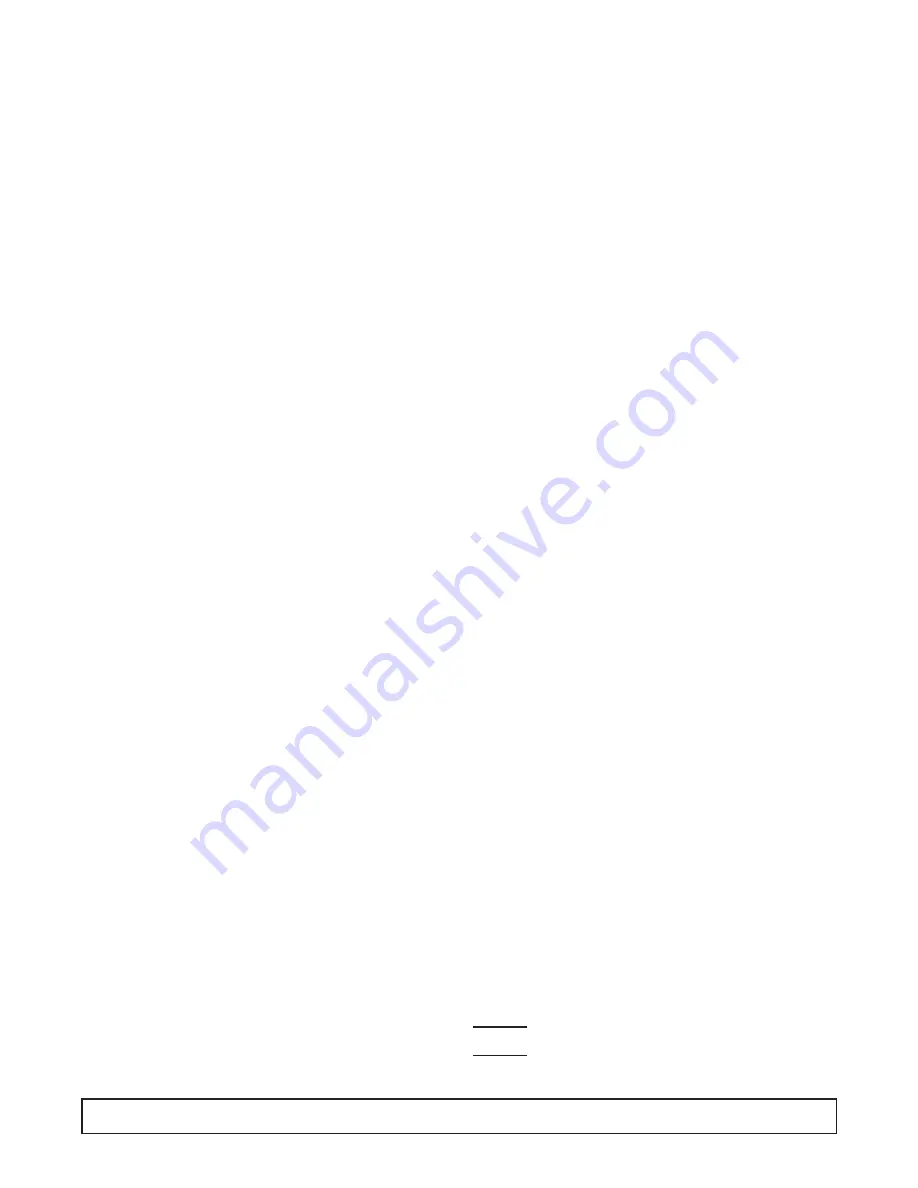
CMCT TROUBLESHOOTING GUIDE
The following is a guide to aid in the proper diagnosing
of service problems.
High Head Pressure & High Back Pressure
1. Air in system.
2. Defective fan motor or fan blade dragging on con-
denser shroud.
3. Defrost heater on during refrigeration cycle due to
heater going to ground or defective time clock.
4. Refrigerant over charge.
5. Blocked condenser (dirty)
Low Back Pressure & Low Head Pressure
1. Defective back pressure valve—check for proper
setting as described under “Back Pressure Valve.”
