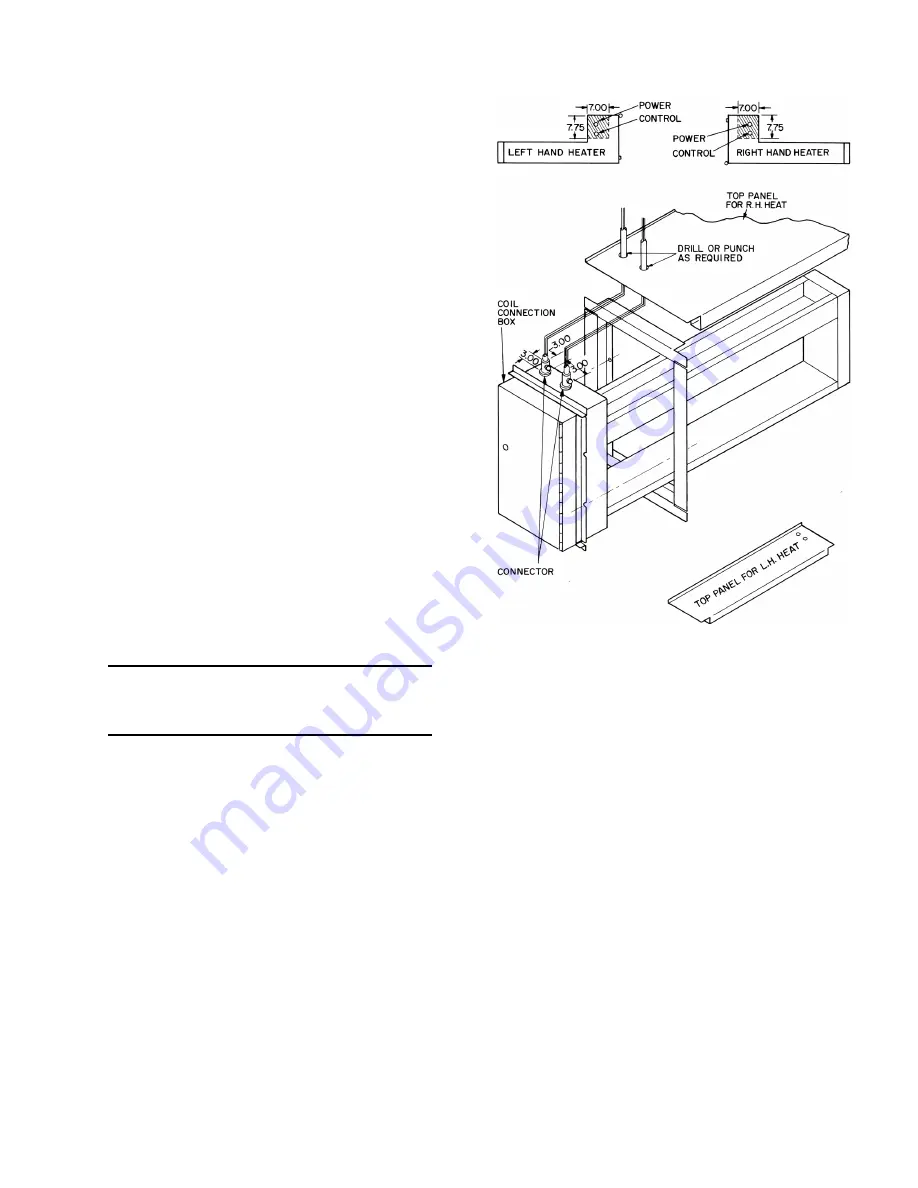
45
Electric Heaters
Electric heaters may be factory installed or drop shipped to the
jobsite and field installed. The heater can only be installed in the
preheat-electric section.
To install electric heater, refer to Fig. 47 and proceed as follows:
1. Locate preheat-electric section already mounted on unit and
remove protective shipping cover.
2. Locate crate containing electric heater and verify heater
matches the unit. Unit hand and heater hands must agree.
