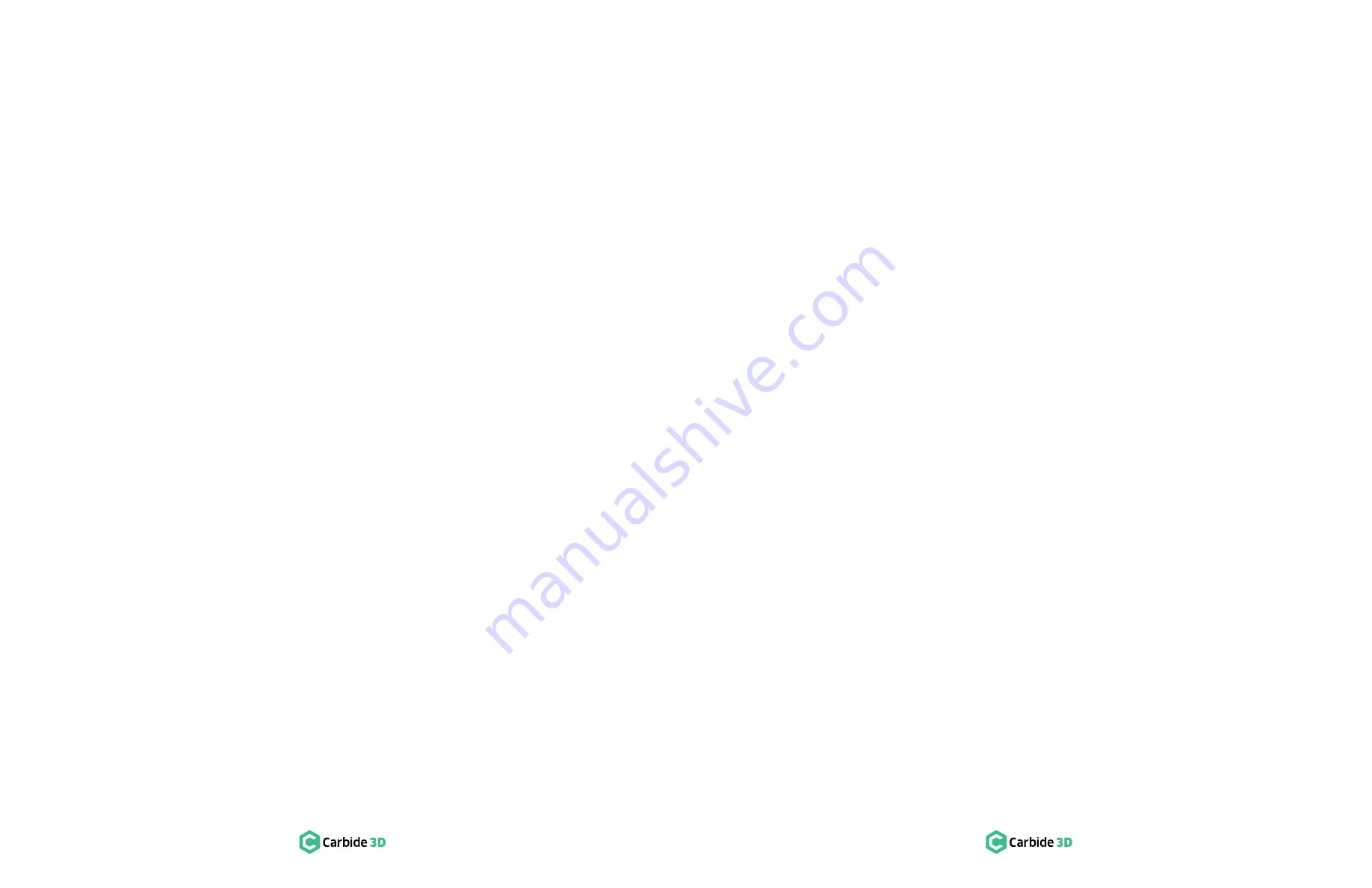
2
docs.carbide3d.com
3
Important Safety Instructions
The Shapeoko is a machine tool and requires the same caution that should be exercised with any power
tool.
Eye Protection
Always wear safety glasses or goggles which are suitably impact resistant.
Hearing Protection
Always wear ear plugs or ear muffs. For long jobs, it may be desirable to wear both. Hearing damage is
cumulative and irreversible, so one should always err on the side of caution.
Respiratory Protection
Always wear a filter or respiratory mask suitable for the type of dust generated by the material being cut. If
necessary, arrange for dust collection and proper ventilation.