2. Shortage of refrigerant—place a temperature indicat-
ing device on outlet of top coil (lower lefthand side of
coil). Temperature should read within 3 to 4 degrees of
low side pressure taken at the compressor suction
service valve. Add gas slowly until these conditions
are obtained or remove charge with certified recovery
equipment, and recharge with correct charge.
3. Cap tube plugged due to moisture or dirt.
Pressures Normal – Cabinet Warm
1. Top coil blocked with frost—see corrective mea-
sures under “Coil Block With Frost.”
2. Refrigerant under charge. Due to the fact that it
takes a considerable amount of under charge before
it has any great effect on pressures and inaccuracy
of gauges it is possible to have normal pressures
and yet have an under charge of refrigerant. This
under charge will “starve” the top coil and seriously
affect cabinet temperature. To determine correct
charge see #2 under “Low Back Pressure … .”
Coil Blocked With Frost
1. Bad timer or timer motor.
2. Bad drafts in store caused by heating or air condi-
tioning fans; cabinet located too close to door.
3. Defective defrost heater.
4. Defective defrost terminating thermostat, safety
thermostat or defective solenoid in time clock.
4.
Either of these (#4) can keep the cabinet from going
through a defrost cycle. The defrost thermostat (see
wiring diagram) should be in open position between
terminals 1 & 2 when the cabinet goes into defrost.
4.
After the coil reaches 76°F, it closes, energizing a
solenoid in the time clock which in turn trips the time
clock mechanism off defrost. Should this thermostat
be in the closed position when the clock trips into
the defrost cycle, it will immediately trip it off again.
(NOTE: Switch between terminals 1 & 2 will not
open until thermostat drops below 59°F).
4.
If the solenoid in the clock is stuck closed (plunger
up), it will have the same effect. To determine which
is at fault, remove the wire from X on the clock and
turn clock dial into defrost cycle; if cabinet goes into
defrost, it is the defrost thermostat that is bad. If it
still does not go into defrost, remove clock and
inspect the plunger of the solenoid coil.
5. Defective safety thermostat.
5.
This thermostat has a SPDT switch with one side
wired in series with the defrost heater. Contacts
between terminals 2 & 3 should be in the closed
position during the refrigeration cycle. Its only pur-
pose is, in case of failure of the defrost timer during
the defrost cycle, it will open the heater circuit when
the coil reaches 76°F, preventing any over heating of
the defrost heater.
5.
If this thermostat is in the open position when the
cabinet goes into the defrost cycle, the heater will
remain off. For access to thermostat connections to
check continuity, refer to wiring diagram. Disconnect
this thermostat and check with ohmmeter.
5.
If for any reason the temperature termination feature
is inoperative, the fail safe settings on the timer
should be set for 30 minutes defrost time.
Defrost Cycle Too Long – Terminating On
Fail Safe (Heater On)
1. Bad solenoid in time clock (opening winding).
1.
If there is an open circuit in the coil of this solenoid,
it will not trip the time clock off defrost when the ther-
mostat closes. The cabinet will stay on defrost for
the length of time the fail-safe lever on the time clock
is set. (Factory set at 40 minutes.)
2. Defrost terminating thermostat not closing when coil
reaches 76°F.
To determine which is at fault, turn clock into defrost,
place jumper across X and N on clock. If solenoid is
good, this will trip the clock off defrost indicating that it
is the defrost thermostat that is at fault.
Be certain that the defrost thermostat has
reached 76°F before determining that either
the solenoid coil or the thermostat is defective.
NOTE:
38
MAINTENANCE & REPAIR
Содержание 52-2038-01
Страница 3: ...SECTION I Introduction...
Страница 13: ...12 INTRODUCTION WIRING DIAGRAM 00 1667 00 CMCT 4 6 8...
Страница 14: ...INTRODUCTION 13 WIRING DIAGRAM 00 1670 00 CMCT 10...
Страница 15: ...14 INTRODUCTION WIRING DIAGRAM 00 1934 00 ECMCT 4 6 8 Export Models...
Страница 16: ...INTRODUCTION 15 LAMP WIRING DETAIL Upper Raceway Typical...
Страница 17: ...SECTION II Maintenance Repair...
Страница 23: ...CONDENSING UNIT LAYOUT 24 MAINTENANCE REPAIR...
Страница 32: ...UPPER CROSS SECTION CMCT Models...
Страница 38: ...SECTION III Parts List...