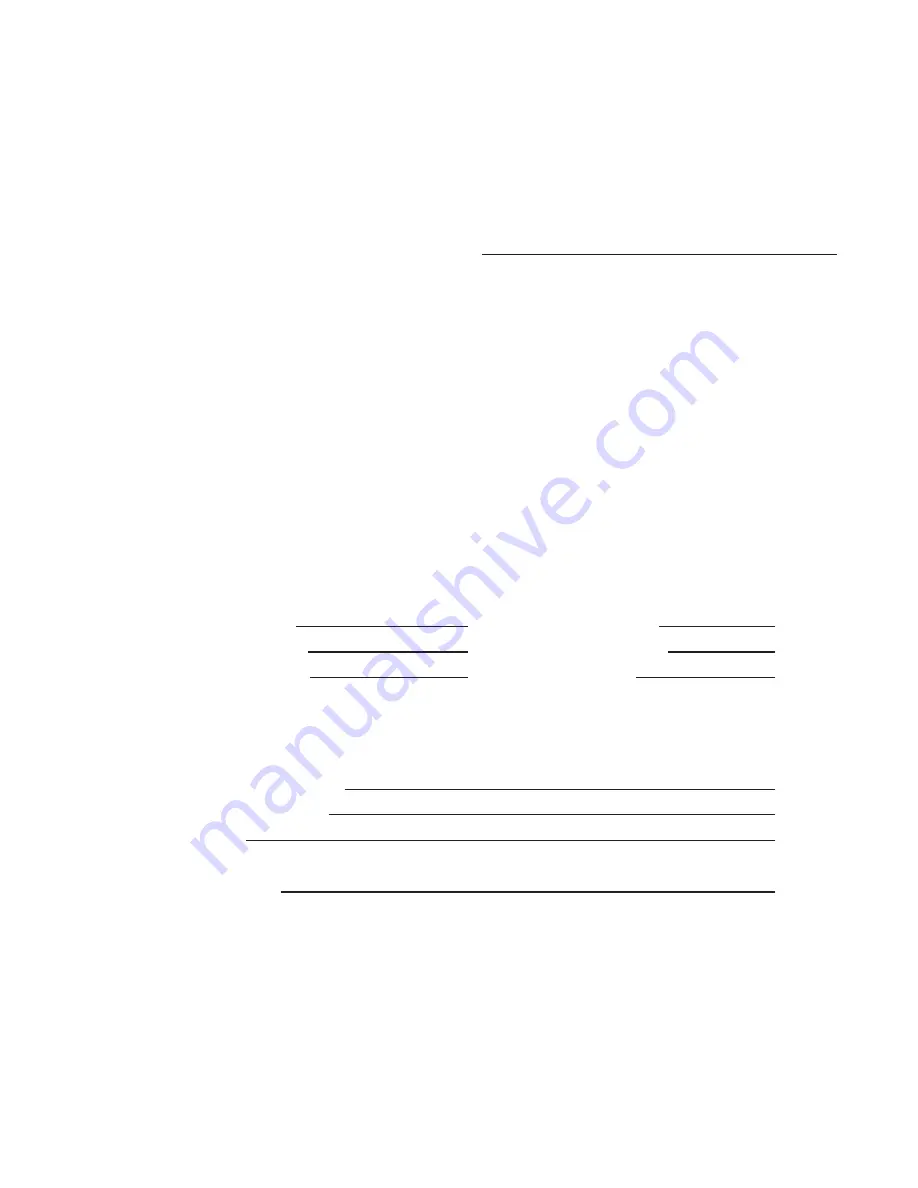
9.4 Start-Up Worksheet
1. While monitoring the discharge gage (located on the high pressure connection port on the
compressor body, not the discharge service valve), bump the compressor (turn the power on
for 1/2 to 1 second). If the discharge pressure increases, the direction of rotation of the com-
pressor is correct. If the discharge pressure drops, the compressor is experiencing reverse
rotation and the phase sequence must be reversed. The phase sequence may be changed by
switching any two leads at the compressor motor. (If a variable speed drive is used, see
Step 2.)
Discharge pressure reading when bumped:
2.
Warning:
If a variable speed drive is used, the rotation of the compressor must be checked
(as noted in Step 1) both with the inverter and through inverter bypass. When bumping the
compressor with the inverter, watch the service gage carefully as it may take 1–5 seconds
for significant rotation to occur. The phase sequence entering the variable speed drive may
not be the same as the phase sequence leaving the variable speed drive. If the compressor
rotation is incorrect both through the inverter and in bypass mode, any two leads must be
switched at the compressor. If only the inverter or bypass mode is experiencing incorrect
rotation, any two leads leaving the device causing reverse rotation must be switched.
After
any wiring change the compressor rotation must be checked both with the inverter and in
bypass mode.
3. If a variable speed drive is used and the compressor will not start within 10 seconds, shut down the
compressor and check the inverter size and logic.
4. After rotation has been verified prior to running the compressor, ensure gages have been
connected to the oil feed manifold (between oil line solenoid and compressor). Upon start-up,
immediately check oil pressure (difference between oil feed pressure and suction) to ensure that
it is greater than 45 psid (3 bar). If oil pressure is less than 45 psid (3 bar), shut compressor off
and check all oil line valves, filters, oil level and head pressure. Check the oil pressure drop
across the oil filter. If the pressure drop exceeds 45 psid (3 bar), change the filter element.
Oil Filter Inlet (Psi):
Oil Manifold Pressure:
Oil Filter Outlet (Psi):
Suction Pressure (Psi):
Pressure Differential:
Oil Pressure (Psi):
5. During compressor operation ensure that the economizer solenoid (if the economizer is used),
liquid injection solenoid and oil line solenoid (taking into account the time delay) are
energized and de-energize on shut down.
6. If an economizer is used, set the superheat leaving the subcooler to 6°F to 15°F (3°C to 9°C).
Subcooler Vapor Pressure:
Saturation Temperature:
Superheat:
7. Check the oil temperature entering the compressor and ensure that it is less than 190°F (88°C).
Oil Temperature:
8. Check functionality of the LonCEM/Carlyle Electronic Module:
• Disconnect either 5K thermistor from the LonCEM/CEM to verify that the compressor will not start
and all solenoid valves stay off.
• Check to ensure that the motor cooling valve will feed (head pressure may have to be manually
raised).
39