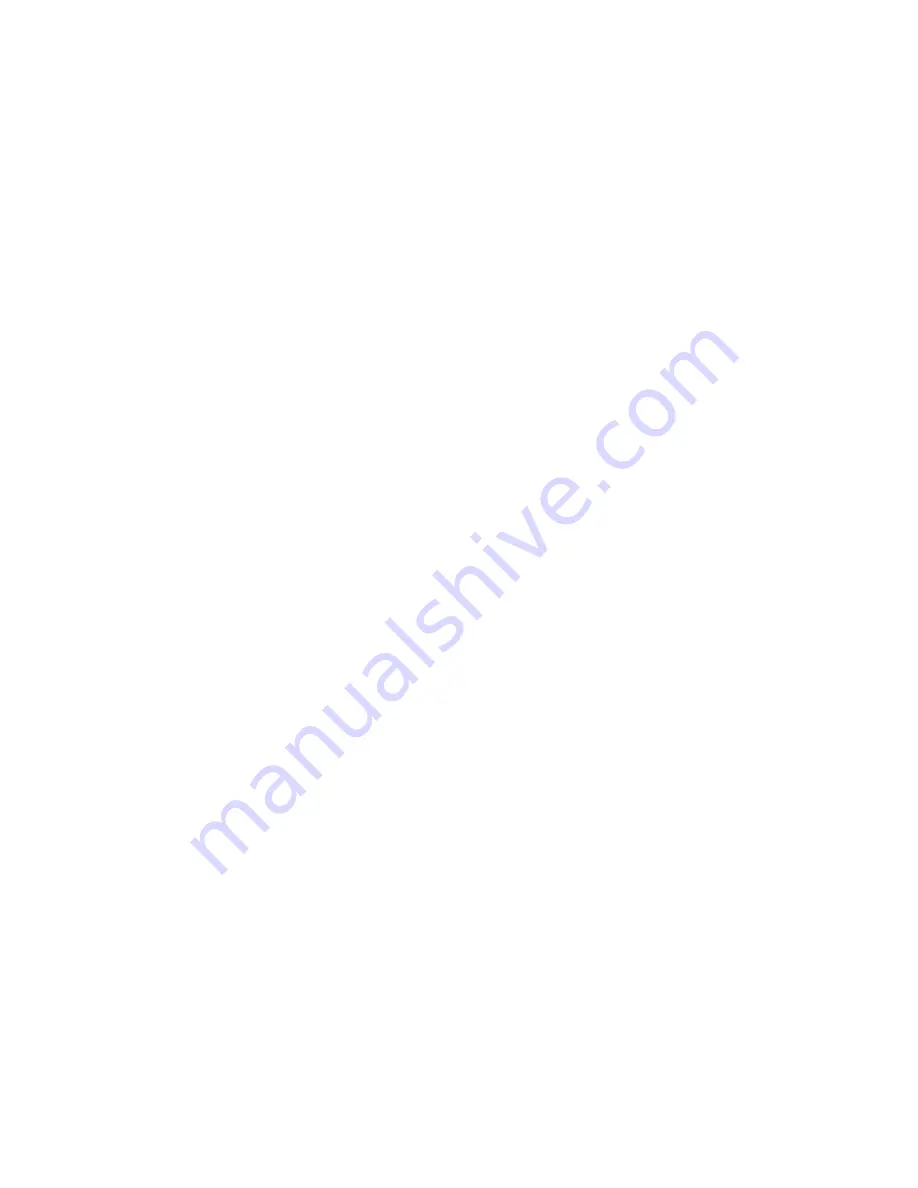
PRINTED IN USA
COPYRIGHT
2018
P/N 990-30265
BRODERSON MFG. CORP.
LENEXA, KANSAS 66215
OPERATION AND
MAINTENANCE MANUAL
IC-600-A
OWNER:_______________________________________________________________________
_________________________________________________________________________
_________________________________________________________________________
SOLD AND SERVICED BY:________________________________________________________
___________________________________________________________
___________________________________________________________
MODEL NO. ___________________________SERIAL NO.
______________________________
Содержание IC-600-A
Страница 6: ...1 2 IC 600 A DIMENSIONS ...
Страница 7: ...1 3 IC 600 A TURNING DIMENSIONS ...
Страница 15: ......
Страница 35: ...2 20 CAPACITY CHART CRANE CAPACITY VALUES ENLARGED ...
Страница 36: ...2 21 CAPACITY CHART METRIC CRANE CAPACITY VALUES ENLARGED ...
Страница 49: ...2 32 ...
Страница 58: ...3 9 IC 600 A LUBRICATION CHART ...
Страница 59: ...3 10 IC 600 A LUBRICATION CHART ...
Страница 60: ...3 11 IC 600 A LUBRICATION CHART ...
Страница 76: ...3 27 JIC HYDRAULIC SCHEMATIC ...
Страница 88: ...3 39 BOOM CHAIN ADJUSTMENT ...
Страница 95: ...1 W I R I N G IC 600 A WIRING DIAGRAM ...
Страница 96: ...2 W I R I N G ...
Страница 97: ...3 W I R I N G ...
Страница 98: ...4 W I R I N G ...
Страница 99: ...5 W I R I N G ...
Страница 100: ...6 W I R I N G ...
Страница 101: ...7 W I R I N G ...
Страница 102: ...8 W I R I N G ...
Страница 103: ...9 W I R I N G ...
Страница 104: ...10 W I R I N G ...
Страница 105: ......