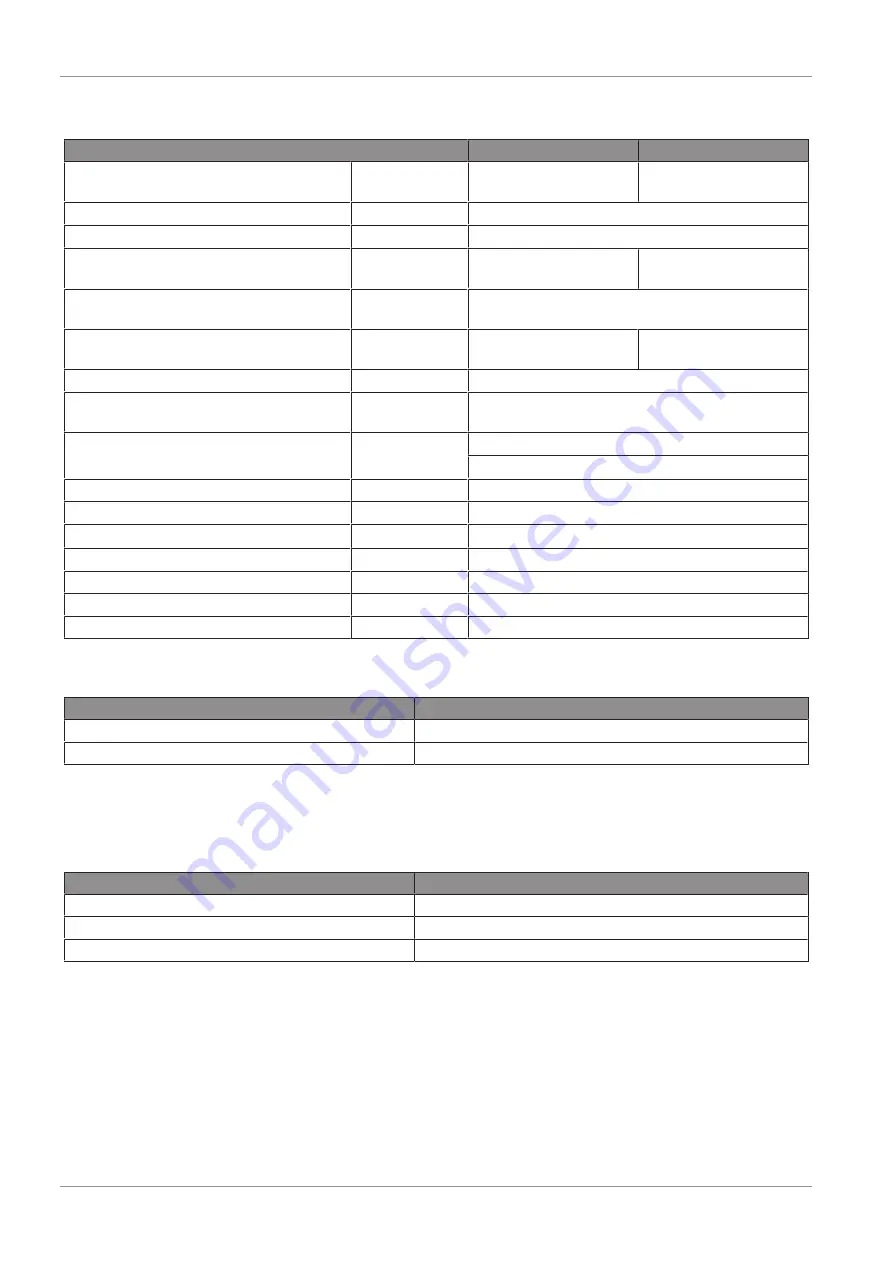
12 | Technical Data
36 / 40
0870567092_NC0630C_WCV_A0006_IM_en
12 Technical Data
NC 0600 C
NC 0630 C
Pumping speed
(50Hz / 60Hz)
m³/h
600 / 600
630 / 630
Ultimate pressure (without gas ballast)
hPa (mbar) abs.
≤
0.01
Ultimate pressure (with gas ballast)
hPa (mbar) abs.
≤
0.1
Nominal motor rating
(50Hz / 60Hz)
kW
18.5 / 18.5
15 / 17
Nominal motor speed
(50Hz / 60Hz)
min
-1
3000 / 3600
Noise level (EN ISO 2151)
(50Hz / 60Hz)
dB(A)
≤
74 /
≤
76
≤
70 /
≤
75
Ambient temperature range
°C
5 … 50
Max. allowable counter pressure at the dis-
charge
hPa (mbar)
200
Max. allowable gas inlet temperature
°C
≤
50 hPa (mbar)
►
200
>
50 hPa (mbar)
►
70
Relative humidity
at 30 °C
90%
Ambient pressure
Atmospheric pressure
Cooling water requirements
See
Oil capacity - motor side
l
1.7
Oil capacity - suction side
l
0.6
Cooling liquid capacity approx.
l
29
Weight approx.
kg
600
13 Cooling Liquid
Zitrec M-25 (ready-to-use)
Part number 5 L packaging
0831 563 469
Part number 25 L packaging
0831 563 468
The cooling liquid Zitrec M-25 is ready-to-use and does not require additional water.
For further information, consult the website
14 Oil
VE 101
ISO-VG
100
Part number 1 L packaging
0831 000 099
Part number 5 L packaging
0831 000 100
Содержание COBRA NC 0600 C
Страница 38: ...Note...
Страница 39: ...Note...