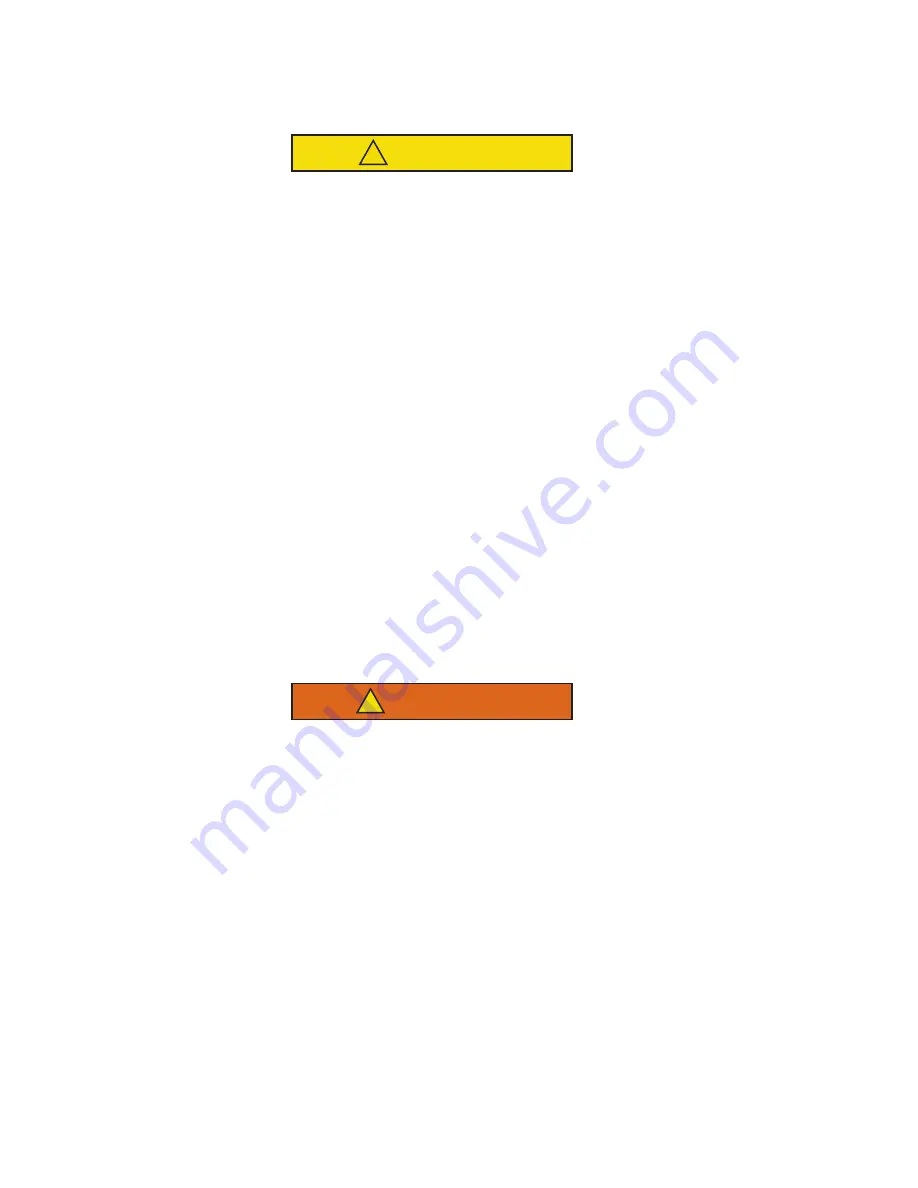
T-340
7–4
7.4 Pump Down the Unit
To service the filter drier, economizer, expansion valves, economizer solenoid valve, digital unloader valve or evap
-
orator coil, pump the refrigerant into the high side as follows:
CAUTION
!
The scroll compressor achieves low suction pressure very quickly. Do not use the compressor
to evacuate the system below 0 psig. Never operate the compressor with the suction or dis
-
charge service valves closed (frontseated). Internal damage will result from operating the com
-
pressor in a deep vacuum.
1. Attach manifold gauge set to the compressor suction and discharge service valves (see
).
2. Start the unit and run in the frozen mode (controller set below -10°C (14°F) for 10 to 15 minutes.
3. Check function code Cd21 (see
). The economizer solenoid valve should be open. If not, con
-
tinue to run until the valve opens.
4. Frontseat the liquid line service valve. Place Start-Stop switch in the OFF position when the suction reaches
a positive pressure of 0.1 bar (1.4 psig).
5. Frontseat the suction and discharge service valves. The refrigerant will be trapped between the compressor
discharge service valves and the liquid line valve.
6. Before opening up any part of the system, a slight positive pressure should be indicated on the pressure
gauge. Remove power from the unit before opening any part of the system. If a vacuum is indicated, emit
refrigerant by cracking the liquid line valve momentarily to build up a slight positive pressure.
7. When opening up the refrigerant system, certain parts may frost. Allow the part to warm to ambient tempera
-
ture before dismantling. This avoids internal condensation which puts moisture in the system.
8. After repairs have been made, be sure to perform a refrigerant leak check (see
), and evacuate
and dehydrate the low side (see
).
9. Check refrigerant charge (see
).
7.5 Refrigerant Leak Checking
WARNING
!
EXPLOSION HAZARD Failure to follow this WARNING can result in death, serious personal
injury and / or property damage.
Never use air or gas mixtures containing oxygen (O
2
) for leak testing or operating the product.
Charge only with R-134a: Refrigerant must conform to AHRI Standard 700 specification.
1. The recommended procedure for finding leaks in a system is with a R-134a electronic leak detector. Testing
joints with soapsuds is satisfactory only for locating large leaks.
2. If the system is without refrigerant, charge the system with refrigerant 134a to build up pressure between2.1
to 3.5 bar (30.5 to 50.8 psig). To ensure complete pressurization of the system, refrigerant should be
charged at the compressor suction valve and the liquid line service valve. Remove refrigerant cylinder and
leak-check all connections.
NOTE
Only refrigerant 134a should be used to pressurize the system. Any other gas or vapor will contaminate the
system, which will require additional purging and evacuation of the system.
3. If required, remove refrigerant using a refrigerant recovery system and repair any leaks. Check for leaks.
4. Evacuate and dehydrate the unit (see
.)
).
Содержание Transicold 69NT40-561-001
Страница 2: ......
Страница 4: ......
Страница 14: ......
Страница 22: ......
Страница 36: ......
Страница 92: ......
Страница 159: ...7 47 T 340...
Страница 163: ...8 3 T 340 Figure 8 2 Schematic Diagram for Standard Unit Configuration Based on Drawing 62 11271 Rev A...
Страница 169: ...8 9 T 340 Figure 8 8 Schematic and Diagram for Lower Vent Position Sensor VPS Option...
Страница 170: ...T 340 8 10 Figure 8 9 Unit Wiring Diagram for Standard Unit Configuration With 3 Phase Condenser Fan Motors...
Страница 172: ...T 340 8 12 Figure 8 10 Unit Wiring Diagram for Single Phase Condenser Fan Motor and Optional Heater...
Страница 173: ...8 13 T 340 Unit Wiring Diagram for Single Phase Condenser Fan Motor and Optional Heater Based on Drawing 62 66721...
Страница 174: ...T 340 8 14 Figure 8 11 Unit Wiring Diagram for Configuration With eAutoFresh and Emergency Bypass Options...
Страница 176: ......
Страница 180: ......
Страница 181: ......