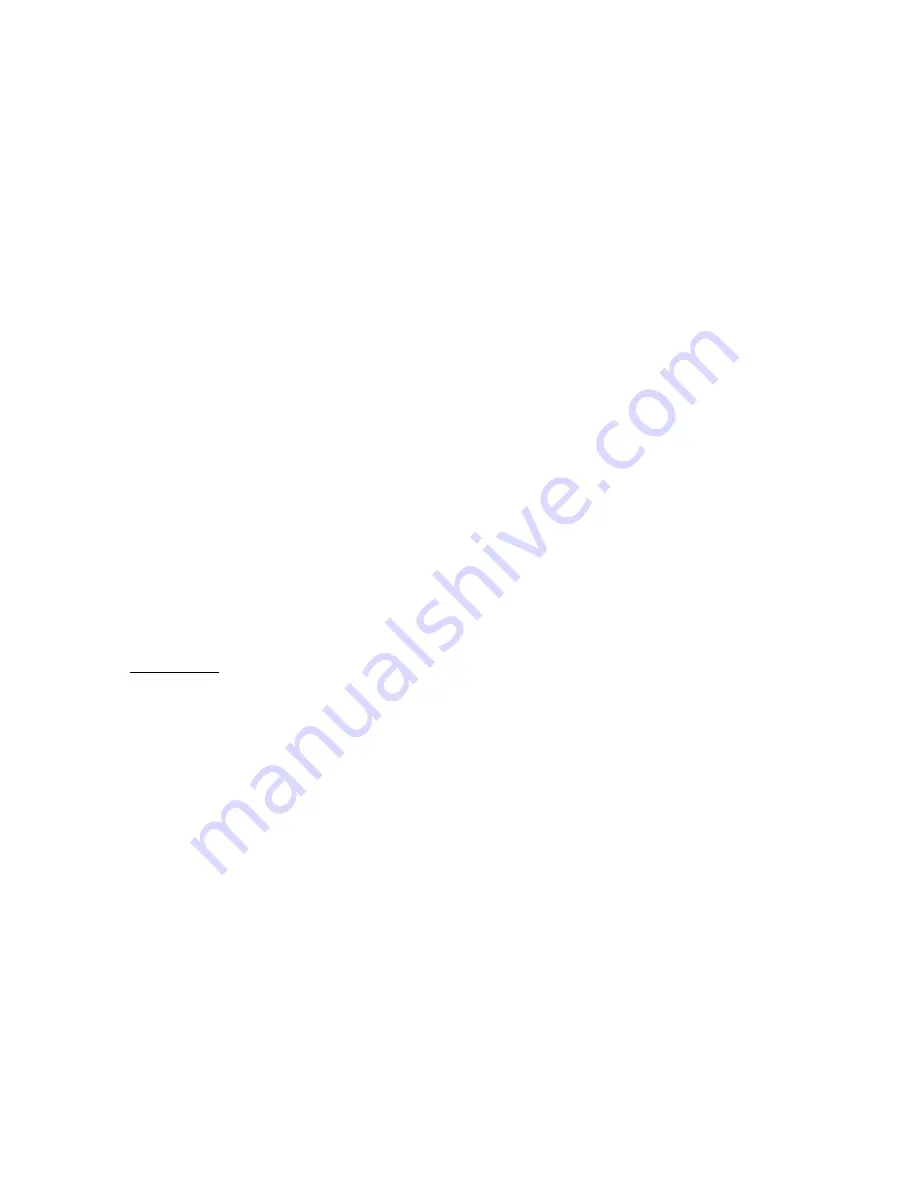
- 18 -
SECTION 3. INSTALLATION
3.1 UNPACKING
PROCEDURE
1.
Remove system components from shipping containers and situate near a 28 VDC
power source. If possible, save shipping containers for future use.
2.
Make sure that all system components are accounted for (Figure 1).
3.
Ascertain they are properly matched by serial number, or have been calibrated
together.
4.
Visually inspect exterior of system components and interconnecting cables for
damage. If damage is evident take appropriate action for corrective maintenance
and repair, as required.
5.
Record serial numbers.
3.2
INITIAL OPERATIONAL CHECK
Before mounting on the aircraft, it is advisable to give the system an initial bench
check to verify that it works properly and to become familiar with its operation.
See Section 4.3 for operation off the aircraft.
3.3
INSTALLATION ON AIRCRAFT
Sensing unit
The sensor is normally located on the aircraft fuselage, mounted through the exterior skin,
with the inlet fitting exposed to the airstream. Other locations, such as a boom, can also be
used.
The pressure field along the side of an aircraft in flight varies with location, and may be
greater or less than the ambient or static pressure. Attempt to locate the sensor at a point
where the pressure is reasonably near static pressure. A side mount is advisable to avoid
pressure changes with change of aircraft pitch, and to avoid rain while parked. Avoid prop
wash and areas of large local pressure changes, such as wing surfaces, behind radar domes
and struts, etc. It is usually safe to mount the sensor near the static instrument ports, as
they are located at or near a point of static pressure.
In pressurized aircraft, try to avoid locating immediately downstream of windows or other
cabin penetrations that might have slight leaks and
thereby affect the air being sampled. A
forward location allows a somewhat better penetration of the aircraft boundary layer by the probe,
and so is somewhat preferable (although usually not critical).
The inlet fitting is designed for use on either the right or the left side of the aircraft, but not
both. The consequence of mounting on the wrong side of the aircraft is: upward pointing
inlet and exhaust holes and the likelihood of collecting liquid water in the sensor.
Содержание 1011C
Страница 7: ...7 C B A Figure 1 Dew Point Hygrometer System shown with optional cables...
Страница 9: ...9...
Страница 12: ...12 Figure 3 Dew Point Sensing Unit A B C...
Страница 14: ...14 Figure 4 Control Indicator Unit F A B C D E...
Страница 17: ...17 Figure 6 Power Unit Internal...
Страница 23: ...23 Figure 9 Flow Test Fixture Hookup...
Страница 28: ...28 FIGURE 10 System Response Characteristics...
Страница 31: ...31 Recommended cable Belden YQ27540 Figure 11 Wiring Diagrams...
Страница 32: ...32 Recommended cable Belden YQ27540 Wiring Diagrams Continued...
Страница 33: ...33...
Страница 34: ...34 Figure 13 Vapor Pressure e vs Dew Point TD or Saturation Vapor Pressure es vs Temperature T...
Страница 36: ...36 Figure 15...
Страница 37: ...37 Figure 16 Aspirating Fixture Hookup...
Страница 38: ...38 Figure 17 1011C Hygrometer Complete...
Страница 40: ...40 Table 2 Dew Point to Frost Point Conversions...
Страница 41: ...41 Table 3 Dew Point Error due to Pressure Change in Sampling System...
Страница 47: ...47...
Страница 48: ...48...