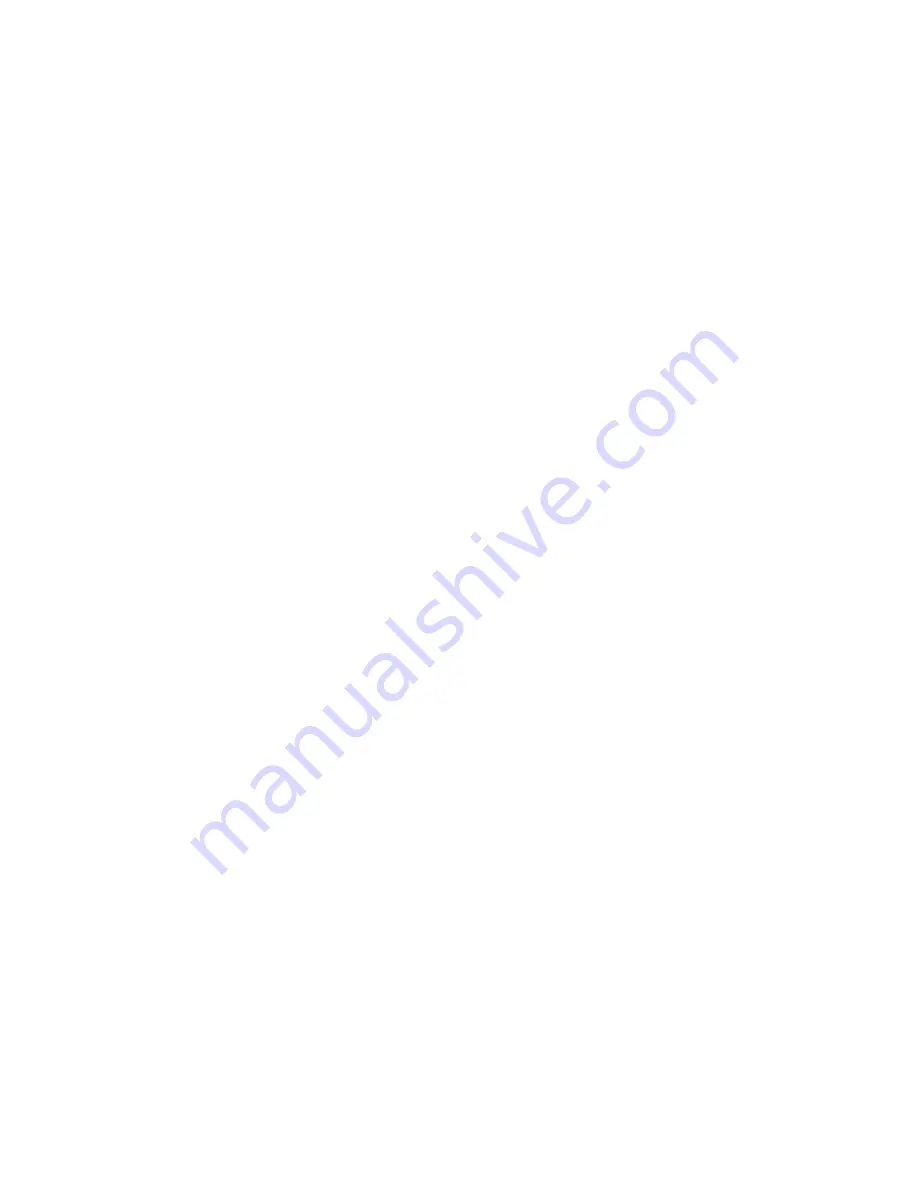
LK3-B438E Mark II
CONTENTS
1. NAME OF EACH PART
...............................
0
1
2. SPECIFICATIONS
.........................................
0
2
2-1.
Specifications ....................................... 2
2-2.
Program list .......................................... 3
3. INSTALLATION
.............................................
0
6
3-1.
Power table ........................................... 6
3-2.
