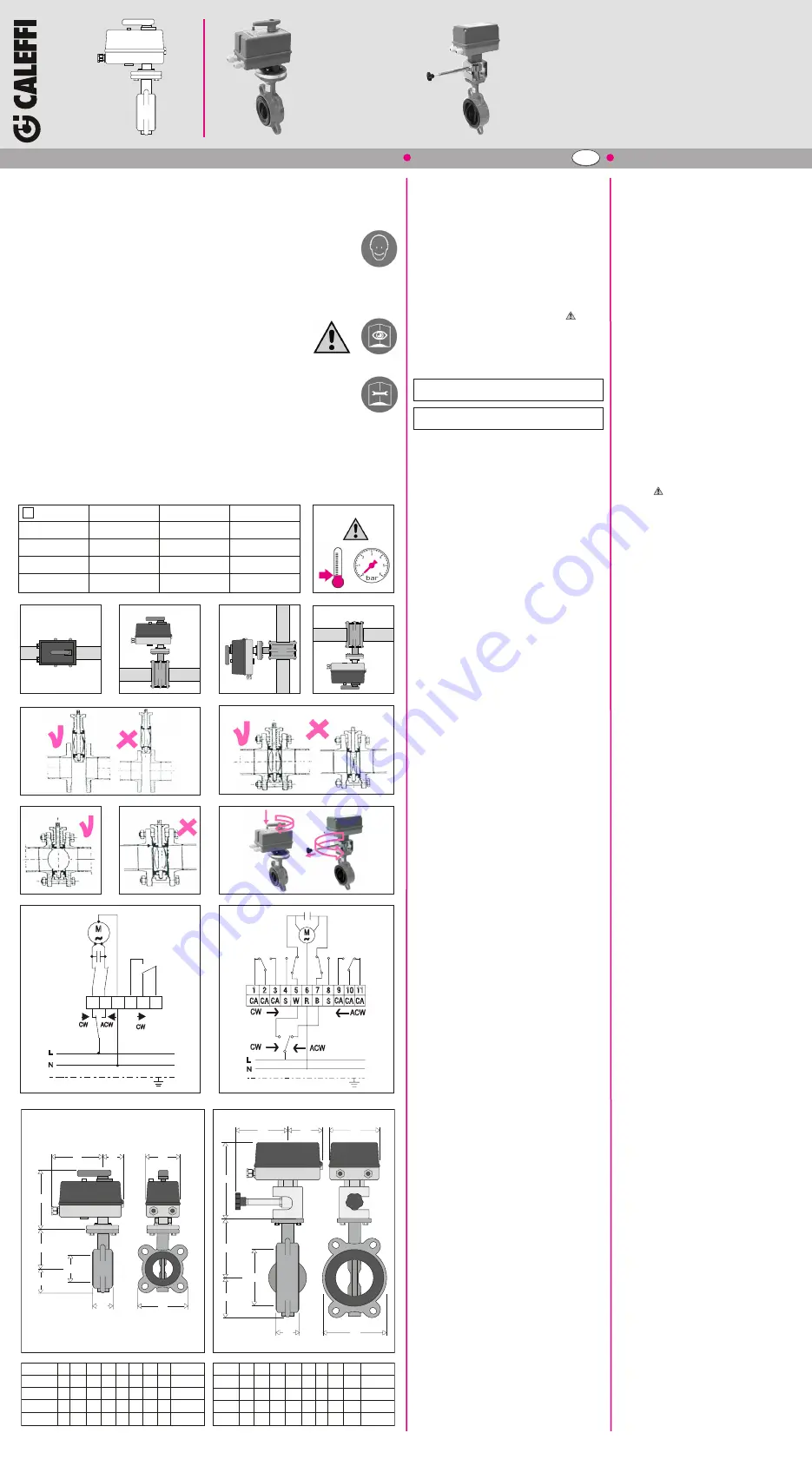
© Copyright 2017 Caleffi
H0000741.01
www.caleffi.com
INSTRUCTIONS FOR INSTALLATION,
COMMISSIONING AND MAINTENANCE
Thank you for choosing our product.
