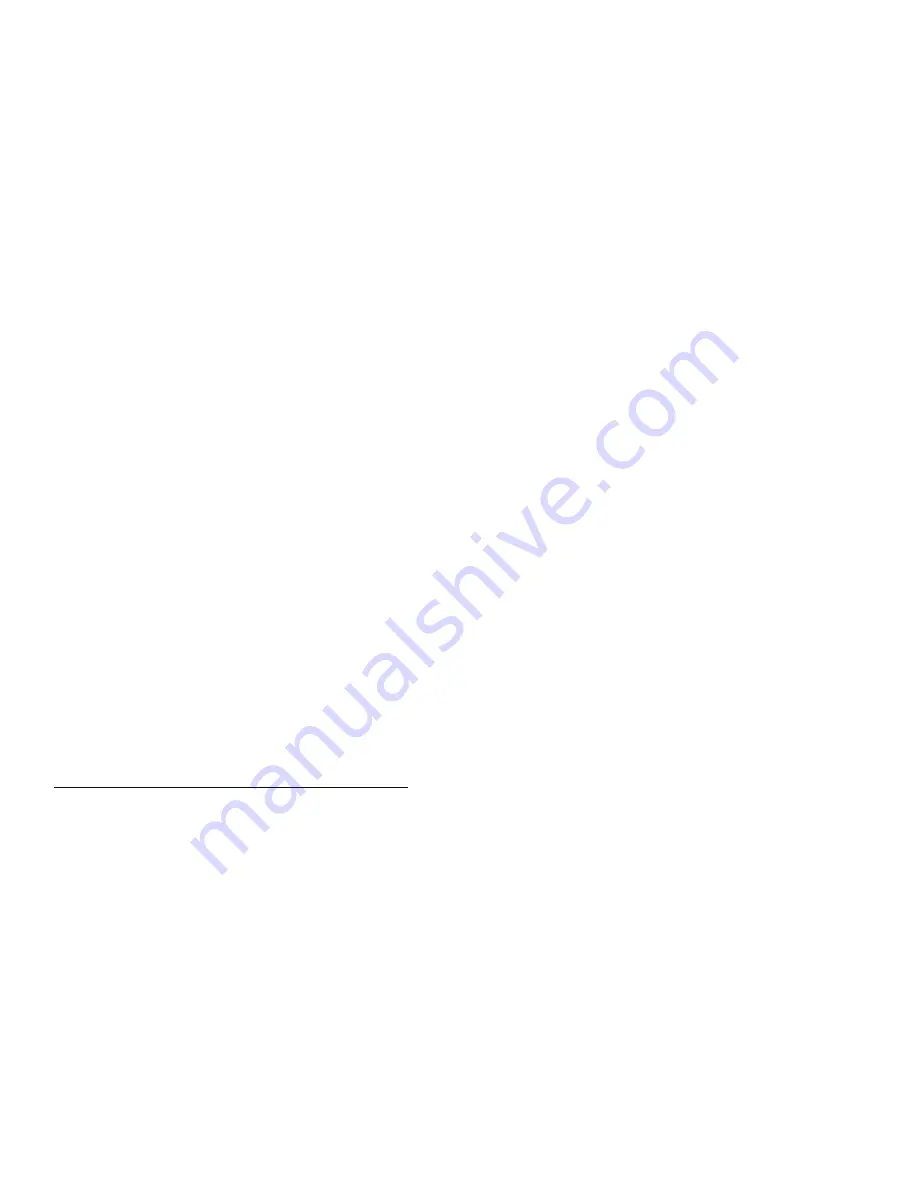
72
Controlling high-capacity power exhaust differs from nor-
mal power exhaust in the following ways:
• The integral term is not used. The percentile commanded
position of the VFD is used instead.
• A “clamp percent” configuration is added (
BP.CL
) to
create a deadband that will assist the algorithm in
controlling the second power exhaust relay.
