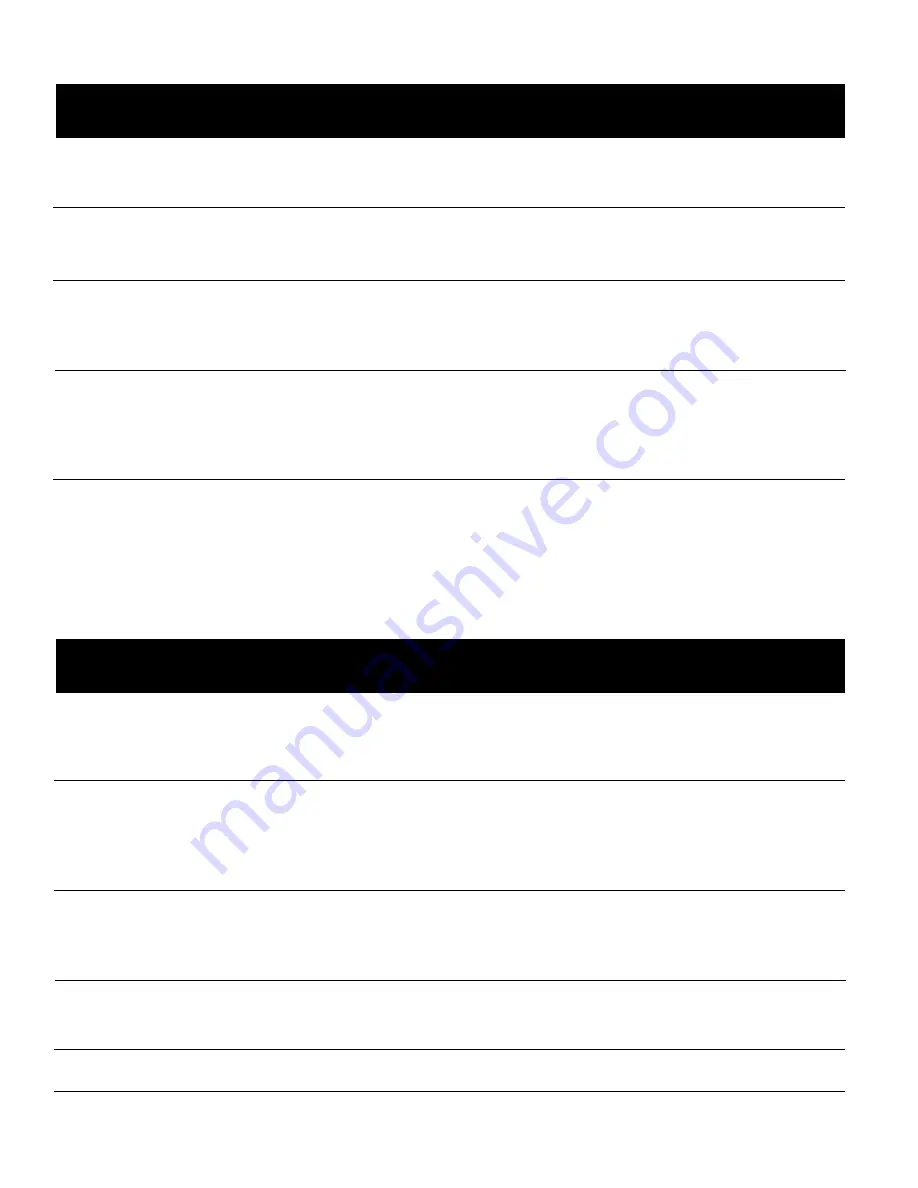
8
Troubleshooting Chart - Welder
Symptom
Possible Cause(s)
Corrective Action
1. No power at receptacle
2. Broken or damaged power
cable
1. Inadequate current at
electrode
2. Poor connections at welder
1. Accidental contact with work
piece
2. Current leakage caused by
moist clothing or work area
1. Use of extension cord
2. Electrode diameter too large
3. Overloaded circuit
1. Wrong type of electrode
2. Electrode diameter too large
3. Work piece not properly
grounded
4. Heavy loads making power
line voltage low
For Information About This Product, Call 1-800-746-5641
Bead is intermittently too
thin or too thick
Ragged depressions at
edge of weld
Weld bead does not
penetrate workpiece
Electrode sticks to work
piece
Electrodes sputter and stick
1. Inconsistent travel speed
2. Output amp setting incorrect
1. Travel speed too fast
2. Arc length too short
3. Output amp setting too high
1. Inconsistent travel speed
2. Output amp setting too low
3. Electrode diameter too large
1. Arc length short
2. Amp setting low
Damp electrodes
1. Check circuit fuse or circuit breaker
2. Power cable requires service
1. Check work clamp, cable and connection to work piece.
Check electrode cable and clamp
2. Check all welder external connections
1. Avoid contact with work piece
2. Make sure clothing and work area are dry
1. If possible, relocated welder to avoid use of extension
cord. If relocation of welder is not possible, use thicker
(lower gauge number) extension cord
2. Use smaller diameter electrode
3. Welder requires a
dedicated
115V circuit
1. Verify that electrode is for alternating current (AC) use
2. Use smaller diameter electrode
3. Verify proper grounding. (No paint, varnish or corrosion)
4. Run welder on dedicated 115V circuit
Welder does not hum
when turned on
Welder hums but does not
weld
Welder gives trickle shocks
Welder overheats - blows
fuses, trips circuit breaker
Arc difficult to strike
Troubleshooting Chart - Welds
Symptom
Possible Cause(s)
Corrective Action
1. Carefully watch and control the width of the molten
weld bead
2. Adjust output amp setting or change to smaller diameter
electrode
1. Watch orange molten weld puddle and control bead
width
2. Practice running electrode across workpiece with welder
OFF
3. Reduce output amp setting
1. Decrease and maintain constant travel speed
2. Increase output amp setting or change to smaller
diameter electrode
3. Recommend either 1/16 or 5/64 diameter
1. Lift electrode to correct arc length as soon as arc is struck
2. Increase amp setting or change to smaller diameter
electrode
Use dry electrodes and store in dry location