Further technical details relating to this
device are vailable at www.caleffi.com
MOTORISED BUTTERFLY VALVE,
WAFER TYPE
Warnings
The following instructions must be read and understood before
installing and maintaining the product. The symbol
means:
CAUTION! FAILURE TO FOLLOW THESE INSTRUCTIONS COULD
RESULT IN A SAFETY HAZARD!
Safety
The safety instructions provided in this document must be
observed.
LEAVE THIS MANUAL AS A REFERENCE GUIDE
FOR THE USER
DISPOSE OF THE PRODUCT IN COMPLIANCE
WITH CURRENT LEGISLATION
Function
The motorised, wafer type, butterfly valves can be used on
heating and air-conditioning systems as zone or shut-off
devices. Thanks to their compact body, they need reduced
spaces for the installation.
Technical specifications
Materials
Body:
cast iron EN-GJL-250C EN 16482
Control stem:
stainless steel EN 10088-3 (AISI 420)
Butterfly:
cast iron
EN-GJS-400 15C EN 16482
Butterfly seal:
EPDM
Control stem seal:
EPDM
Performance
Medium:
water, glycol solutions
Max. percentage of glycol:
30%
Max. working pressure:
16 bar
Max. differential pressure:
6 bar
Flanged connections:
PN 16
Can be coupled with EN 1092-1 counterflange
Conformity:
directive PED 2014/68/EC
(97/23/EC until July the 18
th
2016)
directive 2006/42/EC
Face to face distance:
EN 558-1 ( DIN 3202 T3 K1)
ISO 5752 T5
Upper flange:
EN ISO 5211
Ambient conditions
(valve + actuator)
Medium working temperature range:
-10–95°C
Ambient temperature:
- Operation:
-10–65°C EN 60721-3-3 Cl. 3K4,
max. humidity 95%
- Transportation:
-30–70°C EN 60721-3-2 Cl. 2K3,
max. humidity 95%
- Storage:
-20–70°C EN 60721-3-1 Cl. 1K2,
max. humidity 95%
Actuator technical specification
Synchronous motor three point type
Electrical supply:
230 V (ac), 24 V (ac)
Power consumption:
- DN 32–DN 80:
4,5 VA
- DN 100–DN 200:
10,5 VA
Auxiliary microswitch contact rating:
- DN 32–DN 80:
16 (4) A - 250 V (ac)
- DN 100–DN 200:
16 (6) A - 250 V (ac) - double switch
Protection class:
- DN 32–DN 80
IP 42
- DN 100–DN 200
IP 65
Operating time:
180 s (rotation 90°)
With manual opening system.
Hydraulic characteristics (fig. A)
Installation (fig. B – C – D – E – F - G - H - I - L)
Assembly and disassembly should always be carried out while
the system is cold and not in pressure (fig. B).
The butterfly valve is bidirectional and can be mounted in the
following ways:
• the recommended position is on horizontal pipe with
the actuator laying on the side (actuator axis in horizontal
position), with the lower part of the butterfly opening from
upstream to downstream (fig. C);
• on horizontal pipe with the actuator in vertical position
above the valve body (fig. D). The actuator should never be
installed upside down (fig. F);
• on vertical pipe, with cable glands pointing downward
(fig. E).
Compatibility with pipes and flanges
Check that the flange diameter allows the butterfly rotation.
The valves are intended for fitting between collar and flanges.
Installation on pipe
General: the valve should not be used to separate the flanges
to be inserted within, otherwise the seal can get damaged
(fig. G). Separate the flanges by means of a specific tool in
order to obtain a distance between the flanges which is
suitable for the valve insertion without forcing.
Installation on existing pipe
1. The valve should be installed between the flanges without
difficulty. Separate the flanges by means of a specific tool.
Flanges not perfectly separated could damage the gasket
or butterfly during the insertion of the valve (fig. G).