3. Remove both knockout slugs (power and signal). Install con-
duit connectors in top of coil connection box.
4. Remove top panel of the preheat-electric section and drill or
punch 2 holes are specified in Fig. 47.
5. Insert the electric heater into unit. It must slide between two
angles located on the bottom of the section.
6. Secure heater to the preheat-electric section using 4 screws.
7. Locate top panel of section. Run conduit through top panel
and tighten conduit connectors. Lower top panel and replace
panel on unit.
8. Complete wiring per wiring diagram and job requirements.
Follow all applicable local codes.
CONNECT POWER AND CONTROL WIRES
Heater wiring schematic is located on control box panel.
(Figure 48 shows typical wiring details.) Electrical data for each
standard heater arrangement is shown in Table 12. Verify that min-
imum airflow requirement (minimum coil face velocity, fpm) will
be met, especially on applications where variable air volume is
supplied.
Use copper power supply wires rated for 75°C minimum. On
250-v or greater applications, use 600-v rated wiring. Size wires
to carry 125% of current load on each set of terminals
(Table 12). Use the following formulas as required:
Single-phase line current
Three-phase line current
(kW per set of terminals) (1000) = (voltage) (1.73)
Note that if the heater is rated at 50 kW (or more) and is con-
trolled by a cycling device such as a multi-stage thermostat, or
a step controller, conductors may be sized at 100% of load am-
peres (as in Tables 12 and 13) per National Electrical Code
(NEC) Section 424-22. Heater construction and application in-
formation (Tables 16 and 17) are based upon Underwriters’
Laboratories (UL) Space Heating Standard No. 1096 and the
requirements of the NEC. Installer is responsible for observing
local code requirements.
Install a disconnect switch or main circuit breaker in accordance
with NEC and other applicable codes. Locate so that it is easily ac-
cessible and within sight of heater control box (per NEC Article
424-19 and 424-65).
Weatherproof junction boxes have no knockouts for wire entrance.
Drill or punch holes for conduit as required and make all junctions
watertight.
Where field-supplied thermostats are used, isolate circuits to pre-
vent possible interconnection of control circuit wiring.
Where field-supplied step controller is used, connect steps to ter-
minals as marked on wiring schematic. When connecting
multistage heaters, wire stage no. 1 so that it is first stage on, last
stage off. Connect thermostats as required.
Fig. 47 — Electric Heater Installation
Provide sufficient clearance for convection cooling of heaters with
solid-state controllers. Provide at least 5-in. of free air space above
and below cooling fins extending from heater terminal box. Be
sure to connect interlock terminals F1 and F2 to auxiliary contacts
on fan starter.
Each heater has 2 different types of factory-installed thermal cut-
outs for over-temperature protection; an automatic reset thermal
cutout for primary protection and a manual reset thermal cutout to
protect against failure of the primary system. Also provided is an
airflow pressure differential switch to prevent the heater from op-
erating when the fan is not in operation or airflow is restricted or
insufficient. The primary automatic reset cutout is a bi-metal disk-
type cutout. It is wired into the control circuit which operates the
magnetic disconnecting contactors (the same contactors which
also switch on and off the various steps of the coil). The secondary
manual reset cutout is a bi-metal disk-type cut-out. This secondary
thermal cutout is load carrying and is installed in each heater sub-
circuit. The primary and secondary over-temperature protection
systems are independent of each other. The secondary system is
designed to protect against possible failure of the primary system
to deenergize the heater.
Subcircuits in the heaters are designed in compliance with para-
graph 424-22 of the NEC. The coil is subdivided into circuits that
draw no more than 48 amps each and is fused for at least 125% of
the circuit rating.
Pilot tube is to be positioned so that the airflow switch is actuated
by a minimum negative pressure of 0.07 in. wg.
=
1 (kW per set of terminals) (1000)
voltage
=
(kW per set of terminals) (1000)
(voltage) (1.73)