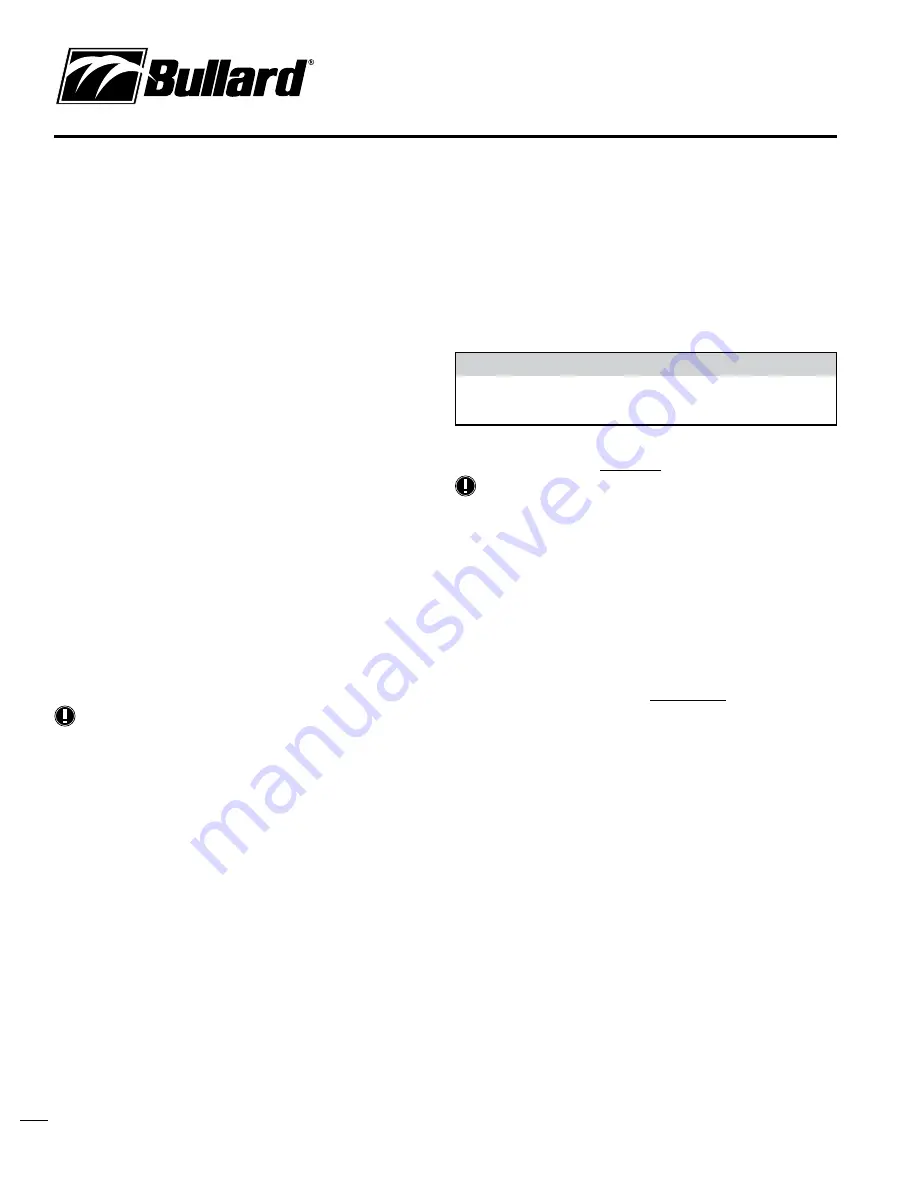
www.bullard.com
6
Maintaining the
fr
ee-
air Pump /
tr
oubleshooting
guide
9. With the air flowing, put on the respirator by following the directions in the
respirator manufacturer’s Instruction Manual.
YOU ARE NOW READY TO ENTER THE WORk AREA.
10. When finished working, leave the work area wearing the respirator with the air
still flowing. Once outside the contaminated area, remove the respirator, turn the
pump off, then disconnect the air supply hose using the quick-disconnect couplings.
See the respirator’s Instruction Manual for proper inspection, maintenance
and storage procedures for the respirator you are using.
Maintaining the free-air Pump
FOR THE PUMP TO OPERATE AT ITS OPTIMUM PERFORMANCE LEvEL, THE
FOLLOWING ROUTINE MAINTENANCE PROCEDURES MUST BE PERFORMED.