Clothing, Hair, and Jewelry
Always ensure that clothing, hair, and jewelry cannot become caught in the machine. Always wear
appropriate clothing: long-sleeved shirts, pants, and suitable footwear are recommended. When doing
metal-working, gloves and an apron are also recommended.
Machine Safety
Never reach into the machine’s working envelope while it is running. Always shut off and unplug the router
to perform tool changes, adjustments, and maintenance. Never leave the machine running unattended.
Always inform someone before operating the machine and check in with them after successfully completing
work. Never allow children to use the Shapeoko 3 unsupervised.
Fire Prevention
Consider the possibility of a fire caused by friction from the router and take suitable fire prevention
precautions (e.g. having a fire extinguisher handy and other suitable precautions).
Outlet Requirements
Plug the router into an outlet that has a dedicated on/off switch. Be sure this is accessible while the machine
is running, in case you should need to shut off the Shapeoko 3 immediately.
End Mill Safety
Use care when handling end mills—both to avoid being cut and to avoid damaging them. Handling end
mills with suitable gloves, or using a cloth to avoid contaminating them, is recommended. Inspect end mills
carefully before each use and ensure that they are securely held by the collet.
Debris Disposal
Recycle or safely dispose of milling debris and dust, keeping in mind flammability, (potential) spontaneous
combustion, and chemical considerations. Even natural materials can have surprising disposal implications.
For example, walnut wood dust is allelopathic (it inhibits plant growth), an irritant to the skin and respiratory
tract, and potentially poisonous to some animals. All of these possible disposal implications are in addition to
the spontaneous combustion hazard posed by all types of sawdust.
Machine Operating Checklist
1.
Be Safe
Always follow the safety guidelines listed on the previous page. Always wear appropriate safety equipment, especially safety
glasses/goggles, hearing protection, and respiratory protection.
2.
Check the Machine
Check that all bolts and set screws are tight, V-rails are in good condition with no nicks or other damage, belts are tight and
in good shape, wiring is in good condition with continuity and securely fastened, and that nothing is frayed or broken and
everything is clear and safe.
3.
Secure the Workpiece
Secure the workpiece (the material being milled) right-side up and in the desired orientation to the worksurface using a
technique appropriate to the material. After securing the workpiece, be certain that the machine is still able to move.
4.
Mount the Router
Mount an appropriate compact router; ensure that it is vertical, square to the machine, and well-secured.
5.
Examine the End Mill
Examine each end mill prior to use to ensure that it is sharp, in good condition, and not chipped (this is best done with a loupe
or magnifying glass). Install the end mill per the compact router manufacturer’s directions so that it projects at least as much
as the deepest intended cutting depth. Check to make certain that the collet is tight and will not work loose during operation
(it needs to be more than finger-tight—the machine will take no notice or care if it works loose).
6.
Clear the Work Area
Ensure the work area is clear and all cables run without interference. Most importantly, check that there is nothing beneath
the rails which might interfere with the movement of the carriages.
7.
Connect to a Computer
To connect the Shapeoko 3 to a computer:
a. Power up the computer.
b. Connect the USB cable to the port at the rear of the Carbide Motion board and to your computer.
c. Start Carbide Motion 5 on your computer.
d.
Turn the Shapeoko 3 on by flipping the in-line rocker switch on the power supply cord to the ON position. Once
powered on, you will see a steady blue LED light on the Carbide Motion board through a slit in the enclosure
cover.
e.
Open the connection to the machine (it should connect and allow you to home the machine).
f. If necessary, home the cutting tool to the proper place in relation to the workpiece.
8.
Disconnect the Touch Probe
If you’re using a Touch Probe, remove the ground clip and secure it safely outside of the machine’s working envelope
9.
Double Check the Work Area
Ensure that nothing has been left in the work area. Optionally, you may traverse the working boundary of the job as a final
check.
10. Send NC File to Machine
Load the NC file (the G-code which gives the machine its instructions). Start the compact router as required and set it to the
correct speed. Follow all prompts for tool changes.
11. Monitor the Machine During Operation
While staying clear of the work area, monitor the machine during operation. Ensure there is no build-up of dust, debris, or
fumes, and that nothing works loose. Do not reach into the machine’s working envelope or insert any object into it while the
machine is operating.
12. Finish and Clean Up
Once the job is complete, turn off the router, return the gantry to the home position or a known offset from home, and ensure
the end mill has stopped spinning before removing the finished piece and any waste. Store end mills carefully when not in use
to protect the cutting edges. Collets and accessories should be cleaned between uses. Wipe them off with a suitable solvent
such as isopropyl alcohol.