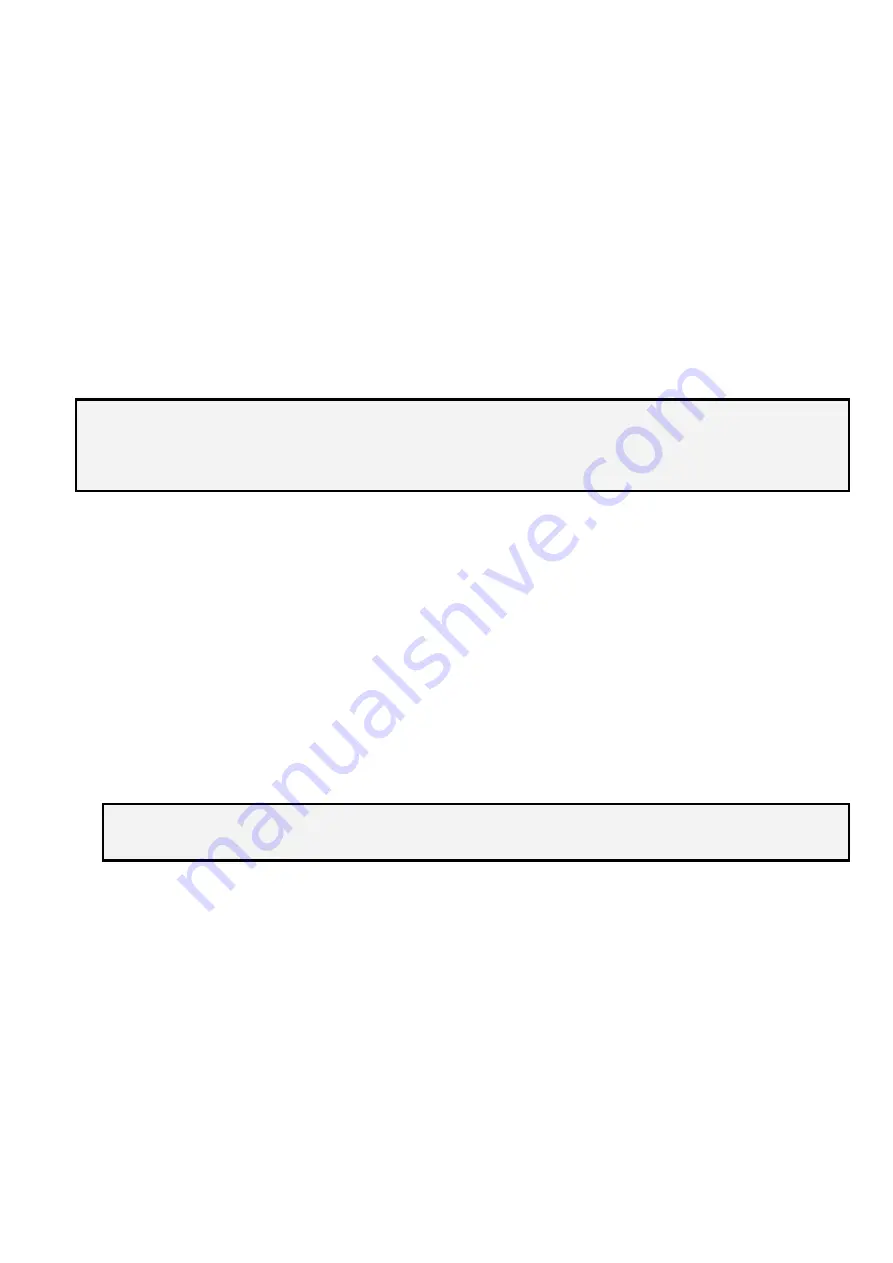
16
Pistons
Replace the piston skirt if it is lined, especially on a low-pressure pump, which has no piston rings. Check that
play on the piston pins is not excessive.
Piston Rings
On the pumps equipped with these rings check that they have no marks or breakages. If necessary, replace.
Check Valves
Carefully check the cage. If cracked or very worn on the fins, replace. The seats are suitable, even if worn,
provided that the working surface (where the cap beats) has no cuts or deformations. The same applies to the
valves. The springs should not be worn. It is preferable to change the whole valve assembly.
N.B.
Excessive wear on the check valves on a pump which has only worked a few hours could be caused by
the pump running at a higher speed than the maximum allowed (550 rpm) or by the presence of sand or
other abrasive substances in the liquid pumped.
Pressure Accumulator
It is always advisable to check the wear on the lower accumulator diaphragm and replace it if necessary. Inflate
according to the working pressure as specified below:
Pump Pressure (bar)
Air Pressure (bar)
0
– 5
0
– 2
5
– 15
2
– 6
15
– 20
6
– 8
When dismantling a pump, which has been working, it is advisable to replace the O-rings gaskets and seals in
general to avoid the risk of having to check everything again.
Point 4
To reassemble proceed as when dismantling but in reverse, bearing in mind the following:
A) All the shoulder rings should be mounted with the bevel in correspondence with the shaft shoulder.
B) On pumps with piston rings, these should be positioned on the piston with the gaskets diametrically
opposite
C) The cylinders should be re-mounted with at least 4 oil supply holes in the direction of the shaft rotation to
assist air drainage, checking that the piston ring joints are not on line with the cylinder holes.
D) The check valve must be positioned correctly. Looking at the suction manifold can help. The valve near
the suction manifold must allow the liquid to enter the head; consequently the delivery valves should be
mounted the other way up.
NOTE
If all valves are mounted (by mistake) in the suction direction the pump will explode on starting. If mounted in
the delivery direction, the pump will not be able to suck.
E) Before re-mounting the heads, make sure that the moving parts turn freely. If they are stiff or tight, check
the assembly of the moving parts to ensure that this has been carried out correctly. One can then
proceed with assembling the heads.
F) It is a good idea to remember that a plastic hammer can be useful in both dismantling and re-assembling
the pump, but is should always be used with care.
G) After Completing assembly, fill with oil to the maximum tank capacity.
DO NOT REPLACE STOPPER.
H) Expel Air as follows:
Turn the pump shaft slowly by hand keeping it inclined with respect to the transversal shaft. Bubbles of air
will rise to the surface in the oil tank and the level will fall. Keep the oil level topped up so that air does not
enter the pump. Continue for a few minutes until no more air bubbles are expelled from the tank. Top up
the oil level to between ¼ and ¾ of the sight glass, then replace the oil stopper.
I) To eliminate any further air trapped between the piston and the diaphragm, loosen the oil tank stopper,
run the pump at 200-300 rpm for a few minutes without pressure. Check the oil level again and after
screwing the stopper shut the pump can work normally.