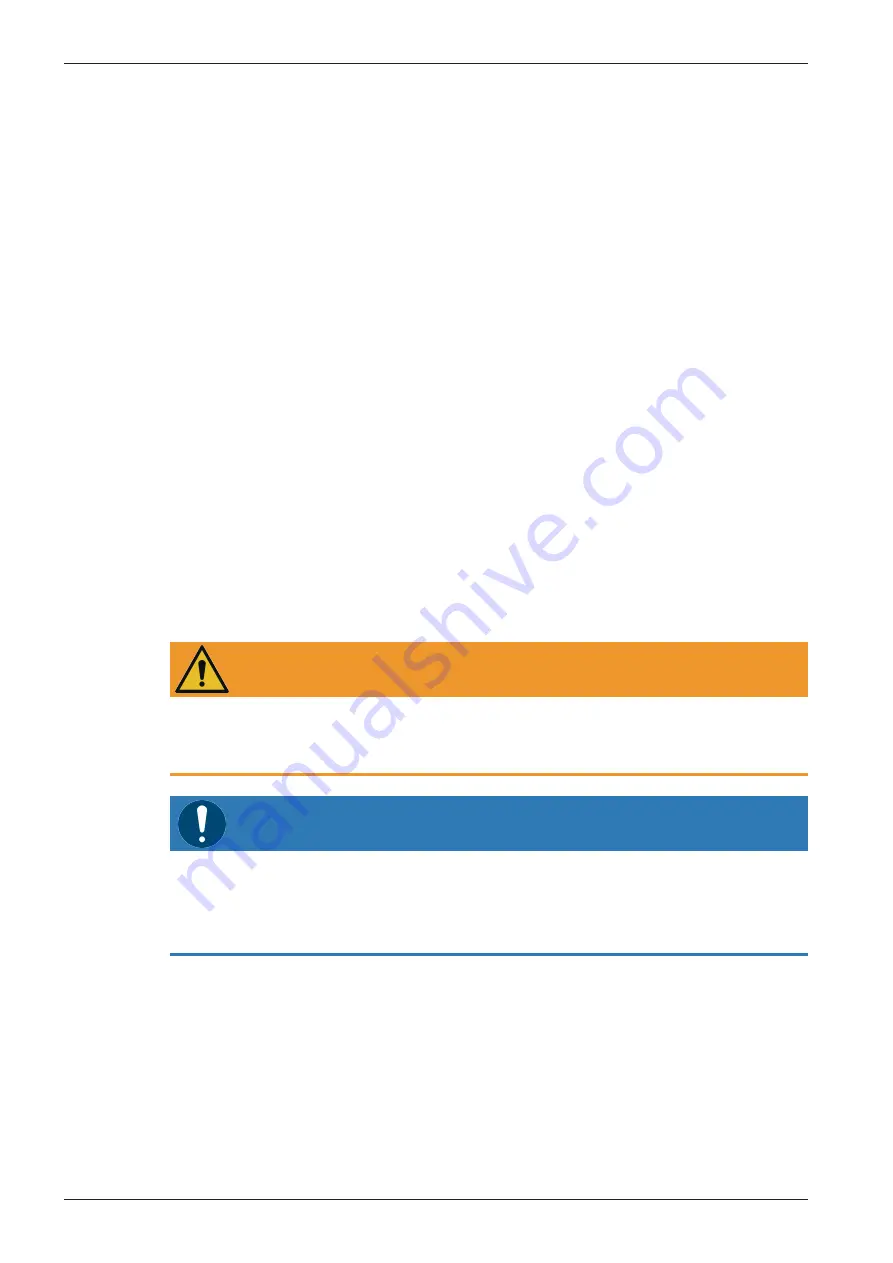
5 | Installation
12 | 44
Instruction Manual COBRA NC 0400 B WCV_EN_en
●
Make sure that cooling air inlets and outlets of the motor fan are not covered or obstructed and
that the cooling air flow is not affected adversely in any other way.
●
Make sure that the oil sight glass (OSG) remains easily visible.
●
Make sure that enough space remains for maintenance work.
●
Make sure that the machine is placed or mounted horizontally, a maximum of 1° in any direction
is acceptable.
●
28].
●
Check the cooling liquid level, see
Cooling Liquid Level Inspection
●
Make sure that the cooling water complies with the requirements, see
If the machine is installed at an altitude greater than 1000 meters above sea level:
●
Contact your Busch representative, the motor should be derated or the ambient temperature
limited.
5.2
Connecting Lines / Pipes
●
Remove all protective covers before installation.
●
Make sure that the connection lines cause no stress on the machine‘s connection; if necessary use
flexible joints.
●
Make sure that the line size of the connection lines over the entire length is at least as large as
the connections of the machine.
In case of long connection lines it is advisable to use larger line sizes in order to avoid a loss of
efficiency. Seek advice from your Busch representative.
5.2.1
Suction Connection
WARNING
Unprotected suction connection.
Risk of severe injury!
●
Do not put hand or fingers in the suction connection.
NOTICE
Ingress of foreign objects or liquids.
Risk of damage to the machine!
If the inlet gas contains dust or other foreign solid particles:
●
Install a suitable filter (5 micron or less) upstream from the machine.
Connection size(s):
– DN63 ISO-K, DIN 28404
– DN80 PN6, EN 1092-1
If a purge gas system or a liquid flushing device being installed:
– DN80 PN16, EN 1092-1
If the machine is used as part of a vacuum system:
●
Busch recommends the installation of an isolation valve in order to prevent the machine from
turning backwards.