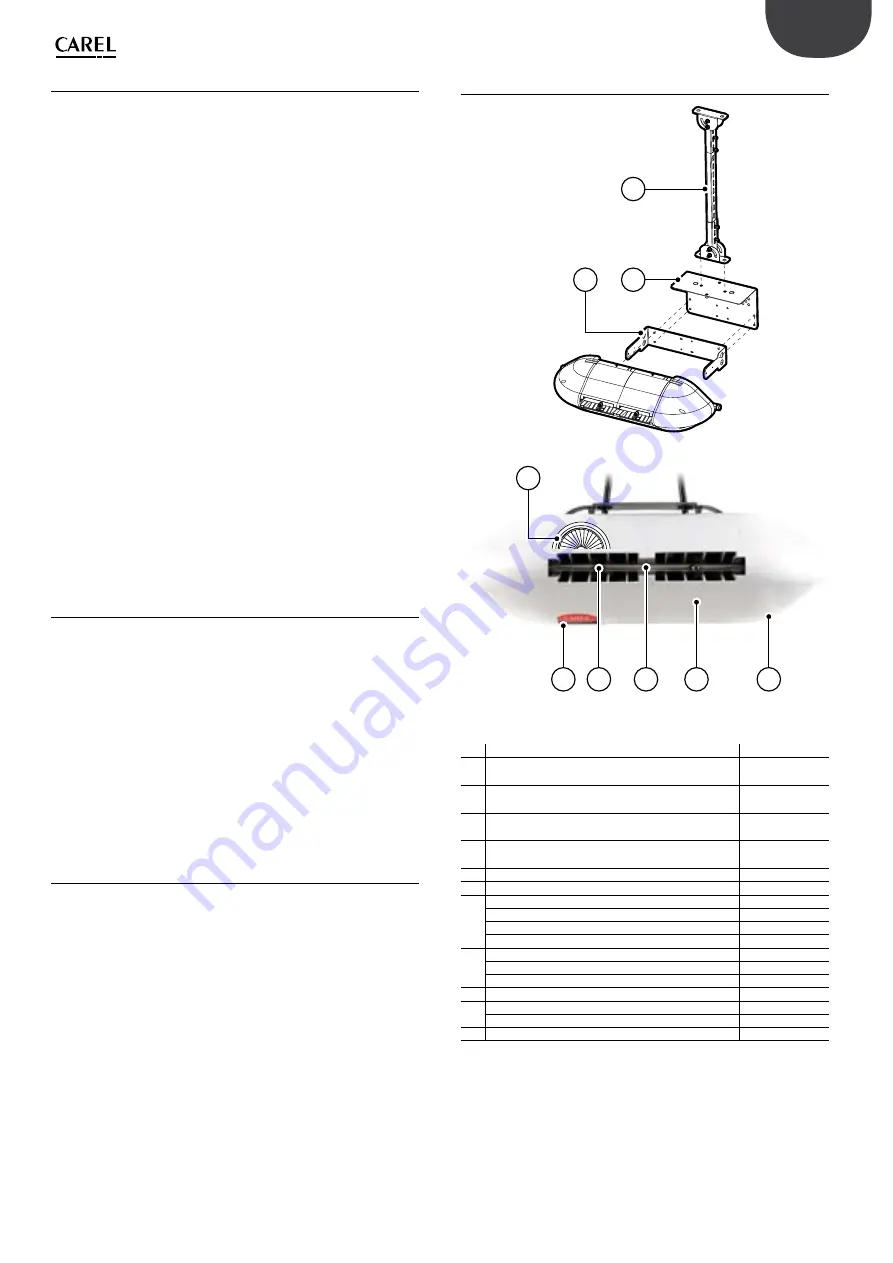
39
ENG
"humiFog direct" +0300073EN rel. 1.2 - 02.05.2019
11.3.2 Gasket and valve replacement
The gaskets and valves require replacement every each 3000 hours,
as signalled on the display by the “3000 hour maintenance” alarm.
Nonetheless, in specific conditions of stress replacement may be needed
earlier.
Carel recommends to check the pump operation every 1000 operating
hours (signalled by notification). If the pump makes noise, or is not able
to reach the required operating pressure (70 bars), the gaskets and valves
may need to be replaced sooner.
Valves and gaskets are consumables, and wear does not reflect a product
malfunction.
To replace the gaskets, proceed as follows:
1.