2. Close the butterfly so that it is about 5-10 mm inside
the valve body. A fully open butterfly could in fact get
damaged by scraping against the flanges.
3. Position the valve between the flanges. Centre the valve
body and put in all the bolts.
4. Completely open the valve.
5. While z the valve correctly aligned with the flanges, and
removing the tool used to separate them, screw the nuts
by hand (fig. H).
6. Carefully close the valve and check that the butterfly
rotates freely.
7. Completely reopen the butterfly and fully screw the nuts.
The bolts should be fully screwed with the valve in fully
open position, otherwise the gasket could be compressed
in not optimum conditions. This could result in too high
closing torque or leakage (fig. I). Do not use o-ring or grease
(fig. L).
Installation on new pipe
1. With the butterfly almost closed, put the two flanges on the
body with a few bolts. Close the tap between the flanges.
2. Install everything on the pipe.
3. Fix the flanges to the pipe with a few welding spots.
4. Undo the nuts and remove the valve from the flanges.
5. Complete the welding of the flanges and allow to cool
completely.
6. Refit the valve as described above in the section
“Installation on existing pipe”.
DO NOT COMPLETELY WELD THE FLANGES WITH THE
VALVE FITTED AS THIS COULD DAMAGE THE GASKETS.
ENGLISH
EN
Manual opening /closing (fig. M)
After cutting off the electric supply, it is possible to open/close
manually the valve by means of the specific manual command.
On DN 32-80 sizes, press the clutch button and rotate the lever
(both are located on the actuator cover). For DN 100–DN 200
sizes, pull the clutch knob (located at the end of the lever) and
rotate the lever into the desired position.
Wiring diagram (fig. N - O)
- Actuator SM 100 for DN 32–DN 80 valves (fig. N):
1 clockwise rotation (CW)
2 anticlockwise rotation (ACW)
3 common
Auxiliary microswitch
(diagram at the end of the indicated rotation)
4 normally open NO
5 normally closed NC
6 common
- Actuator SM 200 for DN 100–DN 200 valves (fig. O):
5 clockwise rotation (CW)
6 common
7 anticlockwise rotation (ACW)
Auxiliary microswitches
(diagram at the end of the indicated rotation)
1 normally closed NC
2 common
3 normally open NO
9 normally open NO
10 common
11 normally closed NC
Safety instructions
Warnings
The following instructions must be read and understood
before installing and maintaining the device.
The symbol means:
Safety
CAUTION! YOUR SAFETY IS INVOLVED. FAILURE TO FOLLOW
THESE INSTRUCTIONS MAY RESULT IN DANGER.
THE PRODUCT SUPPLIED WITH THIS INSTRUCTION
SHEET IS CALLED “DEVICE”.
1. The device must be installed, commissioned and
maintained by a licensed technician in accordance with
national regulations and/or relevant local requirements.
2. If the device is not installed, commissioned and maintained
correctly in accordance with the instructions provided in
this manual, it may not work properly and may endanger
the user.
3. The device is not intended to be used by people
(children included) with reduced mental, physical and
sensory faculties or with lack of experience unless they
are supervised or instructed in the use of the device by a
person responsible of their safety.
4. Clean the pipes of all deposits, rust, incrustations, limescale,
welding slag and any other contaminants. The hydraulic
circuit must be clean.
5. Make sure that all connection fittings are watertight.
6. When connecting water pipes, make sure that threaded
connections are not mechanically overstressed. Over time
this may result in breakages, with consequent water leaks
which could harm people and/or damage property.
7. Water temperatures higher than 50°C may cause severe
burns. When installing, commissioning and maintaining
the device, take the necessary precautions so that these
temperatures will not endanger people.
8. If the water is particularly hard or contains a lot of impurities,
suitable filtration and treatment should be performed
to water before it enters the device, in accordance with
current legislation. Otherwise the device may be damaged
and will not work properly.