If building pressure (BP) rises above the building pressure
set point (
BP.SP
) and the supply fan is on, building pressure
control is initiated. Thereafter if the supply fan relay goes off or
if the building pressure drops below the
BP.SP
minus the
building pressure set point offset (
BP.SO
) for 5 continuous
minutes, building pressure control will be stopped. The
5-minute timer will continue to reset while the VFD is com-
manded to a position > 0%. If the building pressure falls below
the set point, the VFD will shut down automatically. Any time
building pressure control becomes active, the exhaust fan relay
turns on which energizes the exhaust fan VFD.
After the exhaust fan relay turns on, PID control ensues with-
out an “I” term:
Error = BP –
BP.SP
K = 1000 *
BP.TM
/ 60 (normalize the PID control for run rate)
P = K *
BP.P
* (error)
D = K *
BP.D
* (error - error computed last time through the
PID)
VFD control signal (clamped between 0 and 100%) = VFD
Output last time t (P + D)
NOTE: The sum of P + D will be clamped on any timed calcu-
lation to an internally calculated value which guarantees the
VFD is not commanded more or less an amount, than it cannot
achieve before the next time VFD capacity is again calculated.
Bringing the single speed fan (
P.E.2
) ON and OFF is coordi-
nated with the VFD speed. When building pressure first
becomes active,
P.E.2
is OFF,
P.E.1
is ON and the VFD is
allowed to climb to 100%.
BP.CL
will be used to act as hyster-
esis so that when the P + D term is evaluated and it exceeds
BP.CL
, the control will go through a one-minute period hold
off time where the VFD is commanded to
BP.CL
, and
P.E.2
is
brought on. After the transition to
P.E.2
ON is complete, the
control will continue to control the VFD from
BP.CL
%. If BP
rises, the control will speed up the VFD. Should the VFD drop
to 0%, and the next time through the PID the P + D term calcu-
lation is less than –
BP.CL
, the control will go through another
one-minute PID hold off period where
P.E.2
is commanded
OFF and the VFD is commanded to 100 –
BP.CL
.
Configuration
→
BP
→
BP.CF
=5
(Return/Exhaust Control)
— Fan tracking is the method of control used on plenum return
fan option. The fan tracking algorithm controls the exhaust/
return fan VFD and the exhaust fan relay. The
Comfort
Link™
controls use a flow station to measure the flow of both the sup-
ply and the return fans. The speed of the return fan is controlled
by maintaining a delta cfm (usually with supply airflow being
greater of the two) between the two fans. The building pressure
is controlled by maintaining this delta cfm between the two
fans. In general, the greater the delta between supply airflow
and return airflow, the higher the building pressure will be.
Conversely, as the return airflow quantity increases above
the supply airflow, the lower the building pressure will be.
Whenever there is a request for the supply fan (or there is the
presence of the IGC feedback on gas heat units), the return fan
is started. The delta cfm is defined as
S.CFM
–
R.CFM
. The
return fan VFD is controlled by a PID on the error of delta cfm
actual from delta cfm set point. If the error is positive the drive
will increase speed. If the error is negative the drive will
decrease speed.
NOTE: These configurations are used only if Fan Tracking
Learning is enabled. When Fan Tracking Learning is enabled,
the control will adjust the delta cfm (
FT.ST
) between the
supply and return fan if the building pressure deviates from the
Building Pressure Set Point (
BP.SP
). Periodically, at the rate
set by the fan track learn rate (
FT.TM
), the delta cfm is
adjusted upward or downward with a maximum adjustment
at a given instance to be no greater than fan track max
correction (
FT.AD
). The delta cfm can not ever be adjusted
greater than or less than the fan track initial delta cfm (
FT.ST
)
than by the Fan Track Max Clamp (
FT.MX
).
CONFIGURING THE BUILDING PRESSURE ACTUA-
TORS (
BP.CF
= 2) TO COMMUNICATE VIA ACTUATOR
SERIAL NUMBER — Every actuator used in the Z Series
control system has its own unique serial number. The rooftop
control uses this serial number to communicate with the
actuator over the local equipment network (LEN). These serial
numbers are programmed at the factory and should not need
changing. Should field replacement of an actuator become
necessary, it will be necessary to configure the serial numbers
of the new actuator. Five individual numbers make up each se-
rial number and these can be programmed to match the serial
number of the actuators in the building pressure actuator
configurations group,
ACT.C.
