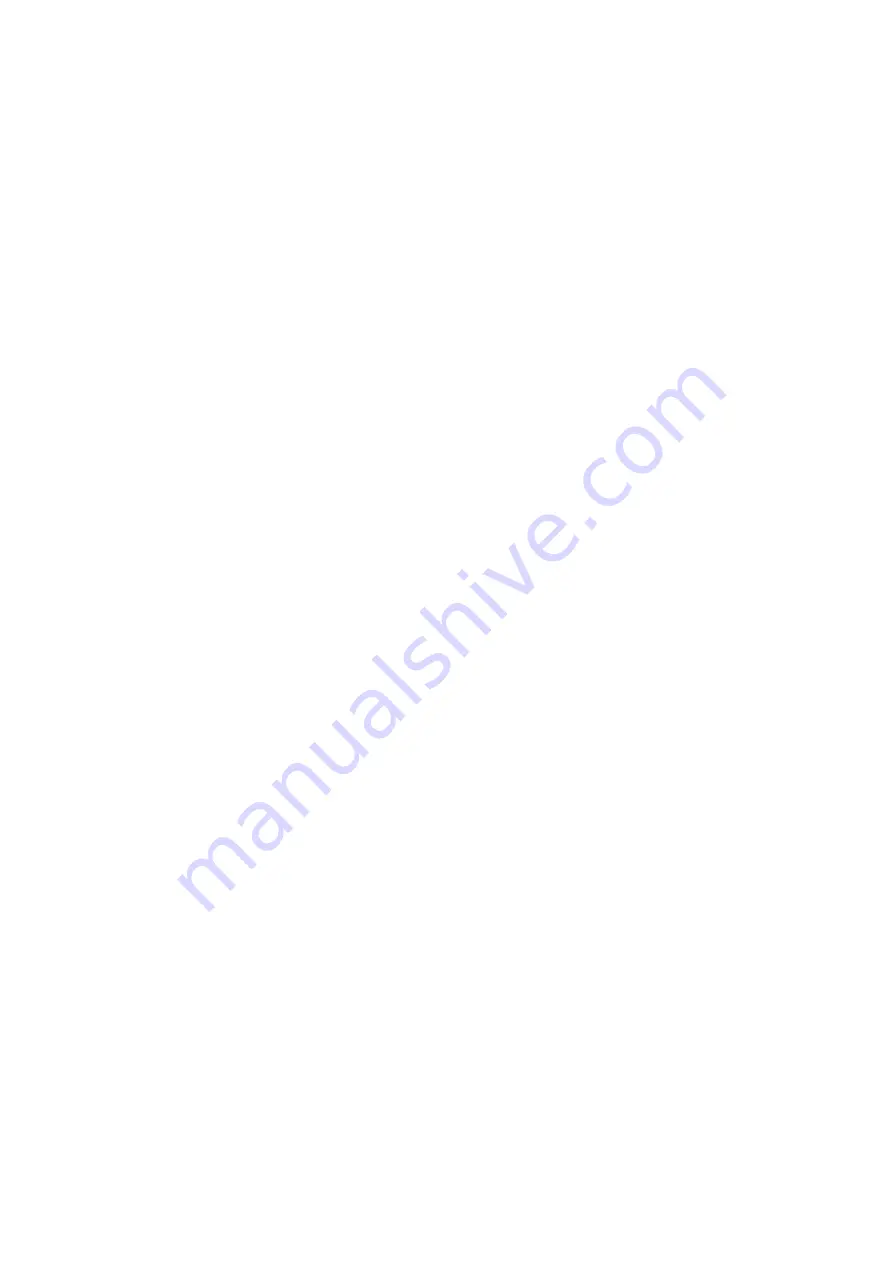
21/23
Default: high frequency impact noise in capillary Zone.
Caused by either reason below:
1>.
The capillary being insert too deep into the evaporator, so when the refrigerant is Jetting, the
end of vibrating capillary will hit the inside of the evaporator.
2>.
Vibration from the capillary touching the inside of the cabinet or air duct board, then when
refrigerant is jetting.
Solutions:
1>. Refer to
(→7.6)
2>. If the capillary touch the inner cabinet and the air duct panel, adjust the position of the capillary and
add the incabloc plastic.
7.8.
Oil jammed noise
Fault: intermittent and deep jet noise coming from inside of the capillary.
Cause: Compressor oil flowing into the cooling system pipe work probably due to the capillary
slightly out of alignment during transportation
Solution: Clean the cooling system pipe, vacuumize it and recharge with refrigerant see
(→7.3)
7.9.
Evaporator freezing.
Because the door seal is not air-proof, or the door is not closed well, cause much water fill in the
cabinet, and the water got frozen when it encounter the cold air, sometimes the ice is too thick, and
it will block the fan or broken the fan.
The solution:
1 >.
Replace the door seal or close the door well. If the door seal is slightly not air-proof, it can be
repaired by the heat dryer.
Aiming at the distortion of the seal with the heat dryer, and move up and down until it expand to
the normal state. When it is cool, check it with the door closed, if there is any distortion, dry it
again until it fix for the door.
(Fig.18)
2 >. If the fan is broken, replace the fan.
Содержание WI152
Страница 1: ...WI152 Caple 15cm wine cabinet Technical information...
Страница 2: ......
Страница 4: ......
Страница 10: ...6 23 2 Electrical circuit diagram 3 Cooling system diagram...