Installing the motor ............................. 7
3-3.
Installing the motor pulley .................. 7
3-4.
Installing the control box .................... 8
3-5.
Installing the rubber cushions ............ 9
3-6.
Installing the oil pan ............................ 9
3-7.
Installing the cushions ......................... 9
3-8.
Installing the machine head ............... 10
3-9.
Installing the head rest ........................ 10
3-10. Installing the liquid cooling tank,
optional ................................................. 10
3-11. Installing the operation panel ............. 11
3-12. Connecting the ground wire ............... 11
3-13. Connecting the cords ........................... 12
3-14. Installing the V-belt .............................. 13
3-15. Installing the belt cover ....................... 14
3-16. Installing the foot switch ..................... 14
3-17. Installing the motor cover ................... 15
3-18. Installing the spool stand .................... 15
3-19. Installing the button tray ..................... 15
3-20. Installing the eye guard ...................... 15
4. LUBRICATION
............................................... 16
4-1.
Lubrication points ................................ 16
5. OPERATION
.................................................. 17
5-1.
Name and function of each
operation panel item ........................... 17
5-2.
Operating procedure ............................ 19
6. CHECKING THE SEWING PATTERN
....... 20
7. CORRECT USE .........................................
21
7-1.
Selecting the needle and thread ........ 21
7-2.
Installing the needle ............................ 21
7-3.
Threading the upper thread ................ 21
7-4.
Winding the lower thread ................... 22
7-5.
Replacing the bobbin case and
threading the thread ............................ 23
7-6.
Thread tension reference guide ......... 23
7-7.
Inserting the button ............................. 25
7-8.
Adjusitng the button holder ............... 25
7-9.
Adjustment by the accessory
spring .................................................... 25
8. SEWING ...................................................
26
9. MAINTENANCE AND INSPECTION .......
27
9-1.
Cleaning the rotary hook .................... 27
9-2.
Lubrication ............................................ 28
9-3.
Draining the oil ..................................... 29
9-4.
Cleaning the control box air inlet
port ........................................................ 29
9-5.
Cleaning the eye guard ....................... 29
9-6.
Checking the needle ............................ 29
10.STANDARD ADJUSTMENTS .................
30
10-1. Adjusting the needle bar height ......... 30
10-2. Adjusting the needle bar lift
amount .................................................. 30
10-3. Adjusting the driver needle guard ..... 31
10-4. Adjusting the needle clearance .......... 31
10-5. Adjusting the shuttle race thread
guide ...................................................... 31
10-6. Adjusting the thread take-up
amount .................................................. 32
10-7. Adjusting the movable knife ............... 32
10-8. Adjusting the button clamp lift
amount .................................................. 34
10-9. Adjusting the holding pressure .......... 35
10-10.Adjusting the position of the
button holder ........................................ 35
10-11.Adjusting the needle up stop
position ................................................. 36
10-12.Adjusting the thread wipper ............... 36
10-13.Checking the input sensor and
DIP switch input ................................... 37
10-14.Checking the input voltage ................. 38
10-15.Clearing all memory settings ............. 38
10-16.Moving stitch patterns ......................... 39
11.USING THE COUNTERS .........................
40
11-1. Using the bobbin thread counter ....... 40
11-2. Using the production counter ............ 40
12.CHANGING FUNCTIONS USING
THE DIP SWITCHES ................................
41
12-1. Operation panel DIP switches ............ 41
12-2. Setting the presser mode ................... 41
12-3. DIP switches inside the control
box ......................................................... 42
12-4. Using user programs ........................... 43
13.CHANGING SPECIAL FUNCTIONS
USING THE MEMORY SWITCHES ........
45
13-1. Using the cycle sewing function ........ 47
14.TABLE OF ERROR CODES ......................
49
15.GAUGE PARTS LIST ...............................
51
16.TROUBLESHOOTING
................................. 52
17.OPTIONAL PARTS
....................................... 55