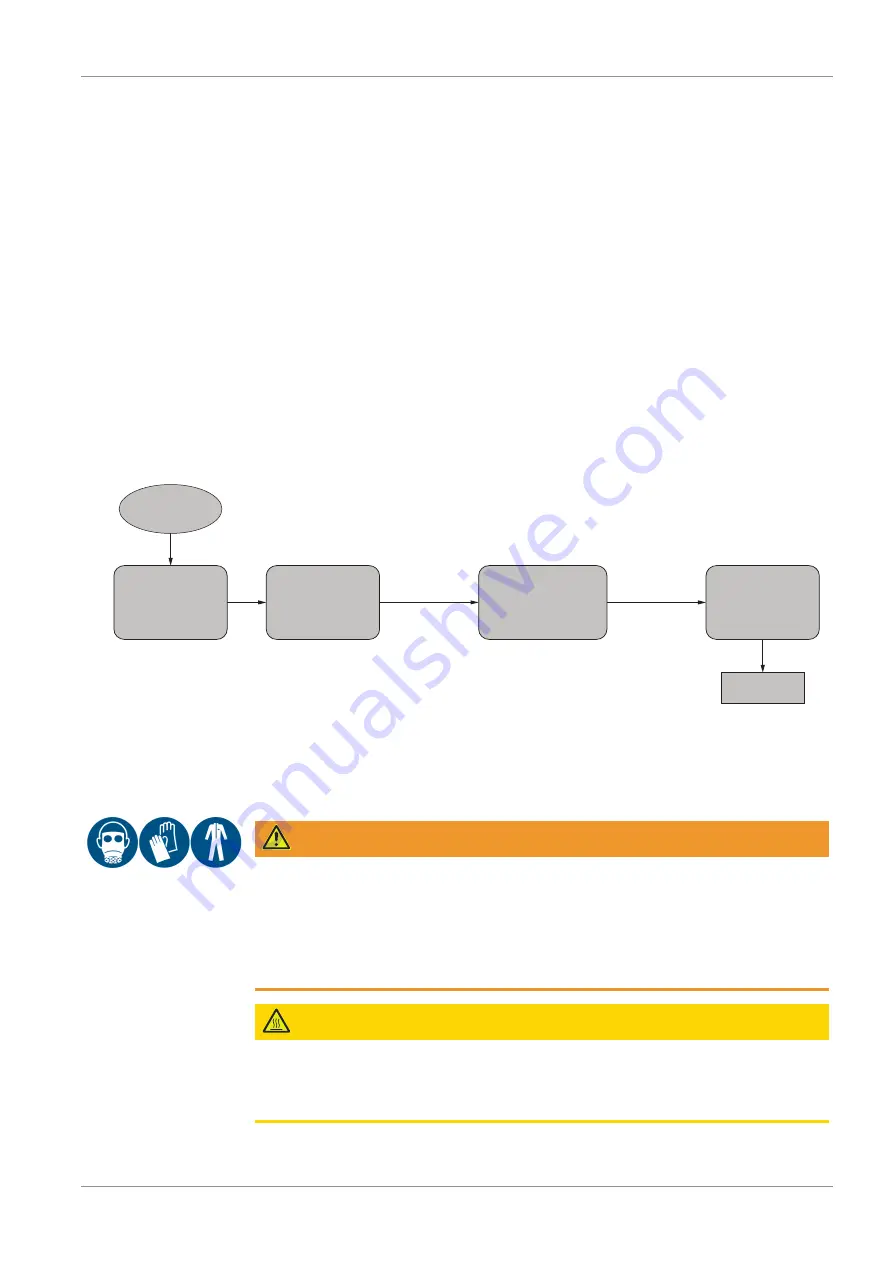
Maintenance | 7
0870219588_NS0600C_WCV_Ex_-0000_IM_en
25 / 40
• Turn on the barrier gas supply.
• Adjust the barrier gas pressure and volume flow.
• Switch on the machine.
• Make sure that the maximum permissible number of starts does not exceed 2 starts
per hour. Those starts should be spread within the hour.
• Make sure that the operating conditions comply with the
• After a few minutes of operation, perform an
.
• After a few minutes of operation, perform a
Cooling Liquid Level Inspection [
.
As soon as the machine is operated under normal operating conditions:
• Measure the motor current and record it as reference for future maintenance and
troubleshooting work.
6.1 Conveying Condensable Vapours
The machine, equipped either with a gas ballast valve or a dilution gas system, is suitable
for the conveyance of condensable vapours within the gas flow.
If condensable vapours are to be conveyed:
START
Open the gas ballast
valve* or the
dilution gas sytem*
(solenoid valve)
Warm up the
machine
30 minutes
30 minutes
• Open the inlet
valve
• Perform the process
• Close the inlet
valve
Close the gas ballast
valve*
or
the dilution gas
system*
END
* optional accessories
• Continuously drain condensate from the condensate drain plug (CD) of the silencer
(SI) (Optional).
7
Maintenance
WARNING
Machines contaminated with hazardous material.
Risk of poisoning!
Risk of infection!
If the machine is contaminated with hazardous material:
• Wear appropriate personal protective equipment.
CAUTION
Hot surface.
Risk of burns!
• Prior to any action requiring touching the machine, let the machine cool down first.
Содержание COBRA NS 0070-0600 C
Страница 38: ...Note ...
Страница 39: ...Note ...