Status Display Table
ECONOMIZER RUN STATUS — The Economizer Run Status
display table provides information about the economizer and can
be used to troubleshoot economizer problems. See Table 79. The
current position, commanded position, and whether the econo-
mizer is active can be displayed. All the disabling conditions
for the economizer and outside air information is also displayed.
COOLING INFORMATION — The Cooling Information run
status display table provides information on the cooling opera-
tion of the unit. See Table 80.
Current Running Capacity (
C.CAP
) — This variable repre-
sents the amount of capacity currently running as a percent.
Current Cool Stage (
CUR.S
) — This variable represents the
cool stage currently running.
Requested Cool Stage (
REQ.S
) — This variable represents
the requested cool stage. Cooling relay timeguards in place
may prevent the requested cool stage from matching the
current cool stage.
Maximum Cool Stages (
MAX.S
) — This variable is the max-
imum number of cooling stages the control is configured for
and capable of controlling.
Active Demand Limit (
DEM.L
) — If demand limit is active,
this variable will represent the amount of capacity that the
control is currently limited to.
Capacity Load Factor (
SMZ
) — This factor builds up or
down over time (–100 to +100) and is used as the means of add-
ing or subtracting a cooling stage during run time. It is a nor-
malized representation of the relationship between “Sum” and
“Z”. See the SUMZ Cooling Algorithm section on page 50.
Next Stage EDT Decrease (
ADD.R
) — This variable repre-
sents (if adding a stage of cooling) how much the temperature
should drop in degrees depending on the
R.PCT
calculation
and how much additional capacity is to be added.
ADD.R
=
R.PCT
*
(
C.CAP
– capacity after adding a cool-
ing stage)
For example: If
R.PCT
= 0.2 and the control would be add-
ing 20% cooling capacity by taking the next step up, 0.2 times
20 = 4 F
ADD.R
Next Stage EDT Increase (
SUB.R
) — This variable repre-
sents (if subtracting a stage of cooling) how much the tempera-
ture should rise in degrees depending on the
R.PCT
calculation
and how much capacity is to be subtracted.
SUB.R
=
R.PCT
* (
C.CAP
– capacity after subtracting a
cooling stage)
For Example: If
R.PCT
= 0.2 and the control would be
subtracting 30% capacity by taking the next step down,
0.2 times –30 = –6 F
SUB.R
.
Rise Per Percent Capacity (
R.PCT
) — This is a real time cal-
culation that represents the amount of degrees of drop/rise
across the evaporator coil versus percent of current running
capacity.
R.PCT
= (
MAT
–
EDT
)/
C.CAP
Cap Deadband Subtracting (
Y.MIN
) — This is a control vari-
able used for Low Temp Override (
L.TMP
) and Slow Change
Override (
SLOW
).
Y.MIN
= –
SUB.R
*0.4375
Cap Deadband Adding (
Y.PLU
) — This is a control variable
used for High Temp Override (
H.TMP
) and Slow Change
Override (
SLOW
).
Y.PLU
= –
ADD.R
*0.4375
Cap Threshold Subtracting (
Z.MIN
) — This parameter is
used in the calculation of
SMZ
and is calculated as follows:
Z.MIN
=
Configuration
→
COOL
→
Z.GN
* (–10 + (4*
(
–
SUB.R
))) * 0.6
Cap Threshold Adding (
Z.PLU
) — This parameter is used in
the calculation of SMZ and is calculated as follows:
Z.PLU
=
Configuration
→
COOL
→
Z.GN
* (10 + (4*
(
–
ADD.R
))) * 0.6
High Temp Cap Override (
H.TMP
) — If stages of mechani-
cal cooling are on and the error is greater than twice
Y.PLU
,
and the rate of change of error is greater than 0.5
°
F, then a
stage of mechanical cooling will be added every 30 seconds.
This override is intended to react to situations where the load
rapidly increases.
Low Temp Cap Override (
L.TMP
) — If the error is less than
twice
Y.MIN
, and the rate of change of error is less than
–0.5
°
F, then a mechanical stage will be removed every 30 sec-
onds. This override is intended to quickly react to situations
where the load is rapidly reduced.
Pull Down Cap Override (
PULL
) — If the error from set
point is above 4
°
F, and the rate of change is less than –1
°
F per
minute, then pulldown is in effect, and “SUM” is set to 0. This
keeps mechanical cooling stages from being added when the
error is very large, but there is no load in the space. Pulldown
for units is expected to rarely occur, but is included for the rare
situation when it is needed. Most likely pulldown will occur
when mechanical cooling first becomes available shortly after
the control goes into an occupied mode (after a warm unoccu-
pied mode).
Slow Change Cap Override (
SLOW
) — With a rooftop unit,
the design rise at 100% total unit capacity is generally around
30
°
F. For a unit with 4 stages, each stage represents about
7.5
°
F of change to EDT. If stages could reliably be cycled at
very fast rates, the set point could be maintained very precisely.
Since it is not desirable to cycle compressors more than 6 cy-
cles per hour, slow change override takes care of keeping the
PID under control when “relatively” close to set point.
MODE TRIP HELPER — The Mode Trip Helper table pro-
vides information on the unit modes and when the modes start
and stop. See Table 81. This information can be used to help
determine why the unit is in the current mode.
ITEM
EXPANSION
RANGE
UNITS
POINT
WRITE STATUS
VIEW
AUTO VIEW OF RUN STATUS
→
HVAC
ascii string spelling out the hvac modes
string
→
OCC
Occupied ?
YES/NO
OCCUPIED
forcible
→
MAT
Mixed Air Temperature
dF
MAT
→
EDT
Evaporator Discharge Tmp
dF
EDT
→
LAT
Leaving Air Temperature
dF
LAT
→
EC.C.P
Economizer Control Point
dF
ECONCPNT
→
ECN.P
Economizer Act.Curr.Pos.
0-100
%
ECONOPOS
→
EC2.P
Economzr2 Act.Curr.Pos.
0-100
%
ECON2POS
→
CL.C.P
Cooling Control Point
dF
COOLCPNT
→
C.CAP
Current Running Capacity
CAPTOTAL
→
CL.ST
Requested Cool Stage
CL_STAGE
→
HT.C.P
Heating Control Point
dF
HEATCPNT
→
HT.ST
Requested Heat Stage
HT_STAGE
→
H.MAX
Maximum Heat Stages
HTMAXSTG
Содержание WEATHERMASTER 48Z030
Страница 103: ...103 Fig 15 Typical Power Schematic Sizes 030 050 Shown a48 8408 ...
Страница 104: ...104 Fig 16 Main Base Board Input Output Connections a48 8409 ...
Страница 105: ...105 Fig 17 RCB ECB CEM SCB Input Output Connections a48 8410 ...
Страница 106: ...106 Fig 18 Typical Gas Heat Unit Control Wiring 48Z055 105 Units Shown a48 8411 ...
Страница 107: ...107 Fig 19 Typical Electric Heat Unit Control Wiring 50Z055 105 Units Shown a50 8248 ...
Страница 108: ...108 Fig 20 Typical Power Wiring 115 V 48Z Units a48 8412 ...
Страница 109: ...109 Fig 21 Typical Power Wiring 115 V 50Z Units a50 8249 ...
Страница 110: ...110 Fig 22 Typical Gas Heat Section Size 055 105 Units Shown a48 8413 ...
Страница 111: ...111 Fig 23 Component Arrangement Size 030 050 Units ...
Страница 112: ...112 Fig 24 Component Arrangement Size 055 070 Units ...
Страница 113: ...113 Fig 25 Component Arrangement Size 075 105 Units ...