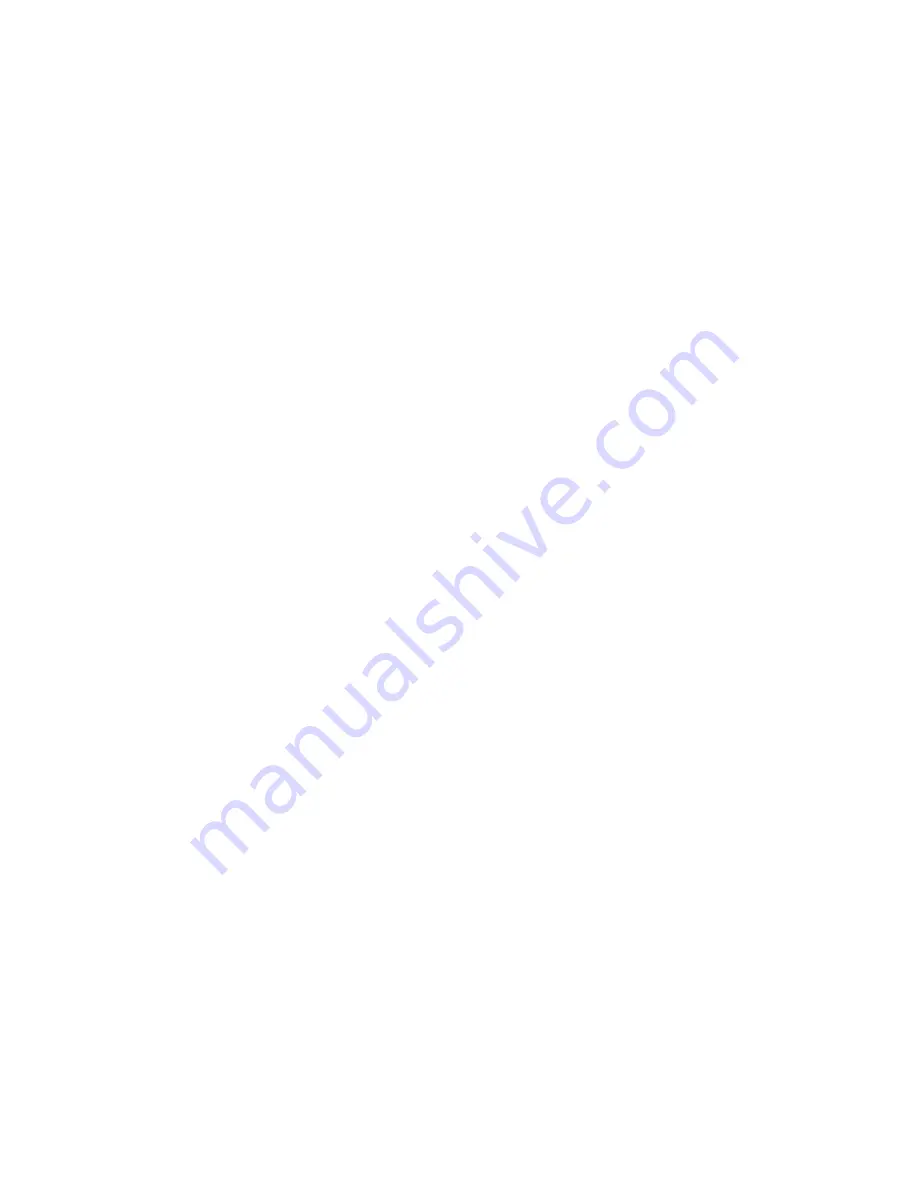
CHAPTER 4
TROUBLESHOOTING
I.
PREFACE ............................... 4-1
II.
IMAGE DEFECTS.................... 4-8
III. PAPER JAMS
TROUBLESHOOTING .............. 4-14
IV.
PAPER TRANSPORT
TROUBLESHOOTING .............. 4-18
V.
MALFUNCTION
TROUBLESHOOTING .............. 4-20
VI. MALFUNCTION STATUS
TROUBLESHOOTING .............. 4-21
VII. MEASUREMENT AND
ADJUSTMENT ........................ 4-28
VIII. MAINTENANCE AND
SERVICING............................. 4-35
IX. LOCATION OF CONNECTORS . 4-48
Содержание LBP-3260
Страница 8: ......
Страница 10: ......
Страница 12: ...This page intentionally left blank 1 2 CHAPTER 1 ...
Страница 27: ...Figure 1 5 7 1 17 CHAPTER 1 ...
Страница 36: ...This page intentionally left blank 1 26 CHAPTER 1 ...
Страница 38: ......
Страница 40: ......
Страница 55: ...2 15 CHAPTER 2 ...
Страница 71: ...This page intentionally left blank 2 31 CHAPTER 2 ...
Страница 104: ......
Страница 108: ...2 68 CHAPTER 2 ...
Страница 110: ......
Страница 160: ......
Страница 194: ...This page intentionally left blank 4 34 CHAPTER 4 ...
Страница 209: ...Figure 4 9 2 4 49 CHAPTER 4 J56 J51 J50 J54 J55 J19 J10 J24 J204 J213 J214 J222 J1302 J1304 J1303 J1301 J102 J217 ...
Страница 210: ...4 50 CHAPTER 4 ...
Страница 211: ...APPENDIX I GENERAL TIMING CHART A 1 II GENERAL CIRCUIT DIAGRAM A 3 III LIST OF SIGNALS A 5 IV MESSAGES TABLE A 11 ...
Страница 212: ......
Страница 214: ......
Страница 222: ...A 10 APPENDIX This page intentionally left blank ...
Страница 234: ...PRINTED IN JAPAN IMPRIME AU JAPON 0199AT0 70 CANON INC The printing paper contains 70 waste paper ...