9. For optimal operation, any air in the medium must
be removed. For safety reasons, due to the high
compressibility of air, testing the entire system, and
especially the valves, for watertightness using compressed
air is not recommended.
10. Any use of the device other than its intended use is
prohibited.
11. The device is not suitable for use in agricultural applications.
12. Any coupling of the device with other system components
must be made while taking the operational characteristics
of both units into consideration. An incorrect coupling
could compromise the operation of the device and/or
system.
1. CAUTION: Risk of electric shock. Live parts. Cut off the
electric supply before opening the device box
2. Wiring must be made according to the state of the art and,
in case of connection to the electric network, the minimum
cross-section of the cable must be equal to 0,75 mm
2
.
3. During installation and maintenance procedures, always
take care to avoid direct contact with live or potentially
hazardous parts.
4. The device must be installed in a specific area and must not
be exposed to leakages or humidity, direct sunlight, bad
weather, sources of heat or high-intensity electromagnetic
fields. This device cannot be used in areas at risk of
explosion or fire.
5. The device must have a separate connection to an
independent bipolar switch. If the equipment needs
maintenance, cut off the electric supply before any work
is carried out. Do not use devices with automatic or timed
reset, or which may be reset accidentally.
6. Use suitable automatic protection devices in accordance
with the electrical characteristics of the zone in which
the device is installed and in compliance with current
legislation.
7. The device must always be earthed before it is connected
to the electric supply. If the device needs to be removed,
the earth connection should always be disconnected after
the other electrical wires. Make sure that the building has
been earthed professionally, in accordance with current
legislation.
Declaration of conformity
We C.N.T. CASPANI SRL declare that our motorized valves
are constructed in accordance with directives 2014/30/EC e
2014/35/EC and assume full responsibility for conformity with
the standards laid down therein when operated according fo
their intended purpose, as described in the operated hand-
book.
Manufactured by
CNT CASPANI S.R.L.
CALEFFI S.p.A.
S.R. 229, N. 25
28010 Fontaneto d’Agogna (NO)
Italia
X
M
1 2 3 4 5 6 7 8 9 10 11
CA
CA CA CA
CA CA S
S
W R B
CW
CW
ACW
ACW
L
N
CW
ACW
L
N
1 2 3 4 5 6
CW
M
A
Size
Kv (m
3
/h)
Size
Kv (m
3
/h)
DN 32/40
149
DN 100
861
DN 50
207
DN 125
1345
DN 65
351
DN 150
1937
DN 80
520
DN 200
3445
B
A
DN 32/40
DN 50
DN 65
DN 80
B
56
62
69
94
C
110
120
135
141
D
152
152
152
152
E
118
118
118
118
F
50
50
50
50
I
79
79
79
79
G
38
50
52
52
H
116
130
137
143
A
DN 100
DN 125
DN 150
DN 200
B
106
127
133
170
C
165
180
193
225
D
227
227
227
227
E
192
192
192
192
F
97
97
97
97
I
108
108
108
108
G
58
65
65
65
H
147
180
206
257
I
H
A
A
B
C
D
E
F
I
H
G
G
E
F
B
C
D
Mass (kg)
3,5
4,5
4,5
5
Mass (kg)
9
11
12
16
X
X
X
E
F
M
1 2 3 4 5 6 7 8 9 10 11
CA
CA CA CA
CA CA S
S
W R B
CW
CW
ACW
ACW
L
N
CW
ACW
L
N
1 2 3 4 5 6
CW
M
G
H
I
L
M
N
O
C
D
639
042
DN 32 /40 230 V
639
052
DN 50 230 V
639
062
DN 65 230 V
639
082
DN 80 230 V
639
044
DN 32 /40 24 V
639
054
DN 50 24 V
639
064
DN 65 24 V
639
084
DN 80 24 V
639
102
DN 100 230 V
639
122
DN 125 230 V
639
152
DN 150 230 V
639
202
DN 200 230 V
639
104
DN 100
24 V
639
124
DN 125 24 V
639
154
DN 150 24 V
639
204
DN 200 24 V