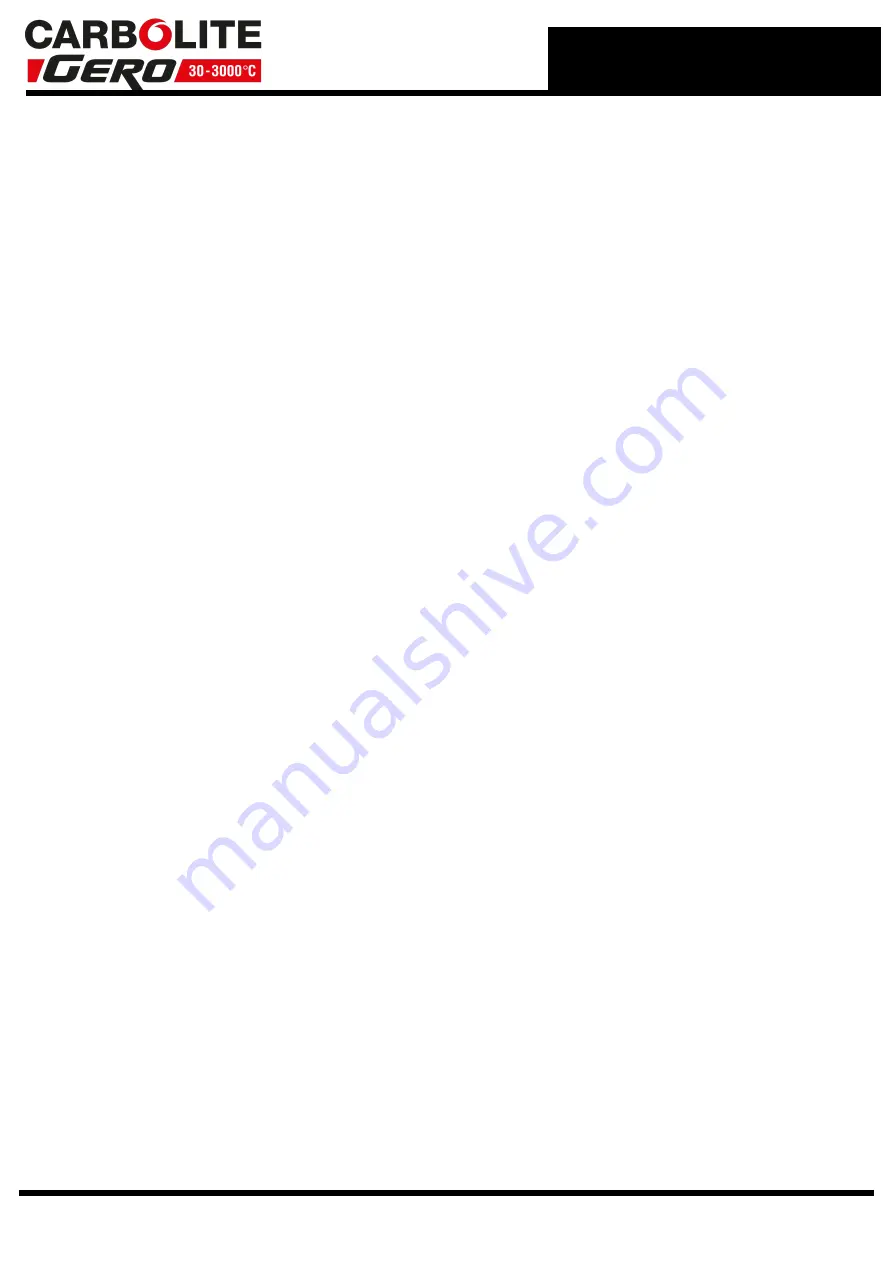
6.4
Gas System Options
The GPCMA is available with a choice of gas system and flowmeter options. The flow of
gas is always turned on and off by program segment events within the temperature
controller/ programmer, regardless of gas system option.
6.4.1
Semi-Automatic Gas System with Analogue Flowmeters - Nitrogen/ Argon
Gas flow rates are required to be set manually via needle valves, but gas flow is turned
on automatically by the temperature controller/ programmer via program segment
events.
All analogue flowmeter options use tapered flow tubes and floats as a visual indicator
of flow rates. Gas flow data cannot be recorded or stored when using analogue
flowmeters.
6.4.2
Semi-Automatic Gas System with Digital Flowmeters
Digital flowmeters read the gas flow rate electronically, but do not control the flow; gas
flow rates are set manually via needle valves.
Data can be read on the front panel display, and is also transmitted to the temperature
programmer, and then onto a digital recorder (if fitted), for remote reading and
recording.
Should the process gas require to be changed, e.g. from nitrogen to argon, digital
flowmeters provide the additional benefit of enabling the operator to change the type
of gas for which the instrument is calibrated, simply by adjusting the settings on the
front panel controls.
6.4.3
Automatic Gas System with Gas Monitoring & Control with Mass Flow Controllers
The mass flow controllers receive their target flow rates electronically from the
temperature programmer, and then control the gas flows accordingly. The flow rates
measured by the mass flow controllers are also transmitted back to the programmer,
and then onto a digital recorder (if fitted), for remote reading and recording.
21
Содержание GPCMA 174
Страница 23: ...23...
Страница 33: ...8 0 Temperature Controller Please refer to the separate temperature controller manual s provided 33...
Страница 48: ......
Страница 49: ...Notes Service Record Engineer Name Date Record of Work...