FOR THE SPECIFIC LOCATION OF THE PUMP COMPONENTS REFERRED TO
BELOW, SEE THE LIST OF PUMP COMPONENTS ON PAGE 4.
Maintaining the air Motor
The air motor is a rotary 4-vane type. The vanes require no adjustment and will last
5,000-15,000 hours if properly maintained.
1. Flush MOTOR (9):
If motor is sluggish or inefficient, flush with LOCTITE SAFETY SOLvENT, or any
non-toxic, nonflammable industrial cleaning solvent).
Use the following directions to flush the motor:
a. Shut-off the pressure into the air motor and disconnect the airline from the
DRIvE AIR INLET (13).
b. Locate the pump in a safe area. Solvent will spray from the exhaust port
during flushing. Protect your face and eyes from the spray.
c. Remove the PLUG (11) and pour several teaspoons of solvent into the opening.
d. Replace the PLUG, reconnect the airline back to the DRIvE AIR INLET. Turn
the pressure back on. Run the pump at a very low speed (10-20 RPM) for
approximately one minute or until all the solvent is flushed.
note:
Motor bearings are grease packed and sealed. They require no
maintenance.
Maintaining the Pump
Pump is rotary 4 vane type. The vanes require no adjustment and will last 5,000 to
10,000 hours if properly maintained.
1. Maintain FILTERS
- Dirty filters restrict outlet air flow and can cause the motor to overload or
cause premature pump failure.
- Replace CARBOFINE OUTLET FILTER CARTRIDGE (6) at least once every 200
running hours (Catalog No. S17101).
- Replace INLET FILTER (1) at least once every 500 running hours to maintain
proper pressure and full air flow. To check the filter - while running the
pump, momentarily remove the FILTER (1) from the INLET PIPE (2). If the
motor speeds up or the outlet pressure shown on GAUGE (5) increases, the
filter needs replacement.
2. Flush PUMP if necessary
Should dirt, foreign particles, moisture or oil be permitted to enter, the vanes
will become sluggish, resulting in a lowering of outlet air pressure. Flush the
pump with LOCTITE SAFETY SOLvENT. (DO NOT USE kEROSENE).
Pump should be operated for at least a few minutes every one to two weeks
to reduce the likelihood of rust film forming in the rotor.
If pump remains idle in humid environment for some time, FLUSHING may be
required to remove rust film in chamber and rotor slots.
Use the following directions to flush pump:
a. Turn-off THROTTLE vALvE (10) to stop the pump before flushing.
b. Before flushing, disassemble and remove the following parts from the pump:
- Respirator air supply hose(s)
- Inlet Filter and Pipe Stand
- Outlet Filter Jar and Outlet Filter
c. With the pump running, pour several teaspoons of solvent into the pump’s
inlet port. Repeat the flushing if necessary.
�
WaRning
RUN THE PUMP FOR A SUFFICIENT TIME TO PURGE ALL TRACES OF THE SOLvENT
BEFORE REPLACING THE FILTERS, RECONNECTING THE AIR SUPPLY HOSE(S)
AND USING THE RESPIRATOR.
3. AvOID ExCESSIvE SPEEDS and PRESSURE
- Avoid running above the 25 psig range for any length of time.
note:
NEvER lubricate this oil-less pump. BEARINGS are grease packed
and sealed. They require no further lubrication.
ensuring Pump Performance
To make sure your pump will perform properly:
1. Always locate the pump’s air inlet in a clean, breathable air environment.
2. DO NOT contaminate inlet air with exhaust air from air motor
3. Change OUTLET FILTER every 200 running hours.
4. Make sure RELIEF vALvE is fully seated (no bleed-off).
5. Always check Respirator Air Supply Hoses to make sure they are free of kinks.
6. Set incoming compressed drive air at 85 psig or higher. Set output air pressure
as specified in respirator owner’s manual.
troubleshooting guide
outlet PRessuRe too high
- Adjust THROTTLE vALvE (10)
- Check for kinked air supply hoses
- Reset pressure adjustment valve
outlet PRessuRe too loW
- Adjust THROTTLE vALvE to increase motor speed
- Check for clogged INLET FILTER
- Check that outlet filter jar is screwed on tight
- Check for clogged OUTLET FILTER
- Check pressure relief valve and adjust if necessary
- Check drive air inlet pressure
- Check for leaks in air hose
- verify proper pressure range for your respirator
- verify that respirator and hose are connected when gauge reading is taken
- Check to see that gauge is functioning properly
- Flush pump with LOCTITE SAFETY SOLvENT