→
BP.1
and
BP.2
(
SN.1, SN.2,
SN.3, SN.4, SN.5
).
NOTE: The serial numbers for all LEN actuators can be found
inside the control doors of the unit as well as on the actuator
itself. If an actuator is replaced in the field, it is a good idea to
remove the additional peel-off serial number sticker on the
actuator and cover up the old one inside the control doors.
CONTROL ANGLE ALARM CONFIGURATION
C.ALM
(
BP.CF
= 2) — The building pressure actuators learn what its
end stops are though a calibration at the factory. Field-installed
actuators may be calibrated in the Service Test mode. When an
actuator learns its end stops through calibration, it stores the
control angle. The actuator will resolve this control angle and
express its operation in a percent (%) of this learned range.
If a building pressure actuator has not learned a sufficient
control angle during calibration, the actuator will be unable to
control building pressure. For this reason the building pressure
actuators used in the Z Series control system have configurable
control angle alarm low limits in the Building Pressure Actua-
tor Configurations group,
ACT.C
→
BP.1
and
BP.2.
(
C.A.LM
).
If the control angle learned through calibration is less than
C.A.LM
, an alert will occur and the actuator will not function.
NOTE: This configuration does not typically need adjustment.
It is configurable for the small number of jobs which may
require a custom solution or workaround.
Smoke Control Modes —
There are four smoke con-
trol modes that can be used to control smoke within areas ser-
viced by the unit: Pressurization mode, Evacuation mode,
Smoke Purge mode, and Fire Shutdown. Evacuation, Pressur-
ization and Smoke Purge modes require the controls expansion
board (CEM). The Fire Shutdown input is located on the main
board (MBB) on terminals TB201-5 and 6. The unit may also
be equipped with a factory-installed return air smoke detector
that is wired to TB201-5,6 and will shut the unit down if a
smoke condition is determined. Field-monitoring wiring can be
connected to terminal TB201-13 and 14 to monitor the smoke
detector. Inputs on the CEM board can be used to put the unit
in the Pressurization, Evacuation, and Smoke Purge modes.
These switches or inputs are connected to TB204 as shown be-
low. Refer to Major System Components section on page 102
for wiring diagrams.
Pressurization — TB204-5 and 6
Evacuation — TB204-7 and 8
Smoke Purge — TB204-9 and 10
Each mode must be energized individually on discrete in-
puts and the corresponding alarm is initiated when a mode is
activated. The fire system provides a normally closed dry
Содержание WEATHERMASTER 48Z030
Страница 103: ...103 Fig 15 Typical Power Schematic Sizes 030 050 Shown a48 8408 ...
Страница 104: ...104 Fig 16 Main Base Board Input Output Connections a48 8409 ...
Страница 105: ...105 Fig 17 RCB ECB CEM SCB Input Output Connections a48 8410 ...
Страница 106: ...106 Fig 18 Typical Gas Heat Unit Control Wiring 48Z055 105 Units Shown a48 8411 ...
Страница 107: ...107 Fig 19 Typical Electric Heat Unit Control Wiring 50Z055 105 Units Shown a50 8248 ...
Страница 108: ...108 Fig 20 Typical Power Wiring 115 V 48Z Units a48 8412 ...
Страница 109: ...109 Fig 21 Typical Power Wiring 115 V 50Z Units a50 8249 ...
Страница 110: ...110 Fig 22 Typical Gas Heat Section Size 055 105 Units Shown a48 8413 ...
Страница 111: ...111 Fig 23 Component Arrangement Size 030 050 Units ...
Страница 112: ...112 Fig 24 Component Arrangement Size 055 070 Units ...
Страница 113: ...113 Fig 25 Component Arrangement Size 075 105 Units ...