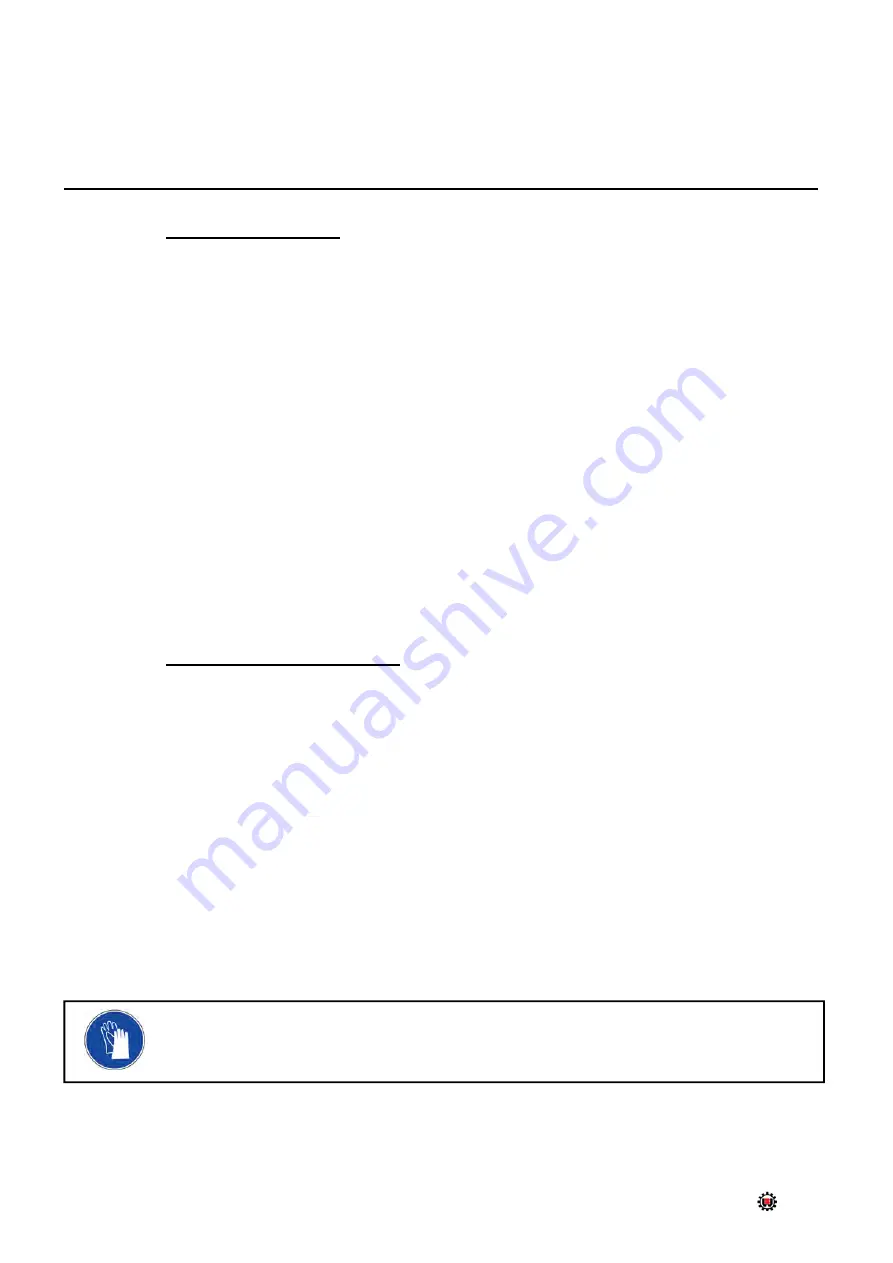
Brobo Group
brobo.com.au
CHAPTER 5 – Maintenance & Selection of Consumables
5.1. Role of the Operator
The person operating & maintaining the
Brobo Group
PEDESTAL GRINDERS PG350
must familiarise themselves
with these instructions for their own safety & that of the others, in addition to safeguarding the production of the
machine. Responsibility must be taken by the user on the general maintenance & up keeping of the unit as specified
in this chapter, with particular emphasis on:
Check to ensure that other operators of the machine always aware of & comply with the relevant safety
instructions & standards as specified in
Chapter 2
- Safety & Accident Prevention
. Therefore, check that
the safety devices are operational & work perfectly & that personal safety requirement is complied with.
Ensure that the working cycle is efficient & guarantees maximum productivity, inspect the:
o
Functions of the main components of the machine
o
Grade of buffing mops &/or grit on the grinding wheel
o
Correct working parameters for the type of material being ground
Verify that the quality of the ground material meets the requirements & that the final product is free from any
machining defects.
5.2. Maintenance Requirements
All maintenance must be carried out with the power switched off & the machine in emergency stop condition.
To guarantee for optimum operation, all spare parts must be
Brobo Group
originals.
On completion of maintenance works, ensure that the replaced parts or any tools used have been removed
from the machines before starting it up.
Any behavior not in accordance with the instructions for using the machine specified in this manual may
create hazards &/or safety risks for the operator.
Therefore, read & follow all the instructions for use & maintenance of the machine & those on the product
itself.
WARNING – SAFETY GEAR
Protective clothing, safety glasses and gloves should
always
be worn while loading parts,
operating the machine, or undertaking any maintenance work on the machine.
Содержание 3220020
Страница 19: ......