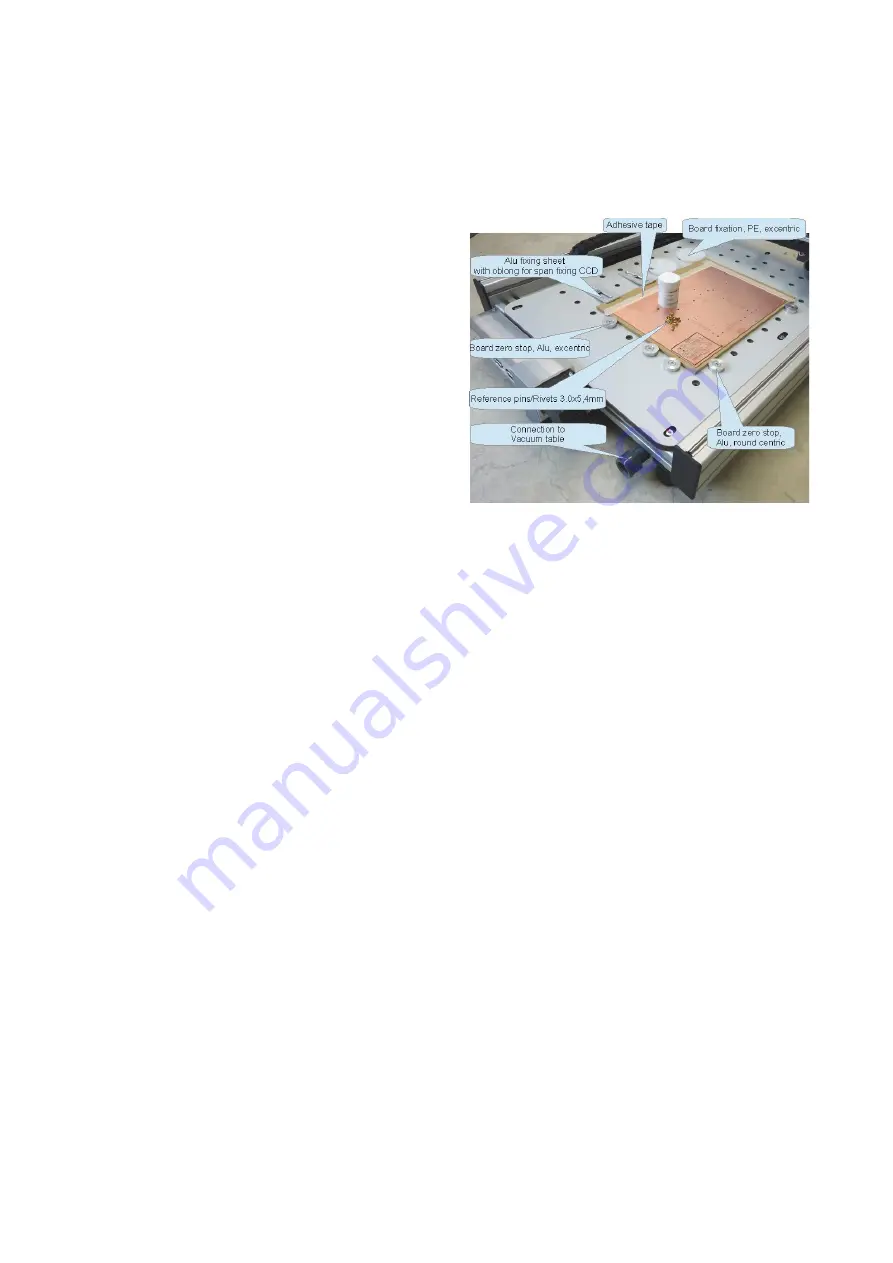
CCD
Operator's manual
Page 26 /35
Fixing the boards
Clamp fixing
The machine table has holes each 50 mm. They
serve to fix the aluminium and plastic flanges
coming with the machine and allow to clamp on
all four edges 1 base sheet and 1 - 3 boards of
the same size of 1.5 mm. The two flanges near
to the machine's zero position determine the
board zero position. Use the two big white plastic
disks with the 3 eccentric mounting holes to
clamp the boards. The small eccentric flanges
can be used to align the board(s) in parallel to a
main axis. This fixing method is in most cases
sufficient for all drilling applications, as well as for
fixing a base sheet for isolation milling and con-
tour cut-out routing. Disadvantage: backing
board and PCB must have the same size.
Span fixing
You may insert screws into the holes in the ma-
chine table. Using stripes of metal or PCB material, this offers you the possibility to fix the plates
from on top. This method will apply mainly for engraving aluminium. Disadvantage: the metal
stripes lie on top of the plate and may be touched by the spindle.
Reference pins / Isolation milling
Use a drilling base that is significantly larger than the board. Create a drill file with two or six refer-
ence holes. These reference holes form a mirror axis, which is needed to reference the bottom
layer of your PCB. We recommend to place the reference holes outside the design, at best on the
long side of the PCB. In our software IsoCam an automatic function to generate these reference
holes is included .
The drill backing board needs to be thick enough to provide a secure grip for the reference
pins/rivets. A 6 mm MDF board is recommended. Instead of steel pins (which stick out of the
board and possibly interfere with the milling action), we prefer rivets. The flat head of these rivets
is almost level with the PCB and does not interfere with the depth limiter.
This fixing method has two advantages: The board is held securely, even for a later cutting out the
PCB from the raw material. And a perfect match between top and bottom of the milled board is en-
sured by the fact that the mirror axis in the software and the physical mirror axis of the reference
holes match exactly.
Also use reference pins in the wet process technique, if you first drill the board, then remove the
board from the machine to make through hole plating and etch the tracks and after that return to
the machine to make the final cut out routing.
Adhesive tape
simplest, fastest and cheapest method. The adhesive tape can be drilled and routed without prob-
lems. In contrast to the clamping and span-method, you can process only one board at a time. If
you need to reference a double sided PCB, you can use the fiducial recognition option of Route-
Pro3000.
Vacuum fixation
As an option all CCDS can be equipped with a vacuum table. This table can be connected to a va-
cuum pump (membrane or better: side channel pump) or a vacuum cleaner. The vacuum table
sucks through the mounting holes of the CCD-table. You can put an MDF-drill backing board on
Содержание ATC
Страница 1: ...CCD Operator s manual Page 1 35 ...