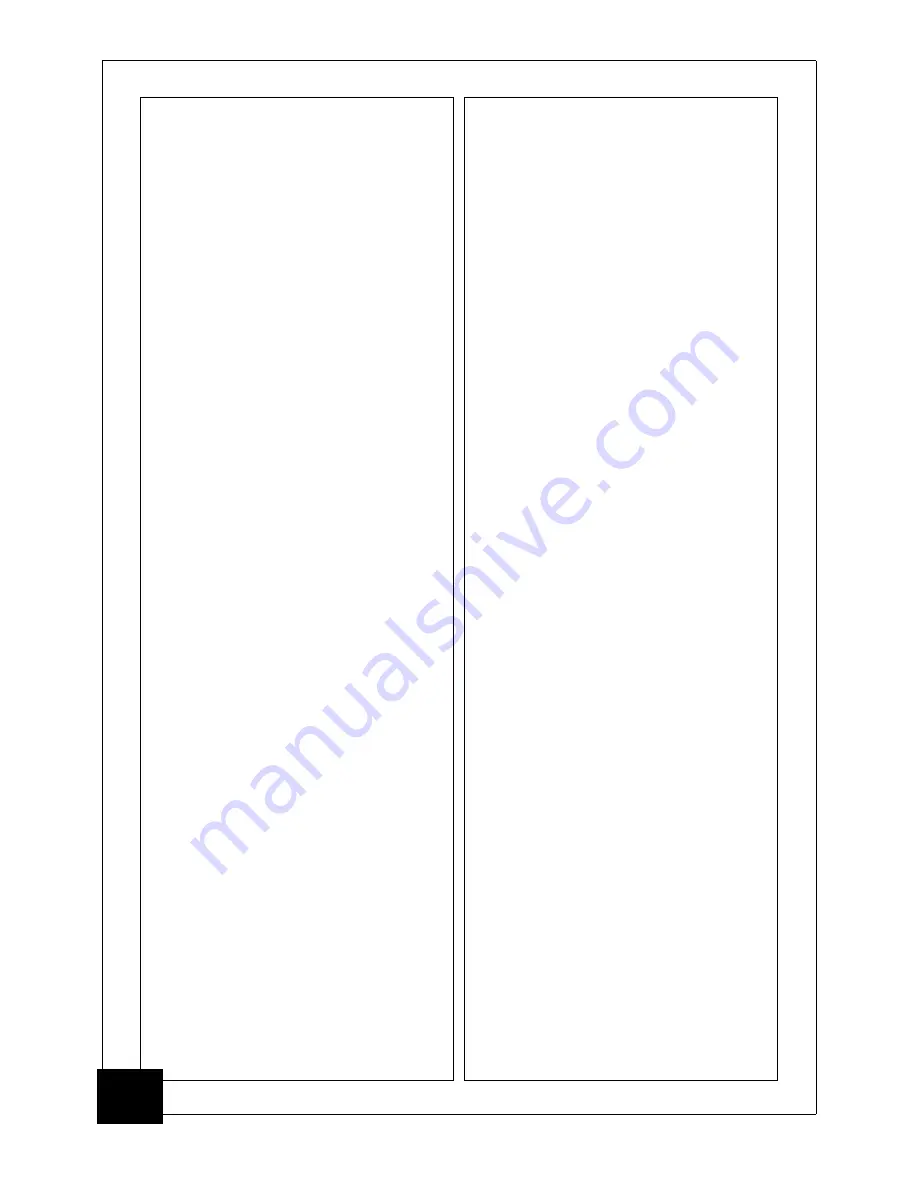
usually fall between 2 and 13% of rated
or "Base" speed. Slowly increase the IR
COMP adjustment clockwise until the
loaded speed equals the unloaded speed
measured in the previous step. Making
this adjustment may now cause the
unloaded speed to be slightly higher.
Repeat this procedure until there is no
difference between loaded and
unloaded speed levels.
Use care not to set the adjustment
too high or speed increase with load and
instability may result.
NOTE : For this adjustment, do not use
SCALED ARMATURE VOLTAGE to
measure speed. Armature voltage is not
an exact indication of loaded motor
speed!
INTEGRAL NULL
Adjustment of the INTEGRAL
NULL pot is sometimes required when
the control is continually operated in
the RUN mode with a zero speed
reference. With maintained zero
reference, creeping can occur. If this
condition exists, increase the
INTEGRAL NULL in the clockwise
direction to minimize the symptoms.
CURRENT PROPORTIONAL AND
CURRENT INTEGRAL
VELOCITY PROPORTIONAL
AND VELOCITY INTEGRAL
The PROPORTIONAL and
INTEGRAL adjustments P11, P12,
P16, and P17 as preset by CAROTRON
will provide stable and responsive
performance under most load
conditions. Therefore, any observed
instability should first be evaluated as a
possible load induced condition.
Cyclic variation in armature current and
in motor speed can indicate mechanical
coupling or machine loading conditions.
If mechanically induced, the instability
repetition rate or frequency can usually
be related to a motor or machine
rotation rate or loading cycle. In this
situation, the instability frequency will
change in coincidence with any motor
speed change.
Instability in the control output due
to incorrect adjustment would usually
be present over a range of speed and
would not usually change frequency in
coincidence with speed. Because the
response of the control can sometimes
be altered to partially compensate for
mechanically induced instability, it is
sometimes difficult to
determine if the
load change is affecting control output
stability or if control output is affecting
the load stability. De-coupling the load
from the motor can help make this
determination.
If fuse blowing or tripping of
breakers should occur, it may be due to
unbalanced operation of the power
bridge. This would usually be
noticeable when rapid changes in output
or surges of torque are being called for
as opposed to steady state operation.
An example would be when quickly
accelerating a load up to speed.
Excessive proportional gain settings
and/or too fast integral settings might
cause such unbalanced operation.
Typically the settings that provide
the most stable and balanced bridge
operation under all conditions do not
give the fastest response. In general,
low proportional gains (too far ccw
rotation) and too slow integral time
constants (too far cw) would cause
instability. Bridge unbalance would
usually result from just the opposite set-
17
Содержание P22194-1
Страница 1: ...P22194 1 DC DRIVE Instruction Manual ...
Страница 22: ...Drawings 9 21 ...
Страница 23: ...22 ...
Страница 24: ...23 ...
Страница 25: ...24 ...
Страница 26: ...25 ...