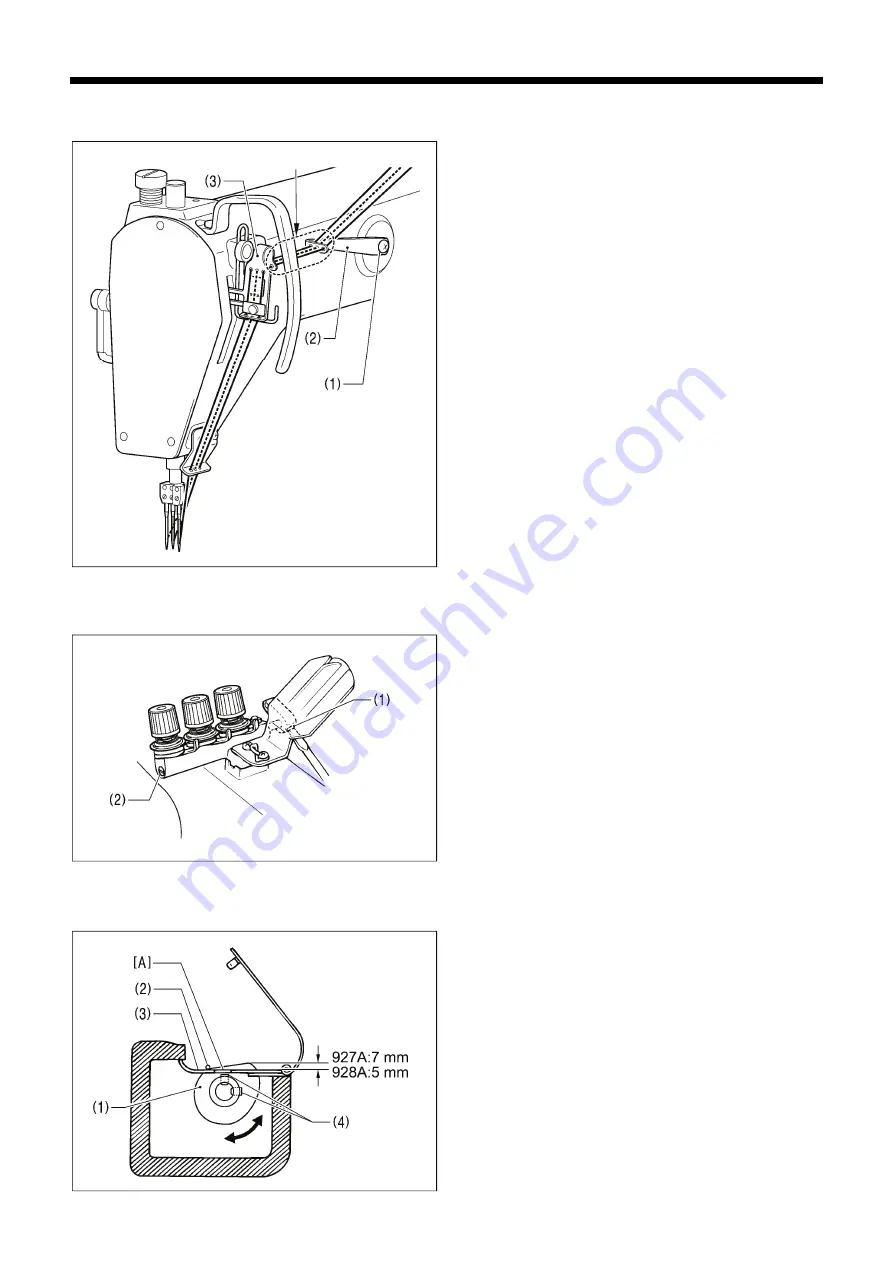
9. STANDARD ADJUSTMENTS
DA-927A, DA-928A
23
9-8. Adjusting the upper thread guide
1. Turn the machine pulley toward you to move the needle to
its highest position.
2. Loosen the screw (1), and then adjust the upper thread guide
(2) so that the upper thread is almost horizontal from the
upper thread guide (2) to the upper thread take-up (3).
3. After adjusting, tighten the screw (1).
* When the upper thread guide (2) is move up, the thread
tightening improves.
9-9. Tension release shaft adjustment
Adjust the tension release shaft so that the tension discs loosen
when the presser foot is raised and tighten when the presser
foot is lowered.
1. Loosen set screw (1).
2. Make an adjustment by turning the tension release shaft (2)
so that the tension discs begin to loosen when the presser
foot rises 1 - 3 mm above the top of the needle plate.
3. After the adjustment, retighten the set screw (1) securely.
9-10. Lower thread take-up timing adjustment
Adjust so that the lower thread take-up (1) touches the thread (2)
when the looper starts its backward travel.
1. Insert the screwdriver through the adjusting hole [A] in the
lower thread take-up base (3), and loosen the two set screws
(4).
2. Turn the machine pulley to raise the needle bar to its highest
position.
3. Raise the lower thread take-up (1) 7 mm [for the 927A] or 5
mm [for the 928A] above the lower thread take-up base (3).
In addition, adjust so that the clearances at left and right are
approximately equal.
4. After the adjustment, retighten the two set screws (4)
securely.
4334B
Thread should be horizontal
4333B
4281B
Содержание DA-927A
Страница 6: ...DA 927A DA 928A v 4284B Oil tank ...