Disconnect the wiring from the high pressure switch, solenoid valve
BYP and the NTC probe.
2.
Disconnect the pump outlet hose (at the top right).
3.
Unscrew the eight hex screws that hold the pump head to the guard.
4.
Remove the gaskets and replace them with new ones (P/N
UAKVGO1501).
5.
Tighten the eight hex screws so as to secure the pump head to the
guard.
6.
Connect the outlet hose to the pump.
7.
Reconnect the pressure switch, solenoid valve and NTC probe
To replace the valves, proceed as follows:
1.
Unscrew the three hexagonal caps on the front of the brass pump
head.
2.
Unscrew the three hexagonal caps on the top of the brass pump
head.
3.
Replace the six valves with new ones (P/N UAKVGO1501).
4.
Tighten the six caps removed previously.
11.4 50 hour oil change warning
The first “oil change required” maintenance warning is shown after
50 operating hours: this indicates that the oil needs to be changed
immediately. This warning is typically displayed a few days after the
systems is first started. Therefore when starting the system, make sure a
spare can of oil is available for the first oil change, in accordance with the
procedure described in paragraph “11.3.1 Oil change”.
The warning can be easily reset by pressing the “Alarm” button on the
user interface (button at the top left).
For practical reasons, the warning can also be reset after 40 operating
hours, entering the “control menu > screen Da10”. The warning cannot be
reset before 40 operating hours.
11.5 Notification, maintenance warning,
reset hour counter
After 1000 hours of operation, humiFog direct generates a "1000 hour
maintenance" notification, signal only. This is a warning that tells the
user to check correct operation of the system. If the pump can reach the
nominal operating pressure of 70 bars, no action needs to be taken.
The notification can be easily reset by pressing the "alarm" button on the
user interface (top left button).
The same occurs after 2000 hours of operation.
After 3000 hours, on the other hand, humiFog direct generates a "3000
hour maintenance" alarm, which shuts the unit down. In this case, action
needs to be taken on the unit, changing the oil and replacing the pump
gaskets and valves (as described in paragraphs 11.3.1 and 11.3.2).
Will be necessary subsequently reset the alarm in the menu “Control >
screen Da09” and press subsequently the “Alarm” button of the display.
If for some reason the gaskets and valves need to be replaced before
3000 operating hours, the hour counter needs to be reset on screen
Da09. It is recommended, whenever replacing the gaskets and valves, to
also change the oil before resetting the hour counter.
11.6 Blower spare parts
6
5
4
8
8
7
1
2
3
6
5
4
8
8
7
1
2
3
Fig. 11.b
No. Description
Code
1 Wall mounting bracket, single blower, 2 nozzles
(DLA02*F*00)
UAKHW20000
Wall mounting bracket, single blower, 4 nozzles
(DLA04*F*00)
UAKHW40000
2 Ceiling mounting adapter, single blower, 2 nozzles
(DLA02*F*00)
UAKHC20000
Ceiling mounting adapter, single blower, 4 nozzles
(DLA04*F*00)
UAKHC40000
3 Ceiling mounting bracket, L = 0.5 m
UAKVC00500
Ceiling mounting bracket, L = 1.0 m
UAKVC01000
4 2 nozzle water manifold, single blower
Contact CAREL
4 nozzle water manifold, single blower
Contact CAREL
4 nozzle water manifold, double blower
Contact CAREL
8 nozzle water manifold, double blower
Contact CAREL
5 Individual nozzle, flow-rate 1.45 l/h @ 70 bars
UAKMTP0000
Individual nozzle, flow-rate 2.8 l/h @ 70 bars
UAKMTP1000
Individual nozzle, flow-rate 4.0 l/h @ 70 bars
UAKMTP2000
6 Power LED
Contact CAREL
7 CE fan – 230 V 50 Hz
Contact CAREL
UL fan – 120 V 60 Hz
Contact CAREL
8 Plastic cover
Contact CAREL
Tab. 11.b
Содержание humiFog direct DLA02DF000
Страница 2: ......
Страница 4: ...4 ENG humiFog direct 0300073EN rel 1 2 02 05 2019...
Страница 6: ...6 ENG humiFog direct 0300073EN rel 1 2 02 05 2019...
Страница 46: ...46 ENG humiFog direct 0300073EN rel 1 2 02 05 2019 Note...
Страница 47: ......